- - an unpainted profiled sheet of light gray or silvery-gray shade. The most budgetary option.
- Profiled sheeting with one-side polymer coating - The corrugated board is painted on one side. It is used as a wall and roofing material, enclosures of country cottages (the color side inside).
- Profiled sheeting with two-sided painting - the polymer coating is applied on both sides. Used for building fences, a more expensive option. The company MetStroy produces coloring of each side in different colors at the request of the client.
|
![]() |
![]() |
Galvanized corrugated board - the most economical option | Coating on one side - used for roof and walls | Two-sided coating - designed for fences |
Types of coverings for corrugated board
1. Polyester
Also known as polyester. The thickness of the polyester coating is 25 microns, the surface is smooth, semi-matt. Metal with polyester coating is excellent for the production of corrugated board, in combination with a low cost, this type of coating has become very popular for the production of profile sheet.
2. Textured polyester
The coating thickness is 25-45 microns, due to the thicker the coating has a longer service life than a simple polyester coating. As the name suggests, this coating has a texture that gives the coating an attractive appearance.
It should be noted that the service life of polyester coatings in places with increased corrosive activity is significantly reduced (sea climate, proximity of industrial enterprises). Therefore, in areas where the polymer coating is exposed to aggressive environmental effects, it is necessary to use corrugated board with other types of polymer coatings.
3. Plastisol
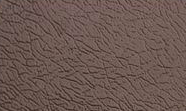
4. Polyurethane coating
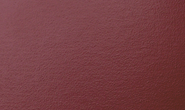
5. PVDF (polyvinylidene fluoride and acrylic)
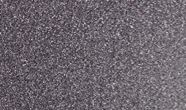
6. Printech
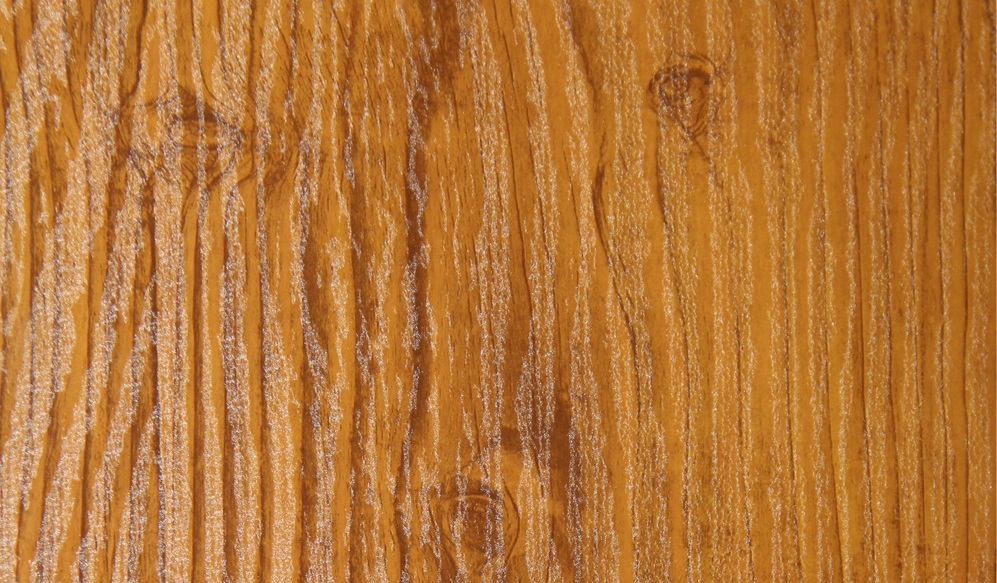
Metal corrugated sheets are a durable, reliable and affordable material for creating various objects. Such elements are characterized by high technical characteristics and relevance in construction. In this case, there are several types and a variety of grades of corrugated board. The most practical option is a material having a polymer coating. These products are steel profiled sheets, on which several protective layers and a polyester coloring compound are applied. This feature allows you to create a variety of designs, differing aesthetic appearance and good performance.
