External insulation of the building can significantly reduce energy losses and save on heating. This method requires the use of a durable and moisture-resistant material. The cost of thermal insulation should not constitute a significant part of the budget foreseen for construction. Experts recommend that the walls be insulated with polystyrene foam, while it's easy to do the work yourself. Plates of expanded polystyrene are characterized by low thermal conductivity, strength and durability. To install the insulation has a tangible effect, it is necessary to strictly observe the installation technology.
Polyfoam - a universal insulation, it can be used on any part of the outer walls of the house from the foundation to the roof. It is a white plate with a pronounced granular structure. The closed gas-filled pores constituting the basis of the material provided him with optimum performance characteristics:
- thermal conductivity - 0,038-0,042 W / m * K;
- density - 15-40 kg / m3;
- water absorption - 2% of the volume;
- operating temperature - from -55º C to + 75º C;
- the coefficient of vapor permeability is 0.05.
The material is environmentally safe, it does not have toxic emissions. Its surface is not exposed to mold and fungi. The low weight of polymer products facilitates transportation, installation by one's own hands and load on the structure.
Polyfoam is produced with the following parameters of the plates: 100 × 100 cm, 100 × 50 cm, the thickness is 1-10 cm. To effectively insulate the walls from the outside, a material with a thickness of at least 4 cm is required.
The strength and durability of the foam depends on its density, the higher this value, the more reliable the heater. External insulation of the walls assumes an increased load in the form of a finishing layer of plaster, therefore plates with a density of 25-35 kg / m3 will be required. The democratic price of expanded polystyrene has made it the most popular heat insulator in private housing construction.
Disadvantages of using foam plastic
Choosing which insulation to install outside the walls, you need to learn all the pros and cons. Foamed polystyrene plates have several disadvantages:
- high flammability class - G3-G4, the material is easily ignited, it gives off toxic gas during combustion.
- damage to the structure by solvents and paint;
- an attraction for rodents.
High fire hazard is compensated by placing the insulation under a layer of non-combustible mineral finishes or decorative siding.
Extruded polystyrene foam - differences and similarities of materials
Extruded polystyrene foam (EPSP) is a fine-pored insulation with a homogeneous and dense structure. This kind of foam plates has the best resistance to moisture, fire, mechanical impact. The edges of sheets of individual grades of insulation are made with a sample. This design reduces the likelihood of cold bridges. The thickness of the plates is 20-50 mm, they are recommended for mounting under siding. The cost of EPS is 1.5-2 times higher than that of foam, so what kind of insulation is better - each customer decides individually.
Calculation of materials for thermal insulation
Plates of foam plastic have a convenient size of 1 × 1 m and 1 × 0.5 m, which means 1 square meter. m and 0.5 square meters. m, respectively. The number of products must correspond to the value of the area. To the estimated amount of materials it is better to add 10% to the fit. The size of the mesh for reinforcement is also equal to the area of the walls of the house.
Fastening of foam plastic is made with plastic dowels, on each sheet it is required 5 pieces. Quantity of glue and plaster mixture depends on the thickness of the applied layer and the manufacturer. On the packaging of the formulations, there is always an expenditure net.
The procedure for the insulation of walls with polystyrene foam
Preparation of the surface for thermal insulation
Universal insulation foam is suitable for installation on any surface of the house: brick, concrete, cinder block. The preparation of the surface of the walls is divided into several stages:
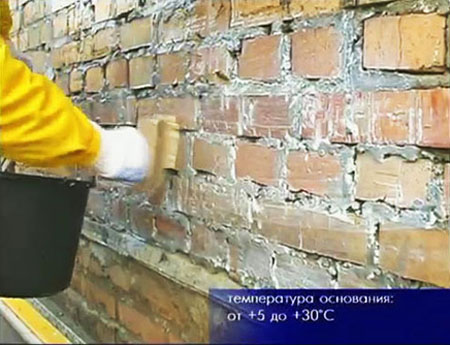
Installation of tin and slope insulation
Secure the ebb on the plastic window before installing the heater. It is mounted so that the edge protrudes beyond the finished wall by 3-4 cm. This arrangement protects the finish of the house from the draining rain water. Simultaneously, the slopes of the windows are insulated. For this purpose, a distance of 2-3 cm is provided. The facade heat insulator will not work because of excessive thickness, it is necessary to use a thinner material. The docking with the general warming of the outer walls will be facilitated by the protuberance of the foam plastic by 1 cm.
