When asked which house is the strongest, the answer is obvious - monolithic. And if earlier the technology of monolithic construction was used only for the erection of high-rise buildings or industrial facilities, today it is increasingly possible to find a monolithic cottage or a private house. Such technologies are able to translate even the most amazing design ideas into life, without restricting straightforward designs. In addition to surprising strength, which is enough to withstand a light earthquake, such cottages are popular also because they are quickly and easily built, do not require expensive materials and labor, and are reliable and durable. Walls of monolithic cottages can be finished with any materials without restrictions, and the technology of fixed formwork allows not to equip additional warming of walls.
Monolithic construction of cottages: advantages and disadvantages
Construction on monolithic technology is carried out completely at the construction site by pouring concrete into the formwork. Due to this feature, this technology has its advantages and disadvantages.
To date, monolithic construction is sung such praised dithyrambs, which gives the impression that there are no shortcomings at all, and there can be nothing better than a monolith. Let's figure it out, there are really many advantages:
- Due to the integrity of the monolithic structure, the mechanical strength of the entire building is increased, it is resistant to damage caused by soil displacements, rills and earthquakes.
- The absence of seams in the building box makes the cottage warmer, since there are no so-called "cold bridges".
- Work on the construction of a monolithic cottage can be made at any time of the year, on any ground.
- Fast construction.
- Low financial costs.
- The possibility of curvilinear construction, projects of monolithic cottages can be arbitrarily intricate.
- Provided the use of insulated concrete mortars with additives: expanded clay, perlite, sawdust, slag, etc., the construction becomes easy enough that it would not be possible to equip a heavy buried foundation.
- The walls of a monolithic cottage can be insulated and trimmed with various materials.
- When using non-removable formwork, additional insulation will not be required, and the total thickness of the wall will be reduced. Also, the walls will have exceptional sound insulation.
- Possibility of arrangement of any interfloor overlap: slab, from monolithic concrete, wooden.
- Uniform shrinkage of the building, which eliminates the appearance of cracks.
But it also does not do without a fly in the ointment, disadvantages of monolithic construction:
- For pouring a concrete mixture at a height, a concrete pump (mortar pump) is required. This is not at all a problem if you order construction in the company, and it is costly if you do it yourself.
- When pouring a monolithic slab overlap repeatedly increases labor costs, will require special forests.
- A monolithic cottage with a non-removable formwork, which is also a thermal insulation, is not capable of "breathing" walls, it will be necessary to equip the supply and exhaust ventilation. High humidity in the house.
- Expanded polystyrene, which is used in non-removable formwork, is a non-environmentally friendly material that, although it has a G1 flammability class, means that it dies within 2 minutes, but in the process of decay produces extremely toxic substances, so the mandatory requirement is the plastering of walls from non-removable formwork.
- Time costs for the manufacture of formwork taking into account the features of the project.
- Required grounding for the entire cottage, as the walls are reinforced concrete with metal reinforcement.
Considering which prices and all their advantages are on monolithic cottages, many neglect the shortcomings associated with the non-ecological nature of expanded polystyrene. It is understandable - cheap, fast, beautiful, durable, strong, who will think about your health there? Although it should be noted that if you do not use a fixed formwork, and build walls of warm concrete, and then heat it with more environmentally friendly materials, the cottage will not only be cheap and warm, but also quite comfortable.
Technologies for the construction of monolithic cottages
In total, there are two technologies for building monolithic cottages. They differ only in that in one case the formwork is removed after the hardening of the concrete, and in the other, the formwork is not removable. Both technologies have their own peculiarities and nuances in construction and operation.
Building a monolithic cottage with a removable formwork
Removable formwork is made individually for each project of the cottage, as it must exactly repeat its bends and features. Most often used wood, plywood, plastic or iron.
The width of the empty space between the walls of the formwork should be equal to the width of the future wall, which is calculated taking into account the thermal conductivity of the concrete mixture and the construction region. Shields of the formwork are fastened with the help of washers, studs, nuts. In order to be easy to remove the formwork after pouring concrete, it is necessary to put corrugated pipes on the threaded studs, protecting them from contact with concrete.
The technology of building a monolithic cottage with a removable formwork assumes that it is possible to fill not only ordinary concrete, but also mixtures that have much less thermal conductivity, for example claydite, perlite concrete, cinderblock, sawdust, foam concrete, aerated concrete, arbolite and others. The walls will be much warmer and more vapor-permeable, but they can not withstand too much pressure.
Also important is the reinforcement of the concrete wall. To do this, you can use reinforcing mesh, plastic or steel, and for greater strength - binds the frame from the reinforcement.
Important! The wall, reinforced with a frame of reinforcement 8 - 18 mm, will be quite cold, as the metal parts of the frame will act as "cold bridges".
It is allowed to fill not more than 50 cm of concrete in one pass. Only after he "grabbed" you can continue to fill. Concrete consolidation in the formwork is performed with deep vibrators, special attention should be paid to the corners.
After the concrete hardens, the formwork is removed and rearranged above. So, until the whole cottage is flooded.
For concrete to take maximum strength, it is necessary to allow it to survive for at least 4 to 5 weeks. After this, you can proceed with warming and finishing.
Monolithic walls can be insulated with expanded polystyrene, extruded polystyrene foam, mineral wool, "warm" plaster. In doing so, use the technology of a ventilated or wet facade.
It is also possible a variant of the well facade, when an indent is made outside the concrete wall, then it is covered with a facade brick or tile, and the free space is covered with a heater: expanded clay, eco-wool, etc.
The indisputable advantage of this technology is that the house can be made as much as possible "breathing" and ecological, although it will be necessary to tinker with the assembly and disassembly of the formwork.
Construction of a monolithic cottage with a permanent formwork
The use of non-removable formwork is advertised with enviable persistence and perseverance. After all, according to this technology formwork is not simply not removed after casting of concrete, it is also a layer of thermal insulation. When using this technology for monolithic construction of cottages the price is the lowest, since labor costs are reduced as much as possible.
After the arrangement and waterproofing of the foundation, a formwork is installed on it, which is a form of expanded polystyrene, fastened with special profiles. These molds have a "spike-groove" fastening system, which allows you to connect so tightly and without gaps, that absolutely no leakage of concrete or its cracks in the places of connection forms of formwork.
The width of the foam polystyrene formwork can be different, in the case of a large order, the factory can produce blocks of any desired thickness. The standard is a block in which empty space for concrete is 150 mm wide and on both sides of expanded polystyrene with a layer of 5 - 7,5 cm. This is quite enough for the house to be warm in winter and cool in summer, to include heating only when the temperature drops below +5 ° С.
After the formwork is installed, the concrete is poured into the concrete by a layer of 50 cm and sealed with a deep-seated vibrator.