Properties, types and features
The technology of production of corrugated sheets is quite simple. High-quality raw materials are used in the manufacturing process. Rolled steel sheets pass through special roll forming machines, and then protective layers are applied to the metal. The structure of the outer side of the corrugated board includes steel sheet, zinc layer, as well as a layer of anti-corrosion protection, a primer and a colored polymer composition of polyester. The internal galvanized side of the sheet has an anti-corrosion coating, a soil composition and a layer of protective paint. This structure provides high characteristics of galvanized material.
- Application of zinc layer on steel sheets, which is the main protection against metal corrosion;
- Passivation of the zinc layer represents a failure of the coating of the sheets with an oxide film, which has protective properties;
- The mixture for priming the surface provides good adhesion, as a result of which the galvanized material is reliably bonded to the polymer layer;
- The application of a colored layer of polymer composition, and then its varnishing. The thickness of such a coating can be from 25 to 200 μm, which determines the degree of durability and stability of the material.
In the manufacturing process, most often the color composition of polyester is applied to flat sheets of material, and then performs the profiling of the elements. The reason is that in this way the polymer coating is applied more evenly, providing the same degree of metal protection in all areas. At the same time, for the production of profiled sheeting, the most accurate and technological machines and other equipment are needed, since the protective composition is applied very thinly. The probability of its damage to poor-quality equipment is quite large.
Qualitative corrugated board with a coating is a demanded material in construction. For example, galvanized sheets with a layer of polyester are used for roofing, construction of fences, temporary structures and construction of ancillary facilities. Versatility and relevance are due to a number of advantages that distinguish galvanized colored corrugated board compared to other materials.
Metal galvanized sheets have different characteristics and are presented in a wide variety. The common features of all brands are such qualities as resistance to mechanical, chemical and climatic influences. This feature ensures the efficiency of the structure from galvanized corrugated board in any conditions. Polyester coated sheets also feature simple mounting technology, high levels of strength and reliability, fire resistance and low temperatures.
The stages of manufacturing galvanized sheets are the following processes:
Galvanized corrugated board with a coating is a quality elements for the construction of various objects. In this case, there are several options for coverage, each of which has certain features and characteristics. In each case, there are distinctive features, and the material has a certain lifetime. Depending on these qualities, you need to choose and painted corrugated board. The most common coating options are matt polyester and polyester, pural, plastisol, PVDF. Each composition includes components that give the coating the necessary properties. For example, profiled sheeting, galvanized coated polyester - a material that has an aesthetic appearance, is resistant to ultraviolet rays and temperature differences. At the same time, the resistance to mechanical damage at the polyester coating is low enough, but there are certain advantages. Galvanized sheets with polyester coating are practical in use, easy maintenance and suitable for creating decorative corrugated board, as polyester allows to simulate the structure of stone or other material.
Coatings of galvanized corrugated board have the following features:
- Polyester is characterized by low cost, medium technical level and aesthetic appearance. This polymer coating is not resistant to mechanical damage. Matte polyester is more resistant to temperature changes, deformation and mechanical influences;
- Based on polyurethane, a pural is produced. The layer of such a substance on galvanized metal sheets is resistant to chemical attack, acids and ultraviolet radiation. The color of the sheets does not tarnish with time, and the service life of the material is 50 years;
- Painted corrugated board with a coating of plasticizers and polyvinyl chloride is the best option for operation in aggressive conditions. Plastisol coating creates a special structure, due to which the decorative corrugated board is made with the coloring for wood or other materials;
- The PVDF coating is characterized by a high level of resistance to chemical, temperature and climatic influences. Also, the layer of this substance is resistant to mechanical damage, providing steel protection from deformation and preventing the reduction of technical characteristics, and its service life is more than 40 years.
The choice of galvanized corrugated board with a color coating should be carried out depending on the requirements for the design, operating conditions, installation features. In any case, an important point is a careful calculation of all parameters and characteristics, which determines the optimal version of the coated galvanized material.
Qualitative colored corrugated board is presented in a wide range. It serves for the installation of roofs, fences, construction of buildings and structures, ceilings and fences. A number of characteristics of galvanized metal with polyester coating provides a universal application of products and a long service life. Such a painted corrugated board is an affordable and practical solution for building and equipping buildings.