Ways of installing foam plastic
Technology of insulation of walls with foam plastic from outside offers several ways of fixing the plates on the walls with your own hands:
- Glutinous - a universal or special composition is used for gluing polystyrene foam, for example, Ceresit CM 83. The dry mixture is poured into a bucket of cold water and mixed with a construction mixer or a drill with a nozzle.
- Nailing - apply plastic dowels with a wide bonnet, they are called "umbrellas", "fungi" or bowl dowels. The metal or polymer insert is clogged inside the fastening. One plate requires 5 pieces - 4 - at the edges and 1 - in the middle.
- Combined - the most reliable and common method, it combines the two previous methods.
Order of fixing dowels
Foaming plastic foam
To do the work yourself will need:
- spatula 80 mm;
- large spatula 200 mm;
- mortar bucket;
- mixer;
- level.
A special adhesive dry mix of Ceresit CM 83 is diluted in a bucket according to the manufacturer's instructions. The consistency of the solution should not be liquid, otherwise the foam sheets will go down, and excessive density will make installation difficult. A normal consistency can be selected after the first knead. Do not mix a lot of solution at once, it can harden to full capacity.
Apply the mixture using two spatulas - small it is recruited from a bucket and stacked on a large one. Apply glue to the EPS board or to the wall of the house. The first method is recommended in the presence of a flat surface without significant differences. The solution is dashed by a dashed line along the perimeter of the plate, with an indentation from the edge of 2-3 cm. In the central part, arbitrary blobs are sprinkled in the amount of 6-8 pieces. Minus method - weighting of foam, installation of the entire insulation requires significant work.
If the wall is a curve, then the thermal insulation will not fit well. Correction of unevenness allows the application of the adhesive mixture directly on the surface to be insulated. Using this method, the thickness of the solution is changed, decreasing or increasing it at different sites.
Mounting and docking of plates
The process of warming the outer walls of the house with foam begins with the installation of the starting plate. It is installed along the entire perimeter of the building with the help of anchors or dowels. The horizontal fixing is checked by level. The profile will allow to keep sheets of a heater from sliding down to drying of a glutinous mix.
Mounting the plates with your own hands starts from the bottom of the corner of the house. After applying the adhesive mixture, the heater is pressed against the wall and leveled. The plane is controlled by applying the level. Plates are stacked with dressing, using the method brickwork. The joints must remain dry, without glue. Filling the entire surface of the heater outer wall, it is left for 3 days to dry.
Fastening with plastic dowels
Belleville dowels - universal and convenient fasteners. With their help, the foam is reliably held on the outer walls, allowing the application of a layer of plaster or the installation of siding. The length of this "fungus" should exceed by 4-5 cm the thickness of the insulation to ensure a strong attachment with the supporting structure. To install a plastic dowel in a foam plastic and a perforator, a hole is drilled with a reserve of 2 cm. The fastener is inserted without a nail and clogged level with the surface of the thermal insulation. With a heater it is better to use a plastic core, it will eliminate the appearance of a cold bridge. If the nail protrudes above the dowel head, it must be cut off. "Fungi" are placed in two ways:
- on the surface of one slab.
- one in the center, the rest at the joints of adjacent sheets of foam plastic.
Which of the schemes is better, each solves independently, but experts recommend the second method. In this case, the fastener clamps the joints, and the plates are closer to the wall.
Processing of seams and fastening points
After nailing all the foam, inspect the joints of the plates, if there is more than 5 mm gap between them, it is poured with mounting foam. When the foam solidifies, the protruding part is cut. The holes from 2 cm or more are filled with polystyrene cuttings. When protruding one of the polystyrene plates at the junction, the protrusion is removed with a float. When using EPPA, the joints are corrected with a construction knife.
Joints of plates and hats plate dowels shpaklyut glutinous mixture, trying to wipe all the irregularities.