Important! Please note that for casting permanent moldings, only concrete can be used and warm mixtures should not be used. This is due to the fact that the vapor permeability of expanded polystyrene is negligible and equal to 0.05 Mg / (m * h * Pa), while the vapor permeability of warm mixes is above 0.09 Mg / (m * h * Pa). If you clamp the warm concrete between the layers of expanded polystyrene, it will accumulate condensate, as a result of time, mold and fungus will appear.
After the construction of the walls they do not need to be insulated, simply plastered with decorative plaster or sidewalk.
The advantage of the technology of fixed formwork is the simplicity of erection, cheapness and lack of need for additional insulation. But this cottage is a thermos that can not breathe.
Types of formwork for monolithic construction
In the field of application there are several types of formwork: wall formwork, foundation, overlapping, tunnel formwork, formwork of annular walls with a modified radius. Due to such a variety, monolithic pouring can be used for any element of the building structure.
Various formwork elements are also installed in different ways. The foundation formwork is installed on struts and horizontal supports. Wall formwork - with the help of racks, brackets and connecting locks. Decking for flooring is applied to the structure from telescopic or bulk retaining racks.
Removable formwork is made of such materials: steel, aluminum, wood, plastic. Depending on the material performance has different properties. If you use plywood for the formwork, then it must be cut with a saw with fine teeth, so as not to damage the veneer and lamination. Drilling holes for pipes and cables in the formwork is necessary on both sides, for the same reason. Keep the plywood formwork in a dry place.
Before use, the removable formwork is treated with a special mortar so that it can be removed easily.
Fixed formwork, as already mentioned above, consists of expanded polystyrene, does not require additional processing. Its forms are different: angular, longitudinal, window-sills, nadkonnye and others. In fact, the arrangement of the removable formwork is reminiscent of the combination of figures of the LEGO constructor.
Types of concrete mortars for monolithic construction
The undeniable advantage of monolithic construction is the ability to pour solutions into the formwork with different thermal conductivity and vapor permeability.
Concrete - the simplest option and, unfortunately, the only one permissible when pouring non-removable formwork. The cottage made of solid concrete will be very cold, since its thermal conductivity is 1.51 W / (m * S), and the vapor permeability is 0.03 Mg / (m * h * Pa). Walls of concrete should be carefully insulated.
Reinforced concrete - even colder than concrete, as the iron reinforcement acts as "bridges of cold". The cottage of monolithic reinforced concrete requires insulation with expanded polystyrene, extruded with polystyrene foam or mineral wool.
Expanded clay concrete has a thermal conductivity of 0.66 - 0.14 W / (m * C) and a vapor permeability of 0.09 - 0.3 Mg / (m * h * Pa). The indices depend on the density of the mixture, the larger the porosity of the expanded clay, the warmer and steam-permeable wall. The wall thickness for the Moscow region is 50 cm.
Slag Concrete - the same as keramzitobeton, only instead of expanded clay - slag. It is less durable, so the thickness of the walls should be 55 - 60 cm.
A mixture of cement, sand, sawdust (needles) and water. The walls are obtained by warm, fire-resistant and eco-friendly, only from the outside they need to be protected with waterproofing material.
A mixture of cement, water and wood chips wood 40x10x5 mm. Chips are pre-ventilated or treated with lime. The walls of the arbolite are warmer and stronger than from the sawdust concrete.
Foam Concrete - concrete, chemically foamed, warmer material than ordinary concrete. Its thermal conductivity is 0.29-0.08 W / (m * C), and the vapor permeability is 0.11 - 0.26 Mg / (m * h * Pa).
Monolithic construction of the cottage with their own hands
Usually the construction of a monolithic cottage is ordered in a construction company. This is due to the fact that for the work will need formwork, concrete pump, wood for the slab and other equipment, which is in any construction organization, and buying it for one time is unprofitable.
But for those who do not like simple ways and agree to spend money on a mortar pump, and make an overlapping wooden or order a slab of ceiling and install it with a crane, it will be possible to erect a monolithic cottage with their own hands.
The project of a monolithic cottage can be carried out independently, downloaded on the Internet or ordered by a project organization, in the latter case you will make all necessary calculations: the strength of load-bearing walls and loads on them, the necessary thickness of the pouring and insulation.
When the project is ready, we equip the foundation. If the house is on the ground floor, then the plinth can be covered with a monolithic slab, and the foundation - with a strip. Usually, they build a pile-tape foundation and carefully waterproof it.
How to build a monolithic cottage with a removable formwork
Formwork is made of wooden boards with a thickness of 30 - 50 mm. If the temperature in the region drops to -30 ° C, we make the walls 55 - 60 cm thick. We tightly connect them to each other and drive the posts 80x80 mm, at a distance of 1 to 1.5 m from each other. The length of such shields should be 2 - 4 m, and height 60 - 80 cm.
At the bottom we install metal ties with bolts, so that the shields do not burst when the concrete is poured into them. Above the boards are fixed with wooden pads or similar screeds.
Insert a reinforcing mesh or frame into the formwork, depending on the project.
For the production of sawdust, we take: 8 parts of dry sawdust, 1 part of cement M400 - M500, 3 parts of lime, 2 parts of sand.
Important! Sawdust should be at least a year outdated.
First mix cement with sand, separately lime with sawdust, then mix both mixtures and mix thoroughly, adding water slightly. As a result, the water should be so much that it does not flow out of the solution.
The resulting solution is poured a layer of 20 cm into the formwork. We compact it with vibrators and pierce the rods to carefully compact the solution. Then fill in the next layer. And so on until the formwork is practically filled (for convenience we leave 5-10 cm above empty).
It is possible to rearrange the formwork only after 3 to 5 days. All this time, concrete should be sheltered from the sun and precipitation of film or roofing material.
After the completion of the construction of the walls, we give concrete strength for a month, then we equip the ceiling and the roof. Overlapping should go to the walls for a 15 - 20 cm minimum.
After the drying of the sawdust concrete, it is possible to insulate the walls from the outside as needed. To do this, you can use a "warm" plaster, which can be applied to a layer of up to 50 mm. It is an excellent waterproofing, heat insulator and at the same time easily releases steam to the outside.
How to build a monolithic cottage with a permanent formwork
The erection of a monolithic cottage with a fixed formwork is an extremely simple task. First you need to stock up the elements of the formwork. They are wall, corner and radius. It is necessary to calculate the number of each type of elements according to the developed project.
We install a non-removable formwork on the foundation, assembling it as a LEGO constructor, connecting the locking joints of the blocks. To begin with, the first row will suffice.
We carry out all necessary sewer, water and ventilation pipes. Then, if reinforcement is required, insert the reinforcing mesh. We prepare a concrete mortar from cement M500, sand, crushed stone and water. We build the formwork and fill the 50 cm layer, compact it with deep vibrators.