) is a sheet of cold-rolled hot-dip galvanized steel, on which several types of coating are applied. As a result of the production process, the steel sheet, which has already been galvanized, is covered with a phosphate layer, which performs an anticorrosive function. After that, the primer is applied, the reverse side of the sheet is covered with a special protective varnish, and a polymer coating is applied to the face moaning.
Zinc plating of steel sheet provides cathodic protection of steel against any corrosive effects. The thickness of the zinc layer reaches 25-30 μm. If you look at the corrugated sheet in a section, it will be a multi-layered structure, the center of which is galvanized steel, on both sides of which there is a passivated layer and a primer layer, and then a polymer coating on the front side and a protective paint on the bottom.
Polymer coating is made of organic polymers, which are used as plastics and synthetic resins. They add additives and pigments, which give the layer not only protective, but also decorative properties.
One of the most commonly used is the plastisol coating (PVC). It includes polyvinyl chloride and various additives. The coating thickness for the roofing sheet is 175 or 200 μm. Such a significant thickness of the plastisol coating provides reliable protection of the corrugated sheet from mechanical damage. The shortcomings of such a coating include low temperature resistance, as well as low resistance to ultraviolet radiation, so this material is not used in the southern regions. Experts of Euromet believe that plastisol coating provides reliable protection against adverse environmental conditions, especially in highly polluted environments. If we talk about color fastness, the plastisol coating is rather low, and the brightness of the color is significantly reduced after several years of operation. If the coating thickness is 175 μm, it is smooth, embossing can be applied to a coating thickness of 200 μm, but it significantly reduces the thickness of the protective layer. Profiled sheeting with plastisol is used in the construction of roofs, since it is plastic and at the same time resistant to mechanical influences by the material.
The most common for the profiled sheet, used in construction, is a polyester coating. Such materials reliably proved themselves in domestic conditions. The coating protects the metal layer from corrosion, while Euromet notes that the corrugated board is weatherproof and permanently retains the brightness of the color.
One of the varieties of polyester is matte polyester, which has excellent aesthetic characteristics. It is usually used to give the buildings a decorative appearance.
Relatively new among the used polymer coatings of corrugated board is PURAL® matt (developed by Ruukki®), the composition of which is based on polyurethane. It is resistant to corrosion, solar radiation and a variety of chemical effects. Building materials using PURAL® matt are used not only for roofing, but also for facades.
If an increased resistance of the profiled sheet to weathering is required, the specialists of Euromet recommend the use of a PVDF coated material (PVF2). Such material permanently retains color, is resistant to corrosion. Its main purpose is facade cladding, it is used where higher requirements are imposed on the color design of the material.
In addition to polymer, in the manufacture of corrugated coatings are applied. This coating is a thin film, which is formed when the paint and varnish materials dry out. The main role of the paint and varnish coating is to protect the surface of the material from corrosion, as well as to improve the aesthetic qualities of the material. Some paint coatings perform a special function - electrical insulation coatings, luminous (fluorescent) coatings, heat-resistant and thermo-indicator coatings, etc. The lifetime of the paintwork is several years, it is easy to apply and restore. As a rule, coatings of metal and profiled sheets consist of several layers, the main requirement for which is high adhesiveness, that is, the adhesion of the layers to each other and the base material. When coating the profiled sheet on the substrate, first a primer is applied to increase the adhesion properties of the coating, then a layer of paint and varnish, which ensures the gloss of the surface. Multilayer coatings can reach a thickness of 40 to 300 μm.
According to the specialists of the company, the use of corrugated board makes it possible to significantly shorten the terms of construction works and achieve a high decorative effect of surfaces.
Profiled galvanized sheet (corrugated sheet) is one of the most in demand modern building materials. It is an easy, unpretentious, easy to transport and install building material. In addition, it is reliable and functional.