Reinforcement of insulation
To reinforce the insulation of the outer walls of the house you will need a fiberglass mesh and a special mixture, for example, Ceresit CT 85. The entire surface of the thermal insulation is applied with an adhesive mass. The reinforcing mesh web is spread over the surface without folds and is put into solution. Neighboring strips are stacked with an overlap of 5-7 cm, at the corners grid is wound on the adjacent wall. To strengthen the corners, the use of a perforated metal corner is effective. The solution is imposed by a wide spatula in a layer of 2-3 mm. Applying the mesh parts, leave the dry area to 10 cm. It is smeared with the reinforcing mixture when applied to the next piece of the mesh. After the composition has dried (1-2 days), the surface is mashed by hand and a leveling coat is applied.
Finishing of external wall insulation
The aesthetic appearance of the house can be achieved by applying a decorative layer of plaster. Before finishing finish the surface is treated with a primer. Further putty putty for painting or decorative plaster. After the outer walls are insulated, the finishing material can be mounted on them.
Features of the insulation of a brick wall under siding
Thermal insulation of the house with foam is often performed under metal or vinyl siding. Installation of heat insulation boards in this case occurs after installation of a frame from a tree or a metal profile. The choice of material depends on the climatic conditions - in dry conditions the tree will last a long time, for wet - the galvanized profile is preferable. The size of the crate depends on the thickness of the insulation, it is usually 50 mm. Polyfoam is fixed between vertical guides using glue and dowels. The installation technique is similar to that described above. Places of joints are smeared with building mortar. In cold regions it is recommended to lay the insulation in two layers.
On top of the layer of thermal insulation, a membrane is tightened, protecting from wetting and wind effects. Between it and the foam plastic leave an air gap created by stuffing the crate. At the top of the protective sheet you need to mount your own crate under the siding. Its installation is carried out according to the manufacturer's instructions.
In contact with
How to insulate the walls with foam plastic from the outside
If the walls of the house can not hold the heat, then no state-of-the-art heating systems will not be able to heat it. At a lowered temperature, the humidity rises sharply in the room and the fungus and mold rapidly develop, affecting not only things and furniture, but also the building itself. Specialists claim that up to 30% of heat is lost through the walls, so you should take care of their warming in time.
Features of work with polystyrene foam
Polyfoam is one of the most popular and inexpensive materials. It is an excellent heat insulator, is not afraid of moisture, does not rot and is easily cut with the help of simple tools. However, this material very quickly loses its properties under the influence of ultraviolet, so the walls, covered with polystyrene, are never left open.
Another significant drawback of foam is flammability. That is why it is used most often in so-called systems of a "wet" facade, when the layer of foam is covered with a layer of plaster fixed on the reinforcing mesh. This technology has become very popular due to its simplicity and low cost.
Important! Any tree can absorb and evaporate moisture, i.e. "breathe". Polyfoam has a low water vapor permeability, so for sheathing wooden house not applicable. In this case, it is better to use glass or basalt cotton wool.
Finishing the house with polystyrene with further plaster coating ("wet" facade system)
The system of "wet" facade with a decorative layer of plaster
Consumables
For the plating of walls with foam plastic you will need:primer: saving here is inappropriate, it will not only reduce the consumption of glue and will prevent the development of the fungus, but also strengthen the surface and improve grip;
warmer: when laying the foam part of the plate goes to the undercut, so 1 square. m of the facade will need about 1.05 square meters. m of foam; its thickness depends on the climatic zone;
glue;
6 mm dowels for fixing the profile;
dowels-umbrellas ("fungi"): on 1 square. m need 5-8 pieces;
basement (for the bottom of the wall) and angular profiles;
reinforcing mesh: 1.35 square meters. m per 1 square. m of the facade; it is better to take a grid with a density of 140-160;
knife for cutting foam;
building level;
putty knife;
plaster: its consumption is indicated on the packaging, but it should be noted that 10% more will be used for the processing of the slopes;
paint for facade works;
forests, stairs, construction goats or platforms.
Wall Preparation
Even an ideally placed thermal insulation material will not help to avoid heat losses in the presence of open air channels. Therefore, before starting work, all the cracks should be carefully plastered or poured with mounting foam. To allow the solution to penetrate inside, they are preliminarily expanded to the desired size.To detect delaminated areas of the wall, you should tap. Crumbling plaster, layers of soot and mold are removed using a metal brush. You can also use a special nozzle on the bulgarian. In order for the foam to lie flat, too protruding parts of the wall are knocked down. Greasy stains are treated with a solvent. On painted walls of oil paint to improve the adhesion, it is better to make small incisions with an ax.