For a day you can increase in height no more than 50 - 70 cm.
After the completion of the construction of the walls, they do not need to be insulated, and as a decoration it is possible to perform a so-called "wet" facade - plaster with decorative plaster on a fiberglass mesh.
The construction of a monolithic cottage with your own hands is much simplified if you call for help a couple of partners. After all, after overcoming a certain height, when building walls for pouring concrete upward, you will need to use a concrete pump. And coordinated actions can shorten time and organize proper work.
Quite often, during construction, special machinery is used. A large selection of spare parts for road-building equipment from leading manufacturers, such as spare parts for Komatsu bulldozers , are presented on the website of the company "Aimashineri".
The construction of modern buildings and structures is carried out mainly on special projects. Buildings of complex configuration are erected from monolithic reinforced concrete. Monolithic structures are formed by pouring concrete into the system of enclosing planes - formwork, which can be made of various materials.
Wall formwork, as a kind of restraint systems, allows you to accurately build the structural elements of the structure without loss of quality. In this article, we'll look at what and how to make a formwork for a monolithic wall.
Wall formwork is a system of shields of different sizes
The purpose of the formwork for walls is to keep the liquid mass of concrete in the desired shape and volume until it is completely solidified.
Materials for fencing must have sufficient strength and reliability, so that, without deforming, to withstand the pressure of the mass of concrete poured. The made frame of fences should be a hermetic construction, not allowing leakage of the solution.
Wall formwork is a system of shields of different configurations and sizes. Materials for wall formwork define the names of fencing types:
- wooden shields;
- building plywood;
- metal shields;
- plastic panels;
- aluminum shields;
- fixed blocks;
- auxiliary material.
The framework of wooden shields for the formation of a monolithic concrete wall is collected from hardwood boards.
When building a low-rise small house, the formwork for walls is collected from the boards and beams by hand.
As materials for the formwork, as a rule, dry edged boards with a smooth surface from 25 mm to 30 mm in thickness are used. The main fastening elements of the formwork are the bars with a cross-section of 50 x 50 mm and 70 x 70 mm.
A tree is a fairly strong building material that can be easily processed. When installing fasteners of wooden boards, it is always possible to make the necessary parts from the man-made lumber.
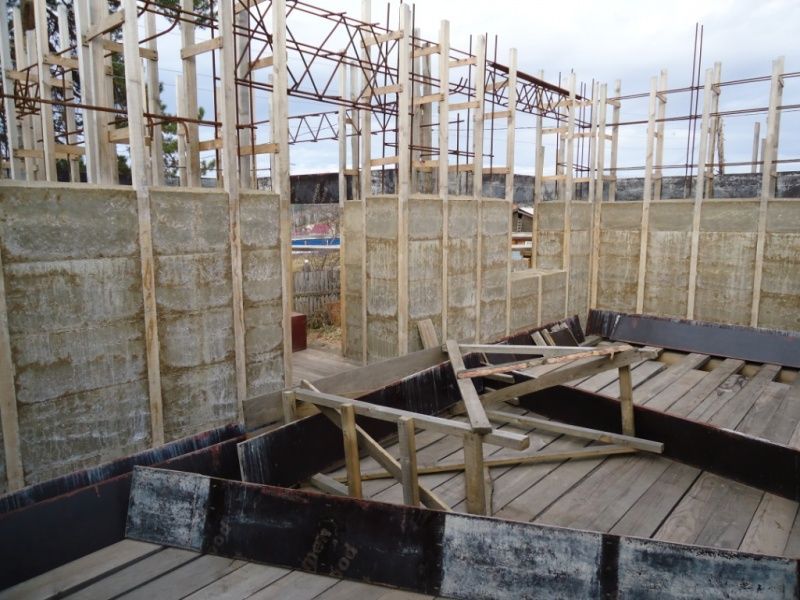
Removable formwork of wooden shields for walls after solidification of a concrete monolith is subject to disassembly.
All elements of the formwork are assembled during the assembly with nails, which fit well into the body of the tree and firmly hold together the details of the structure. Doing this work yourself will not cause great difficulties.
The walls of the house will be smooth if the inner surface of the boards is covered with a polymer film.
When dismantling fences, shields will be easily detached from the monolith without damaging the surface of the concrete.
On the construction of monolithic walls of large objects, wooden shields are not used.
Building plywood
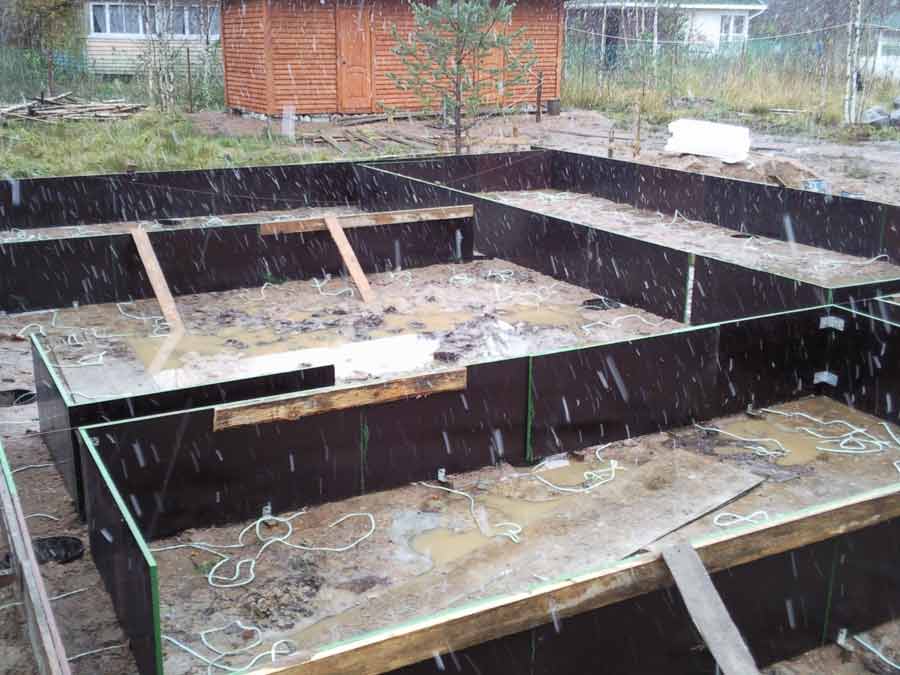
The plywood used for the formwork consists of several layers of hardwood veneer, glued together. The veneer sheets are bonded under strong heating and pressure. Thanks to this, construction plywood has excellent performance.
Absolutely smooth surface allows you to get perfectly even walls. can be reused. The technology of installing the fencing system from this material practically does not differ from the installation of a frame made of wooden shields. The essential difference is that screws are used as fixing hardware instead of nails.