Profiled sheeting with polymer coating is produced by the method of cold rolling on rolling mills made of galvanized steel sheet coated with a polymer. After rolling out sheets of the profile of a wave-shaped or trapezoidal section, differing in height of a wave or a trapezoid, width, ribs of a rigidity leave.
Profiled galvanized sheet is a universal building material used in a very wide range of construction works. It is used as a basement overlap and inter-floor overlapping, for roofing, as wall constructions, for fences and various fencing, fixed formwork. Also used in the form of sandwich panels, where the inner sheet serves as a load-bearing structure, and on the other hand a beautiful facing material covered with a layer of polymer, between which heat insulation is laid.
Advantages of profiled sheet.
Profiled sheeting is relatively lightweight material, it simplifies its transportation and reduces the complexity of installation.
Galvanized steel sheet on one side and polymer coating on the other ensure the durability of the corrugated board, protecting against corrosion.
A wide range of colors of polymer coating gives you the chance to choose the right shade of any color. Profiled sheeting of 30 different shades, which are selected on a special scale RAL, RR.
Polymer coating of the roof does not burn out in the sun, does not rust and does not leak under any weather conditions due to the configuration of the flooring and the peculiarities of the installation.
Polymer coating of corrugated board.
The application of a polymer coating on hot-dip galvanized sheet steel is a rather complex process with a gradual quality control of the work throughout the entire process chain.
The steel sheet undergoes a process of mechanical and subsequent chemical treatment: phosphating, priming the surface to be prepared, drying and then coating the surface of the galvanized steel sheet with a polymer, followed by drying in a heat chamber. As a result, the finished product comes out: a multi-layered profiled sheet coated with a polymer having several layers:
- Sheet of steel.
- Zinc coating.
- Passivating layer.
- Coating with soil.
- One side of the sheet is covered with a protective layer of paint.
- The other side (front) is coated with a polymer.
Polymers used for coating have different perceptions to the factors of aggressive impact, therefore the above-mentioned coating layers are applied according to the parameters of each grade of profiled sheet. Coatings of polymers have different durability:
- To ultraviolet radiation is the color fastness of the coating.
- The temperature is the heat resistance of the coating.
- To an aggressive chemical environment.
- To mechanical damage.
At the moment, there are several varieties of polymer coating of corrugated board:
- Polyester - the most affordable at the moment for the price of polymer coating and the most common for different climatic zones. Polyester is resistant to ultraviolet radiation and weathering, but has a small strength. Therefore, it should not be used in dirty external environments and very carefully perform loading and unloading operations, transportation and installation of the profiled sheet. The basis of polyester is polyester paint. Polyester can have both a glossy and matte finish. He owns good color fastness and plasticity. The heat resistance of the coating is about +120 degrees Celsius. The choice of this type of coverage will be economically feasible and technologically correct if the facility is located in an environmentally clean place and the load during operation is small. The service life of the coating is from 10 to 30 years.
- Polyurethane is a unique coating consisting of polyamide and acrylic. The coating is resistant to ultraviolet radiation and chemical attack of aggressive environment, easily withstands high temperatures and diurnal temperature differences. Recommended for use in cities. It is used for the manufacture of metal roofing, the rebated roof, components for the roof, corrugated board, drainage systems. The heat resistance of the coating is from -15 to +120 degrees Celsius. Service life from 20 to 40 years.
- Plastisol is a decorative polymer, consisting of polyvinyl chloride, modified with plasticizers. Available as a one-sided coating, and with two-sided. A layer of a covering of a professional flooring from plastisol 175 or 200 microns at unilateral covering, and bilateral - on 100 microns from each party. Due to the thick layer, plastisol coating is very resistant to mechanical damage, but due to low heat resistance and low resistance to sunlight, this coating is not recommended for use in areas with high solar activity. With a thick coating layer, plastisol has good anti-corrosion resistance. Having low color stability, after 3-5 years the polymer becomes faded and dull. The service life of the coating is from 25 to 35 years.