Priming of walls
Concrete and brick walls it is better to treat with epoxy compounds for outdoor work, which can penetrate deep into the surface of the walls. For their priming, it is possible to use mineral acrylic mixtures for facades of buildings, which provide good adhesion.
Wall priming
Selection of glue
You can glue the foam to any walls: concrete, brick, plywood, etc. Before starting work better check the quality of the glue. To do this, it should be smeared with a small sheet of paper, squeeze it for a few seconds against the wall and leave until completely dry. If after drying the foam is badly torn off the wall and there are small pieces on it, the glue is of high quality and is chosen correctly.Important! Carefully read the instructions for use: the adhesive must be frost and moisture resistant.
For work with polystyrene, you can take any facade adhesives, silicone sealants or liquid nails. For intertwining seams use a mounting foam. The composition for fixing the foam should not contain organic solvents (acetone, gasoline, ethers, etc.).
The most suitable adhesive is special composition for sticking foam. There are several of its varieties:
1. Universal for foam, which is suitable for both gluing and reinforcement.
2. Adhesive for gluing. It has a high plasticity and tackiness, when used, sheets of foam do not slip during drying.
3. Adhesive for reinforcing the foam: it has high strength, but less plasticity.
Foaming plastic foam
Layout of walls
Angulation in corners is not always possible, because they can have minor deviations. Marking is best done in the old grandfather way: with the help of plumb lines (lighthouses). To the string, hung on a dowel at a distance of 5-7 mm from the wall, the cargo is tied. After he stops swinging, the twine is fixed.If irregularities are found that do not allow the string to be laid flat, they must be knocked down. On the "failure" of the wall can be applied glue or construction foam. Transverse (horizontal) markings can be applied by means of a hydro level and twine.
Aligning the wall to lighthouses
Setting the start profile
To support the plates in the lower part of the wall is fastened a metal profile. In addition, it is able to protect the styrofoam from mice that like to settle in a foam plastic.The size of the profile is chosen according to the thickness of the insulation. The fixing is made by 6 mm dowels with washers with an interval of 30-40 cm. The angles of the profile are joined by the method of oblique cuts or by means of a corner connector.
Fixing the starting profile
Methods of applying glue
You can paste a sheet in the following ways:when not smooth walls it is better to apply a sufficiently large layer of glue along the perimeter of the sheet, as well as in several places along its center;
with a spatula with teeth spread the glue a small layer evenly throughout the sheet, in this way the foam is applied on even walls;
Special glue for polystyrene, sold in cylinders, is applied around the perimeter and center of the sheet.
Warming of foam plastic
Before starting work walls must be dry. If glue foam on wet, not dried after the winter wall, the glue joint will be fragile. When working in summer heat, the differences in daytime and nighttime temperatures will not have the best effect on the strength of the glue composition that has not dried out yet.All work should be done in the spring, about a week after the heating is turned off in the houses. You can glue the foam in the fall, when the temperature of the surrounding air drops to + 17-18 ° C. Do not start work and in warm windy weather, because the glue will grasp too quickly.
It is not recommended to use too brittle foam in work: it is better to choose a material with a density of 20 kg / m3. Thermal insulation of denser sheets is less, so it is better not to use them for insulation of external walls.
Finishing order
You can start sticking foam after a day after applying the primer. Plates are stacked long side of the sheet down, starting at the bottom corner. The second row should go with an offset, as when laying a brick (see photo). To do this, the first sheets of odd rows adjacent to the corners are cut in half. The most convenient are slabs measuring 0.5 × 1 m and a thickness of 5 cm.
The gaps between the sheets are filled with foam. Too large gaps can be sealed with polystyrene chips.
The scheme for gluing foam plastic
Additional Fixation of Polyfoam
For this, umbrellas are used - special dowels for foam plastic, having a plastic head. Their length is selected taking into account the thickness of the plates. Metal fasteners that can damage brittle plastic are not used. In addition, the metal has a different coefficient of expansion.
Dowels for foam plastic
To install dowels in the wall, pasted with foam, holes are made of the appropriate depth, into which dowels are inserted. They must enter into the foam plastic for 1.5-2 mm.