Build your house from monolithic walls with experience in construction is possible, using a formwork made of construction plywood, assembled with your own hands.
Metal shields
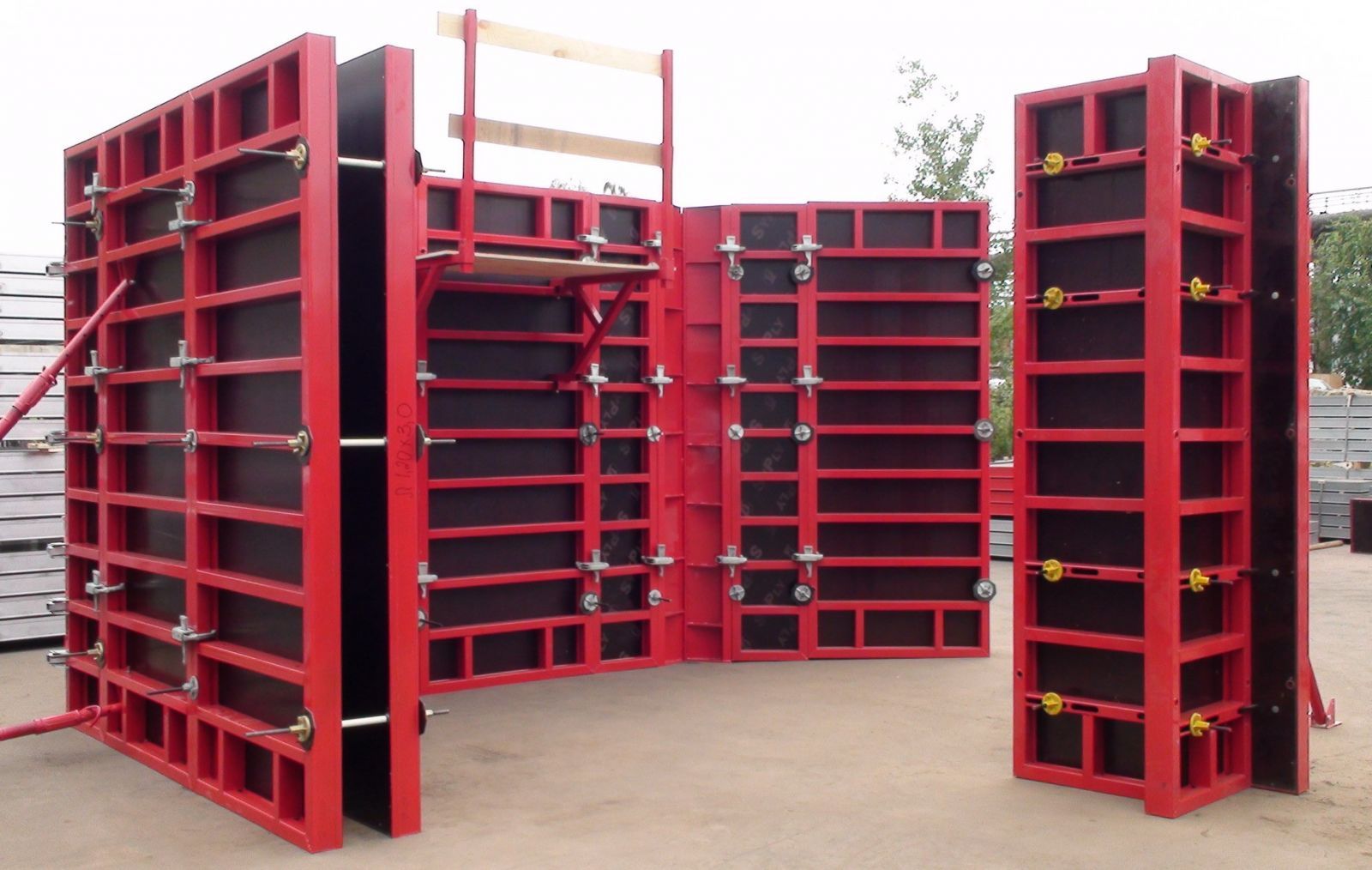
Metal sheets with ribs of rigidity are made in various sizes. Sets of steel shields include a complete set of fixation elements for the enclosing planes in the design position. Locking devices provide sealed joints between steel panels.
Steel shields are used to build walls in large industrial and civil buildings. Large-sized panels are very heavy. Removable formwork of metal shields is mounted using load-lifting mechanisms (tower cranes and truck cranes).
Metal fencing can be of two types:
Adjustable shields
Reinforced formwork made of steel panels allows the construction of high walls in a short time. At a time when the lower tier of the monolith has gained strength, the steel panels are dismantled and installed at a new level.
Metal shields can only be moved by means of lifting machines and mechanisms.
The system of sliding panels is a complex mechanized complex of enclosing structures, consisting of a set of steel elements, lifting devices and rigging devices.
The technology of forming a monolithic wall with the application is that during layer-by-layer formation of a monolith, a number of shields move in the necessary direction to fill the next level of a monolithic wall.
The main disadvantage of steel shields is the corrosion of metal. However, with the timely care of metal fencing will last for many years.
Due to their high bearing capacity, metal shields are used to fill retaining walls that support massive building elements. For information on how to work with sliding formwork, see this video:
Often, to eliminate the threat of destruction of the house, the monolithic structures in the form of a triangular figure with a right angle in the base of the retaining wall are put up against its walls.
For the erection of monolithic walls of his house, the developer can take small metal shields from the building organization for rent. Installing the rented small-piece metal formwork with your own hands will save time and money.