- PVF2 is a coating consisting of 80% polyvinyl fluoride and 20% acrylic. This durable polymer coating withstands cold -60 degrees and does not lose its positive qualities at a temperature of +120 degrees Celsius. Polymer PVF2 does not change its color at all and has an even glossy coating throughout its life. It has great resistance to mechanical damage and aggressive chemical environments. Recommended for use in chemical plants, salt plants, seaside and other aggressive chemical sites.
If you use profiled sheeting with polymer coating, you can build strong, durable and aesthetically decorated rooms, roofs, fences. At the same time, money resources, time are saved, labor intensity of the work is reduced.
A sheet profiled with a polymer coating is a very durable material. Its service life can be 50 years and more, which, in combination with a high load-carrying capacity and a small price, turns such profiled sheet into an excellent building material.
The device of a polymeric covering of the profiled sheet with a protective layer from a varnish from the internal party
Such longevity is the achievement of modern technologies, since only a few decades ago there was only a galvanized profiled sheet, for which a service life of 20-25 years was already considered a fantastic result. The application of polymer coatings to a galvanized sheet allowed this figure to be more than doubled and led to the widespread use of this material.
About what are the protective and decorative coatings of corrugated board, how they are applied, their properties and advantages, and will be discussed in this article.
Structure and production of a sheet with a polymer coating
The metal profile with a polymeric covering is made on high-tech lines from rolls of steel on which the protective layer of the necessary color is already put. The quality of the machines in this case is of particular importance, since in most cases the protective layer is thin enough and can easily be damaged during the bending of the sheets.
The application of polymer protective coatings to the finished corrugated board is rarely practiced, since the complex shape and the presence of depressions complicate the process of uniform distribution of the substance over the surface. This requires complex and expensive equipment, which leaves an imprint on the final cost of the products.
Steel with a polymer coating has a complex structure, and its production consists of the following stages:
- Galvanizing of "black" steel. Despite the presence of a polymer coating, the main anticorrosive properties of the metal is given by the zinc layer. The polymer simply protects it from chemicals, mechanical damage and banal flushing with water during rain.
- Passivation of the zinc layer. During this process, zinc is coated with an oxide film, which prevents corrosion.
- Application of primer. Primer improves the adhesion of materials, so that galvanized metal with a polymer coating forms a strong bond.
- Application of a polymer coating on a metal or its varnishing. The final stage of fabrication of the material is the application of a protective layer. The thickness of the polymer coating of galvanized steel can be from 25 to 200 μm, depending on the purpose of the material and the type of polymer.
Typically, as a protective layer, different polymers are used for the face side of the corrugated board, and a special lacquer for the inner.
Kinds of polymeric coverings of a professional flooring
The main types of polymer coatings that have spread in Russia are the following:
- Polyester;
- Matte polyester;
- Pural;
- Plastisol;
- PVDF.
Let us dwell on each of them in more detail.
Polyester
Profiled sheeting with polyester coating is the cheapest and therefore the most common option. This coating is UV-resistant and fades slowly, preserving the original brightness for a long time. In addition, it perfectly protects the metal from corrosion and easily tolerates large temperature changes.
The main disadvantage of this option is that the polymer coating of polyester is applied very thinly. Because of this, it is easily scratched even from a slight mechanical impact. Therefore, the corrugated board with polyester coating can be damaged during transportation to the site of construction or installation.
Polyester coated profiled sheeting
Therefore, the selection and delivery of this material should be taken particularly responsibly. It is necessary to carefully study the sheets before purchasing for defects. If the batch is big - then you can do this by selecting several random sheets from each pallets. Try to bend the sheet a little - in spite of the fact that the thickness of the polyester coating is only 25 microns, it has good elasticity and should not be covered by cracks.
To avoid damage to the cover during installation of the profiled sheet, make sure that the builders walk on it in shoes with a soft sole without thorns and do not lay tools on the surface of the material. In addition, to cut it, they should not use the Bulgarian. This tool is not suitable for cutting a sheet of profiled polyester, as the flaring pieces of metal easily burn a thin coating.
If you observe precautions, then the corrugated sheet with such a coating will be quite durable. For example, properly mounted roofing with a polyester polymer coating will last you at least 25 years, and for the entire lifetime of its color will change little. A little less will serve a fence, especially if it is in front of a busy road.