Dowel holes
The fastening of umbrellas is made by an envelope: at the corners of the leaf and in the center. Thus, to fix each sheet you need 5 dowels. The dowels must enter a concrete base to a depth of 50 mm, into a brick wall of 90 mm. For example, with a width of 8 cm of polystyrene, "umbrellas" measuring 13-17 cm are used. After inserting them, they are additionally pinned with a rubber hammer so that each of them is drowned in a foam for a couple of millimeters.
Creating a decorative protective layer
After a day after laying the foam, it is leveled with a float. The corners of the house are additionally protected with reinforced mesh with a corner. It is attached to the glue and pressed tightly against the joint with an angled spatula.
Grouting of foam plastic
Important! Do not leave the walls insulated with polystyrene, without finishing for a long time. Even after 2 weeks, ultraviolet rays are already capable of damaging its top layer. If this still happened, the damaged surface is removed using a float, and only then the wall is lined with a mesh.
Armored corner and corner spatula
The reinforcement of the walls insulated with foam is made using a grid with cells of 3-5 mm. The grid is cut into strips of the desired width. On the wall is applied a special adhesive for reinforcement so that the mesh is buried in it. Its edges are fixed in the last turn. After fixing the mesh on the wall with a spatula, it is leveled and the excess glue is removed. Too much of its layer can lead to cracking.
Overlapping reinforced mesh
The second layer of glue is applied only after the first one dries. The reinforced layer after 3 days is primed, plastered, and then a layer of facade paint is applied to the wall.
With all the undeniable advantages of a brick, he still has one significant drawback: high thermal conductivity. Therefore, houses built of this material, need high-quality insulation. For each structure of bricks, it is necessary to make a heat engineering calculation. That is, to find out what the required design resistance is for the building envelope. This will help to perform high-quality insulation brick house outside and inside.
What materials are used to insulate a brick house outside
The developer should focus on three basic rules of heat engineering:
- External insulation is more effective than internal insulation.
- The increase in the vapor permeability coefficient of the materials constituting the wall pie should be directed from the inside outwards.
- For the full insulation of the enclosing structures, it is necessary to perform a set of corresponding works on both sides of the wall.
The scheme of warming the brick house outside
There are three types of heat insulators, which are optimal for the insulation of walls, built of bricks. This is extruded polystyrene foam, polystyrene, mineral wool (or other fibrous materials with similar properties).
Extruded polystyrene foam
Extruded polystyrene foam (EPSP) has the lowest thermal conductivity among those materials that are suitable for making an interior and exterior brick house. EPSP is manufactured by pressing and has a significantly higher density than the foam.
Styrofoam and Penoplex
Polyfoam is the most popular heat insulator for brick walls. It can be used for both types of insulation: external and external. The optimum thickness of the plates is determined with the help of heat engineering calculation, which can be done with the help of the Teremok program or the "Thermal Technical Calculation Online" service.
According to GOST 15588-86, 4 grades of foam plastic are produced: PSB-15, PSB-25, PSB-35 and PSB-50. The developer should be aware that the standards do not envisage the letter "U" - improved or "F" - facade. The presence in the trade network of material with marking of this kind is caused by the desire of the producer to interest the buyer.
Important: In choosing a foam for warming the brick house from the outside and from the inside, you need to pay attention to the figure in the marking. The lower it is, the higher the thermal conductivity of the material.
There is an improved modification of polystyrene. This material has a lower thermal conductivity. It is more profitable to make the insulation of a brick house with foam by means of penoplexes in terms of cost savings, since it becomes possible to use slabs of lower thickness. So, reduce the cost of buying a thermal insulator for exterior walls.
Mineral wool
There are two main types mineral wool: stone (basalt - basalt, limestone, dolomite) and slag (base - slag of non-ferrous and ferrous metallurgy). Any of these fibrous materials, on average, has the same thermal insulation properties as polystyrene foam. For example, the thermal conductivity of mineral wool with a layer thickness of 167 mm is 0.039 W / m ° C. A foam at a thickness of 159 mm - 0.037 W / m ° C.
But minvats have one significant drawback: high hygroscopicity. When wet, it is not capable of performing the function of a heat insulator. Therefore, in regions where the air humidity is increased, it is more profitable and more reasonable to make the insulation of the brick house from the outside or EPS. but good as a heat insulator for the internal walls of the building.