Plastic panels
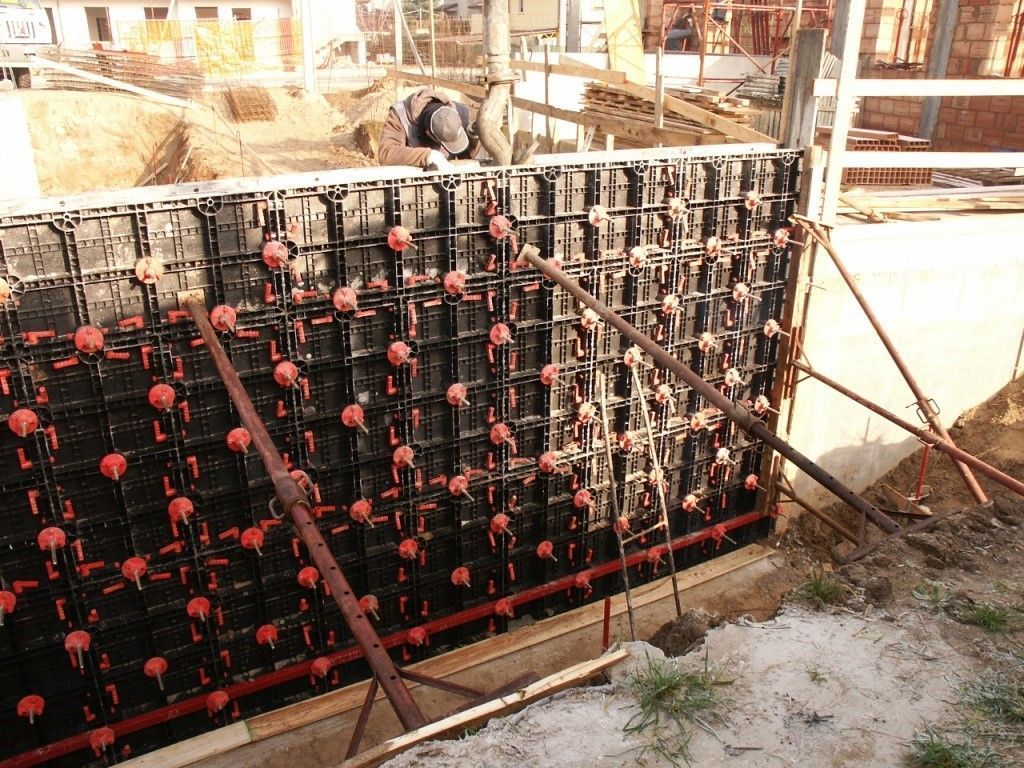
Polymer panels favorably differ from metal shields with their light weight. Shields are designs of reusable use.
Plastic fencing is easily rearranged manually. They are used for pouring monolithic walls of low height.
The outer surfaces of the panels easily deform from accidental shocks.
During installation and disassembly of the plastic frame, you must be extremely careful with the panels.
Plastic panels are not expensive, so they are also profitable to rent.
Aluminum fences
By the way of application, aluminum shields are close to metal formwork. Fencings made of non-ferrous metal are practically not exposed to corrosion and have a low weight. For the erection of walls, the developer can install vertical aluminum fences with his own hands. An example of the use of aluminum formwork see in this video:
The disadvantage of the panels is their high cost. Aluminum structures require careful handling, since they easily deform even from small random force impacts.
Non-removable blocks
Recently, fixed fences have become very popular, which are made in the form of bulk blocks of expanded polymer (polyurethane).
The internal cavity of polymer blocks is poured with a concrete mixture. The surface made of polyurethane becomes part of the walls. The side surfaces of the walls are painted or covered with decorative facing material.
Polyurethane itself is an excellent heat insulator. Walls with such a polymer coating are good at keeping the indoor temperature in the winter.
Auxiliary material
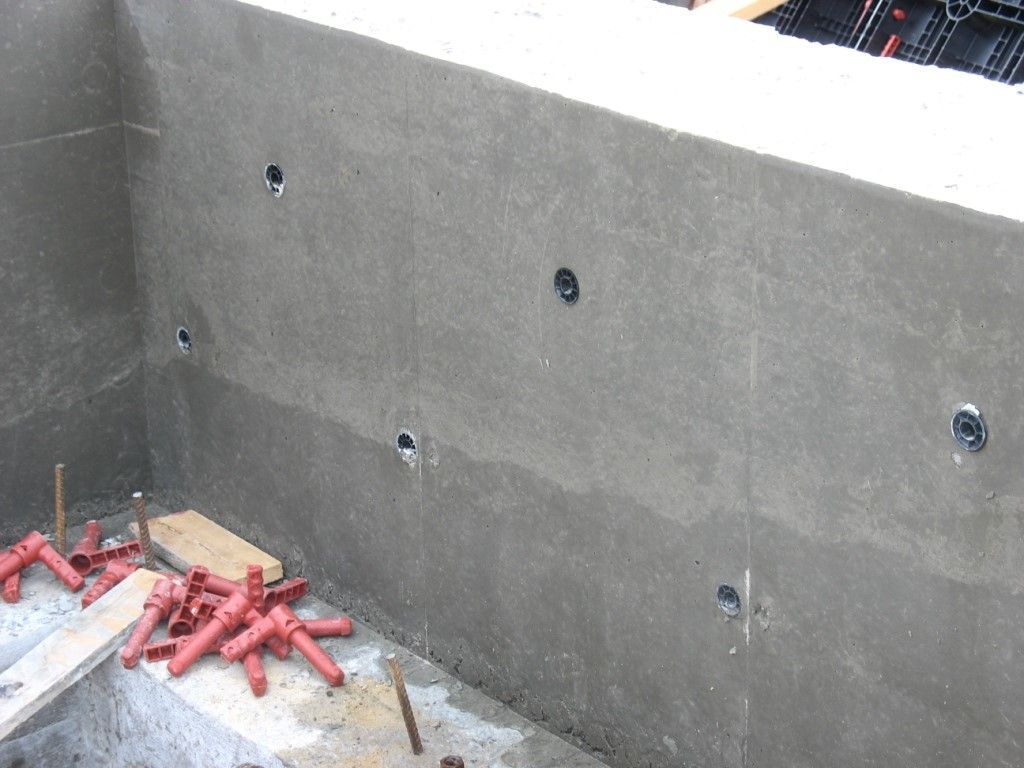
In the household often there is a need for the construction of small yard buildings.
For the construction of monolithic walls of small thickness, the owner of the house prepares a formwork of auxiliary material.
It can be slate, sheets of asbestos cement, scraps of corrugated board, plywood or any moisture-resistant sheet material.
Summarizing the above, we will briefly introduce into the table brief characteristics and scope of the most popular forms of formwork.
№ | Types of fences for monolithic walls | Scope of application | Frequency of use |
---|---|---|---|
1 | Low-rise buildings | Disposable | |
2 | Building plywood | Low-rise buildings | Disposable |
3 | Metal shields | Large multi-storey buildings | Reusable |
4 | Plastic panels | Large multi-storey buildings | Reusable |
5 | Aluminum fences | Large multi-storey buildings | Reusable |
6 | Non-removable blocks | Civil facilities | Disposable |
7 | Material Handling | Light outbuildings | Disposable |
From the data given, it is seen that under the same conditions it is possible to use formwork of different types. The final choice of enclosing structures is affected by the technical and economic indicators of the building design.
In areas where metallurgical enterprises are located, it is always possible to purchase waste products - boiler slag. This is a very cheap building material, which is used in the construction of villas and small private houses. For more information about the material, see this video:
Slag-concrete is prepared from a mixture of slag and cement in a proportion of 5: 1. Sometimes, instead of cement, lime and clay are used.
For the erection of monolithic walls of cinder blocks, a special platemaking structure is made. Fencing is a collapsible construction of wooden shields and clamps.