How to insulate a brick house, if the facade of a siding
If siding (not important, vinyl or metal) is chosen as the facing material for the exterior walls of the house, the best insulation in this case is foam or EPS. Since the second one has a higher price, the first one is the most popular.
Ways of facade insulation under siding:
- gluing foam plastic;
- fixation with special fasteners.
The technology of gluing foam to the outer walls
Warming of a brick house with foam plastic for siding with gluing is the best choice for brick buildings. The reason for this is the less laboriousness of the process and the higher speed of work.
Important: The developer should be aware that the fixation of the foam plastic by gluing is possible if the exterior walls of the brick house are flat.
Stages of work
- The surface of the wall is cleaned of dirt and, if necessary, leveled.
- Produce treatment with a primer of deep penetration.
- In the lower part of the wall, a horizontally mounted strip is attached, which will serve as a support for foam or Penopolix cloths during the gluing process.
On the surface of foam plates (Penoplex) rolled needle roller.- On the perimeter and center of the expanded polystyrene sheets, a layer of glue is applied. You can use glue foam for work with foam PENOSIL, polyurethane adhesives in cylinders, dry mixes Ceresit CT-85, Weber Vetonit, Bergauf Isofix, Perfect Thermo or similar. Any of these compounds allows you to perform quality insulation of the brick house from the outside with foam under the siding.
- First row of plates heat insulating material fixed with support on a horizontal rail.
- The second row of plates is staggered in relation to the first.
- Post-conglutination glue mount siding.
Important: To fix the foam on the exterior walls of a brick house, it is not recommended to use a cement-sand mortar. It is not able to provide the proper level of adhesion of the binder and heat insulator.
Technology of fixing foam to external walls with fasteners
The facade of a brick house insulated with foam
Thermal insulation of a brick house under siding with its own hands can be done with the help of special fasteners: dowels with wide hats. This method is more reliable, but it takes a lot of labor.
Stages of work
- The surface of the wall is cleaned of dirt. Alignment, if there are no large differences in altitude, is not required.
- Install the starting guide (horizontal rail) in the lower part of the wall and beacons from the tensioned cords (serve as a guide during the laying of plates).
- Vertical racks from a metal profile or wooden bars are exposed, the step between which should correspond to the width of the thermal insulator sheets.
- Fasten the foam or Penoplex sheets each with 5 dowels: four in the corners and one in the center.
- Mount the siding.
We warm brick walls with foam and plaster
Use for plastering the exterior walls of a brick house plastered foam - an economically profitable way to make a warm and aesthetically attractive facade. The work uses special prizes: Ceresit, Ecomix, Stolit and others with similar properties.
Important: The insulation of the brick house with polystyrene for plastering is done using a PVC mesh, as this material is resistant to alkali. Optimal choice - grid for facades with a density of 140-160 g / m2.
Stages of work
- Starting from the top of the wall, the mesh is fixed to the foam plastic so that its edges are dense to form an overlap of at least 10 cm.
- Work is begun in the finishing of window and doorways.
- Apply the first layer of plaster thickness 0.7-0.7 mm. This work will be more convenient if you hold the upper part of the grid with one hand and place the solution in a direction from the top down. In this process, it is more convenient to use a special plaster trowel, and mesh the "mash" with plaster.
- On solidification of the first layer, the second layer is applied: leveling. Its thickness is not less than 1 cm. A spatula with a width of 35-45 cm is used in the work.
- Apply a priming layer and proceed to finish the plaster: painting or hand-made.
We warm brick walls with mineral wool
Mineral wool is the optimum heat insulator for internal works. Regardless of whether the roll is used material or slabs, internal walls buildings are fastened vertical racks at a distance equal to the width of the woolen cloths. For external work, it is recommended to use compressed plates.
Warming of a brick house outside under the siding requires a ventilated facade. Due to the high hygroscopicity of this thermal insulator between it and the finishing material, it is necessary to leave a gap that will allow moisture to evaporate. In addition, the minivat should be covered with a vapor-tight membrane.
Stages of work
- The supporting wall is attached to the crate.
- They put a heater.
- Mount the membrane.
- Provide ventilation products with a width of 4-6 mm.
- Strengthen the finishing material.
If this way to perform the insulation of a brick house on the outside with a mineral wool under the siding, this heat insulator will serve irreproachably for many years.