Slag-concrete is covered in the formwork layer by layer with the thickness of each layer 200 mm. Each embankment is rammed, carefully distributing the material around the corners and perimeter of the formwork at the points where the walls meet. As the hardening of the next layer of the mixture, the formwork is moved upwards.
The construction of a monolithic slag-concrete house will cost much less than the erection of a similar structure of monolithic reinforced concrete.
One of the first stages of the erection of structures for various purposes is the installation of formwork. Often this process is left without due attention. But already at the stage of preparation for the casting it becomes clear that not everything is as simple as it was thought at first. The assembly of the formwork will help to assemble the frame.
Types of formwork
There are three types of construction:
- Removable, which is dismantled after the solution dries completely. There is such formwork from separate parts. As a result, a collapsible construction is obtained, which is dismantled and can be re-used. Among the advantages of this type of formwork are easy installation, the possibility of reuse, which significantly reduces the financial costs of construction.
- Fixed, respectively, one that is not dismantled. Installation of the formwork of this type is made mainly of expanded polystyrene or foam. It remains part of the erected building. And at the same time it acts as a heater.
- "Floating" formwork is typical for the erection of a monolithic foundation, which is immersed in the ground. It is a board assembled from boards, which is slightly higher in height than the planned concrete structure. The shield descends to the pit and is attached to its walls. Over it rolled cardboard or roofing paper.
There are also several types depending on the purpose:
- Wall formwork. Its installation is carried out for the erection of vertical structures and walls.
- Horizontal, which is used to install the foundation and floors.
- Curved, which allows you to fill in details of unusual shapes.
Installation and dismantling of the formwork of each type has its own characteristics. They need to be known for quality work.
Advantages of non-removable formwork
Installation of non-removable formwork involves the acquisition of a ready-made kit for the execution of works. It remains only to assemble the structure and perform its installation. Hence, there are a number of advantages that formwork of this type possesses:
- short terms of work execution;
- simplicity of installation;
- light construction weight;
- resistance to the appearance of fungus and mold;
- fire safety;
- low cost.
Also, a non-removable formwork is simultaneously a layer of insulation and is a block of foam that easily connects with each other. In this case, the inner wall is thinner than the outer one. Thanks to this, a high level of thermal insulation is achieved.
Construction of non-removable formwork
The installation of the formwork of walls with the help of fixed blocks is much easier than the traditional method.
Work begins with the preparation of the site, laying a layer of waterproofing. On the foundation simply put on the blocks on the principle of brickwork (with a shift of seams). This allows to increase the strength (rigidity) of the structure.
First, stack only one row of blocks, then reinforce (overlap). For this, there are special grooves. The reinforcement is connected with each other by a vertical wire. In the same way, the following series are laid out.
Blocks are fastened together by simple joining of special grooves by easy pressing. Begin to pour concrete solution already on the third row of blocks.
In the process of work there is one small secret. The walls will be more reliable if the joints of the mortar layers remain in the middle of the block. To do this, fill the top row with half.
Features of the execution of a removable formwork
The basic moments of installation of the formwork will be considered with the example of a removable collapsible structure. This species is often carried out by landowners without the assistance of professional builders.
Installation of formwork is made of boards, blocks, plywood and other sheets of wood. The main thing is that these plates should be flat. All work begins with the preparation of the site. The platform must be completely cleaned of foreign objects, debris and so on. Further, with the help of bars marks the corners of the erected building. They will be the basis from which the remaining measurements will be performed. In accordance with the size between the bars is going to
Finished shields are attached to corner bars with the help of screws or nails. Mounting must be reliable. With the expansion of concrete, the pressure on the shield will increase, which can lead to cracking of the boards. The main thing is that the bar itself is left from the outside. Parallel to the assembled structure, another row is assembled at a distance from the future wall. As a result, you should get a frame around the perimeter.
A layer of rubble or sand is poured into the finished formwork box. This will protect the solution from loss of moisture, which will go to the ground. The formwork mounting technology provides protection against leakage through the openings. For this, the shields are covered with a film or roofing paper, which are fastened with screws or staples using a stapler.
All work must be done taking into account the level. It is very important. At each stage, the evenness of the structure is checked for height, length and vertical (especially important). Two rows of shields must go strictly parallel to each other.
Basic elements of formwork
The demountable formwork, which is assembled independently, consists of the following elements:
- The deck, which is a flat shield, which is the fence of the whole form. The structure should be strong enough to withstand the pressure of the solution. Therefore, it is made of plywood or edging boards 4-5 cm thick.
- Woods which are a support of a design. They hold the walls, not allowing the solution to squeeze out the deck. Produce forests from pine bars or planks (2.5-5 cm).
- Fasteners are all parts with which all the elements of the construction are twisted: wire, clamps, ties, hardware and so on.
The deck is most often assembled from boards with a width of 15 cm, which are joined in several rows by means of nails (driven from inside, curled from the outside) or self-tapping screws (they are twisted from the inside). The distance between the boards should not exceed 3 mm. Shields are fastened together with additional slats.
A simpler version of the manufacture of the deck is the use of moisture resistant plywood with a thickness of 1.8-2.1 cm.
Installation of formwork
The frame will be installed exactly and level if the site is prepared in advance. It is marked using cords stretched between pegs. The sand cushion is filled and compacted. If necessary, a foundation pit is prepared.
The formwork is installed in the following order:
- The perimeter should be marked with vertical guides (wooden blocks, metal corners or pipes).
- On the guides it is required to place the finished boards, keeping the necessary distance between them (it is equal to the necessary thickness of the basement).
- Secure the deck firmly. Support it from the outside with inclined beams (1 scaffold per meter of deck).
- Connect the boards to each other with brusks 5x5 cm.
- The inner side of the formwork is covered with a film (roofing material).
Foundations up to 20 cm high do not require a serious design. For them, enough bribed into the ground.
Installation of wall formwork
More difficult is the process of erection. At the same time, small-piece and large-panel formwork is selected.
The first option is suitable for the erection of small buildings (cottages, buildings of economic purpose) and partitions between the rooms. In this case, small plywood panels are used.
The installation of large-panel formwork is typical for the construction of buildings with high altitude. For work use sheets of metal or large sheets of plywood.
For the installation of walls prepare the foundation, in which the reinforcement is stuck. Round it a two-row frame of a casing is collected. When using conventional plywood, joints are smeared with glue or sealant. Currently, the market has a special plywood for formwork. Individual sheets of it are connected on the principle of "spike-groove", which does not require additional sealing.
Types of overlapping
Installation of the formwork of the ceiling depends on the type of overlap. Allocate the following types of structures:
- On the large bowls. It is used for structures with high altitude. In this case, use vertical stands, jacks, inserts, crossbars and other elements to connect the individual parts.
- On the wedge forests, which are used for multi-storey buildings. Instead of plywood panels, scaffolds are installed.
- In the forests of the cup type. This type provides for the installation of the frame. Stands are connected by a cup method.
- On telescopic bowls. Suitable in cases where the height of the ceiling is less than 4.6 m. It is based on tripods that support the entire structure. On top are shields made of moisture-proof plywood.
Formwork for overlapping
Currently, monolithic overlap is most often used. On his example, we will analyze the process of mounting the formwork.
Vertical racks are used for the formwork, connected together by bolts. They are attached at right angles to the bars going in the transverse direction. On these cross bars there is a plywood board, which is the bottom of the formwork.
The following materials are used for these works:
- stand - a beam with a section of 12-15 cm;
- crossbar and cross bar - edged board with a width of 16-18 cm and a thickness of 5 cm;
- slats - board thickness 3 cm;
- flooring - moisture resistant 1.8 cm thick.
Before the work begins, accurate calculations must be made. It is important to determine the necessary number of racks, the step of their placement and other indicators.
Installation instructions for the formwork of floors
The work instruction includes the following steps:
- To the top of the racks are attached longitudinal bars, the second end of which is fixed on the wall.
- In the same way, the second row is collected. For this, a board thickness of 5 cm is laid under the supports.
- Cross strips are laid in 60 cm steps.
- Install the support posts (strictly vertically).
- The posts are connected with each other by braces.
- On the cross bars are laid plywood sheets, leaving no cracks.
- The ends of the overlap are protected by a brick or brickwork.
- Is going to the frame of the armature. If necessary, leave space for communications.
When all the work is done, you can pour concrete. Remove formwork in 3 weeks.
Conclusion
Installation of formwork of each type provides for the use of certain materials. If boards are used, they must be new. Rotten old boards can not withstand the load and break. Plywood must be moisture resistant or laminated.
All work must be performed in accordance with the calculations made. This is especially important for the installation of formwork of ceilings and walls.
The technology of private low-rise housing construction clearly does not stand still, numerous construction organizations have mastered a complex and quite effective method of building buildings using formwork for pouring walls. The method, used earlier only in industrial and high-rise construction, allowed to completely withdraw the box of a two-storey building in less than three weeks. The basis of high-speed construction is the use of standard formwork sets of wall pouring, enabling the maximum mechanization of the slowest process, requiring a large amount of highly skilled labor, namely the laying of the bearing walls of the house.
For what purposes is used formwork in construction
Since the invention of reinforced concrete, casting a cement-sand mixture into a prepared mold has become the only possible way to quickly build a very strong and inexpensive construction structure. Concreting in the prepared formwork allows in an automatic mode to solve several difficult tasks:
- Making concrete mass accurate geometric dimensions and position relative to steel reinforcement and other building elements;
- Pouring of concrete mixture into the formwork allows to accelerate the process several times and make it as simple and relatively inexpensive to use;
- The application makes it possible to obtain very strong and lightweight structures with a minimum consumption of building material.
For your information! The strength and thickness of the walls are easily regulated during the preparation and assembly of the formwork for pouring. In this case, unlike other methods of forming walls, the thickness and shape can be made any, up to a millimeter, while the brick and block constructions are tied to the size of the masonry materials.
Types of formwork for wall filling
In addition to the well-known and the most popular formwork from sawn timber, reusable metal formwork is widely used, various types of fixed formwork for walls made of asbestos-cement sheets, slate, expanded polystyrene, composite materials based on sawdust, plastic. Disposable types are often used as insulation or finishing material for the surface of a concrete wall.
Requirements for the construction of formwork
Regardless of the type and material of the formwork, the shape design must meet the following requirements:
- The assembly and installation of walls, power elements, screeds, supports, braces should be relatively simple and at the same time reliable, ensuring a lasting connection;
- After casting the concrete, the structure should not be deformed, change the proportions, lose its tightness, swell, interact with the concrete material;
- The mold should be easily detached from the concrete surface when dismantled after the concrete has solidified;
- If possible, the components to the wall formwork should be light and accessible for carrying one or two workers without the use of handling equipment.
It is clear that because of these requirements, reusable structures for wall pouring are made of steel, aluminum or reinforced polypropylene. In addition to the long service life of metal and reinforced plastic, this formwork even after 50 to 70 assembly and disassembly cycles provides stable dimensions of the casting thickness over the entire width and height of the mold.
Reusable structures for molding walls
Formwork is a set of elements that ensure the strength of the form, its permanence in the loaded state, the more intensively the form is used for pouring walls, the more components for wall formwork is included in such a structure. Reusable systems can be conditionally divided into two main groups - standard interchangeable and universal formwork.
Shaped shuttering is the simplest and most accessible form option. These are usually three steel sheets reinforced with stiffeners, and an even number of metal ties that connect the mold walls to a box structure. A fairly simple and even primitive arrangement of such formwork allows it to be used even by an unprepared person.
On the site where a part of the concrete wall is to be cast, metal walls are installed along the marked contour and interconnected by screeds. The end surfaces of the mold are closed with removable cover plates. After pouring this form and hardening of the cement, the screeds are knocked out through the hole in the concrete, the metal walls are removed, rearranged to the next standing area, fixed and poured with concrete. In this case, the holes from the screeds on the old casting are used to fix the extreme fastening of the adjustable form before pouring the continuation of the walls.
Universal systems are most in demand in the flow schemes of building houses. The advantages include the possibility of creating a formwork that provides the pouring of walls with a wide range of thickness and angle of docking. The standard formwork kit includes:
- Side shields of sheet metal, reinforced with corner plates. Shields form the surfaces of the form of the formwork, so each time they are carefully aligned in a vertical and horizontal direction;
- Angle elements provide connection of side panels for the purpose of forming the corners of the walls of the building;
- Screws and pivots provide locking of side panels at a certain distance from each other. From the correctness of their installation after the filling of walls depends the stability and uniformity of the thickness of the casting;
- The struts, most often telescopic, less often helical, ensure the holding of the side shields in a stable position throughout the entire pouring process. Often, with the help of struts, the formwork is adjusted and aligned.
For your information! The ease and speed of assembly-disassembly of reusable formwork is usually provided by using wedges and stoppers. To unmount such a form, it is enough to knock out the locks on the pivots and remove the struts.
After assembling the shields and installing the pivots and screeds, before aligning the adjustment of the installed form along the vertical and horizontal lines is performed. If the formwork orientation is made correctly, the bars of the reinforcement, released from the foundation or walls of the lower floor, will be inside the mold in the calculated position.
Non-removable forms of formwork
Such forms for pouring walls are used in cases where it is easier and cheaper to leave the formwork material on the concrete surface than to waste time and effort to remove it. In many cases, the walls of the mold not only do not affect the quality of the fill, but also strengthen it. The most common type of family of fixed formwork of the walls of the house are foam polystyrene and foam plastic hollow blocks, in shape and size resembling foam concrete material.
After laying one or two rows of such blocks, the bars of steel reinforcement are laid in the cavity and filled with concrete mortar. After grasping the concrete, a stone wall is obtained, covered with a layer of expanded polystyrene. Foamed polystyrene foam will provide excellent noise and thermal insulation, but it remains a combustible material, so the internal surfaces of the walls, obtained by pouring in a similar manner, must be finished with cement-sand plaster or plasterboard. In addition to expanded polystyrene, non-removable forms of formwork are made from compositions based on cement, sawdust and liquid glass.
This kind of formwork is generally considered safer, so modern methods of pouring walls into non-removable forms, as a rule, use similar slabs and detachable molds. In any case, the formwork material is to be finished with protective plaster compositions, which allow minimizing human contact with plastics and modified wood.
Formwork and forms for pouring walls from sawn timber
Despite the huge popularity in the use of sawn timber, edging boards and beams for the manufacture of all kinds of basement wall sections, concrete foundation castings, wood in its pure form is very rarely used for making molds for pouring the bearing walls of a house. Firstly, the use of a calibrated rack or lining for the assembly of shields will cost a tidy sum, and you can not use a conventional unedged board, since the surface of the casting will turn out to be uneven. For the foundation, the presence of prints on the surface is not particularly important and does not affect the strength of the casting.
As an exception, one can cite the case when the formwork walls are made of laminated chipboard, or OSB. In this case, after pouring concrete, very smooth and even walls are obtained, which do not require any additional cleaning and trimming. With each filling, the laminated surface is erased and partially deformed, eventually it swells and exfoliates, so the service life of such a form for walls is limited to 70-100 cycles.
The construction of any monolithic objects, whether a dwelling house or an industrial building, does not do without wall formwork. This construction is necessary for the construction of walls and ceilings.
Manufacturers offer a variety of variations to solve problems of any complexity, one of the most popular is the formwork of the Gamma series.
Formwork material
An important characteristic is the material from which the wall formwork is made. It depends on the calculation of the required amount of concrete, as well as its weight, strength, cost, installation and finishing. Formwork is made of:
reinforced concrete;
Each of the materials has its advantages and disadvantages. Metal formwork is widely used in industrial construction (withstands high pouring speed). However, it is very heavy, its installation requires the use of special equipment.
Form of expanded polystyrene is light, serves as an additional insulating layer. However, the low strength of the material complicates the construction (for example, you can not use a concrete pump for pouring).
Wood, chipboard and plywood are also easily deformed, but at the same time provide an easy and quick installation. Plastic is sensitive to negative temperatures, but durable and airtight. The main sphere of use is private construction (if you need to make a shallow foundation or a light building with your own hands), because their installation does not require special skills.
Major developers prefer to work with the use of removable structures, which also includes Gamma formwork. Depending on the purpose, it can be used for erection:
round structures (columns, pillars);
overlapping.
Calculation of the required volume of concrete is done taking into account the type of formwork.
Advantages of removable structures
If it is not a one-off construction, the prefabricated large-panel or panel formwork is the best option, thanks to such advantages:
-
Removable formwork installation
The main components are the unit and the fastening elements (). Depending on the type of construction (panel, large-panel), the block can be from 90 * 60 cm in size, and up to 330 * 120 cm. The required size of the boards is calculated taking into account the scale of construction. For the construction of a small house, or a conventional panel formwork with 1.5 * 1 m blocks is the best option.
Shield formwork is easy to assemble with your own hands, installation does not require the use of special equipment, and various components can assemble the construction of any shape. This makes it indispensable for pouring a foundation or erecting walls and floors of one or two-story buildings.
The frame of the shield is made of a metal profile (high-carbon steel or aluminum alloy). Shield - plastic or plywood, in some cases, is provided with a hardening material. The installation of additional stiffeners guarantees the strength of the structure.
An essential advantage of the non-removable form is its cost, and easy installation. The construction of monolithic houses with this construction allows to minimize labor costs. Installation of other structures consists of these stages:
- mount the corner block and erect the walls;
- the installation of door and window openings;
- concreting is carried out (each stage of pouring, performed after the previous layer has hardened).
Features large-scale formwork
Large-scale formwork Gamma has, in addition to the listed elements, the following components:
inner corner to make a corner block;
shields on hinges with which you can form internal and external angles of any radius;
arc-forming element, to obtain a rounded section of the wall or overlapping;
screeds that rigidly fix the shields between themselves.
Also, to facilitate work at the height, the kit can be supplied with a stage for workers, which are easily attached to the unit at the level of any floor. Accessories can be purchased as needed, the specialists will calculate the required amount.
Large-scale formwork is used in the construction of large-scale objects, therefore, special requirements are imposed on it. The unit must withstand high filling speed, and its rigidity - to provide an ideal geometry of walls and foundations. This is ensured by the following structural features:
shield from the all-rolled section;
a special lock that allows additional sheets between panels to be inserted, up to 10 cm thick (for hardening the structure or additional heat and waterproofing);
the fastening elements simultaneously pull together and fasten the shields to each other;
the block is covered with a special, protective coating (powder paint), this external finish helps to prevent corrosion.
For today, the removable formwork Gamma is the most optimal solution for the price-quality ratio.
Application of wall formwork (video)
The choice of formwork for various objects
Basically, they use the foundation of small objects (dacha, garage) with their own hands. Installation in the trench and fill are performed manually. For heavy structures, the foundation and walls are reinforced by reinforcement. External and external finishing is possible immediately after the concrete has hardened.
Non-removable panel formwork made of expanded polystyrene has become a popular solution for the construction of small private houses. Thermal insulation properties of expanded polystyrene allow to save significantly the costs of heating the room. In addition, the decoration of such a building (both inside and outside) is not particularly difficult. Most of the finishing materials (gypsum board, facing plates, lining, veneer) are easily attached to sheets of expanded polystyrene.
Removable panel formwork can be installed to build a shallow strip foundation, in which case it acts as a basement floor. Wooden or - the optimal solution for the price, since a shallow foundation does not imply the use of complex structures. It is easy to assemble and disassemble with your own hands, with the help of improvised tools.
Large-scale formwork (for example, Gamma 330) is used in the construction of multi-storey buildings, industrial facilities, etc. Due to its configuration, it is easily transformed into a form for overlapping, supporting elements. The accompanying documentation indicates possible assembly schemes and the calculation of necessary elements.
Versatility. Accessories (special fasteners, rotary elements) allow you to create complex shapes.