It is worth remembering that if profiled sheeting with galvanized polyester was scratched - this does not mean that corrosion will develop instantly. Under the polymer layer is galvanized, which will also protect the metal from spoilage. Therefore, scratches on the surface of the profiled sheet should be corrected in time using paint or special compounds.
In addition to the glossy version, there is also a galvanized steel with a polyester matte finish.
Matte Polyester
Despite the fact that the usual polyester and matte are the same in composition, their properties are somewhat different. The surface of the profiled sheet with such a protective layer is rough, due to which the light is scattered, and the coating does not shine. In addition, because of the unevenness of the surface, the thickness of the polymer coating of the corrugated board can not be measured accurately, and the mat polyester is applied in a large layer. This ensures a longer service life of this type of profiled sheet, which reaches 40 years.
Another feature of a matte polymer coating is the ability to simulate with great accuracy the relief and texture of other materials: stone, brick or wood.
Pural
Pural is a polymeric protective coating, which is made on the basis of polyurethane, often with the addition of acrylic and polyamide. Profiled sheeting with coating pural is very durable - its service life reaches 50 years. It is resistant to mechanical influences - it is very difficult to damage the protective layer of this material, because it is incredibly durable and the thickness of the coating is 50 μm.
The profiled sheet, protected by a layer of this material, is resistant to chemicals, including acids, and is also recommended for use in marine climate. Pearl coated steel easily withstands large temperature changes and is resistant to ultraviolet, although over time, the colors, however, somewhat lose their brightness.
Sheet of corrugated board with a protective layer of wear-resistant polymer coating pural
The only drawback of this material is that the corrugated board with a polymer coating made of pural is several times more expensive than the options with a protective layer of polyester. Therefore, this corrugated board is used, mainly in aggressive climatic conditions, including areas with a large number of industrial enterprises.
Due to the high cost, a profiled sheet with a similar coating is most often used as a roofing and for finishing facades. For the device of fences, ancillary and industrial premises it is used extremely rarely.
There is not only a smooth polymer anticorrosive coating made of pural, but also a matte version of this material. Moreover, due to structural features, such a protective layer additionally acquires resistance to various contaminants.
Plastisol
Polymer coating plastisol consists of polyvinyl chloride (PVC) and plasticizers. It is applied in a thick layer of 200 microns, so that the corrugated board with such a protective layer is most resistant to mechanical influences. In addition, PVC provides excellent protection against chemicals and aggressive climatic conditions.
However, corrugated board with polymer coating from plastisol can not be used in regions with a hot climate, since it has a low temperature stability. In addition, this profiled fiber fades very quickly, so it is recommended to use light colors for it. First, they burn less, and, secondly, they do not so heat up under the influence of sunlight.
Simulation of the wood texture on the polymer coating of corrugated board from plastisol
Polymeric protective and decorative coatings from plastisol have one more important feature - they have a relief surface. They are crowded under the skin, wood and other materials, as a result of which the corrugated sheet becomes opaque and does not give glare.
As a rule, the PVC coated polymer profile is used in northern regions characterized by an aggressive climate, as well as in industrial zones, especially in the case of chemical plants. In addition, it is used in those cases where there is an increased risk of mechanical damage to the material. For example, if there are often hail or dust storms in the area.
PVDF
PVDF coating of corrugated board consists of 80% polyvinyl fluoride and 20% acrylic. Of all the existing polymers, this coating provides the best protection against all types of non-mechanical effects. At the same time PVDF provides a good protection of steel and from mechanical damage.
In addition, the PVDF-coated polymer sheet is incredibly resistant to ultraviolet radiation, so it practically does not fade. Roofs and facades made of this material will retain the original color for almost the entire service life, which reaches 40 years.
Thus, profiled sheeting zinc-plated with a polymer coating of PVDF is perfect for roofing and finishing of buildings located in industrial areas, on the banks of salt ponds and along lively trails.
Technical characteristics of polymeric coatings of corrugated board
Despite the fact that all polymer coatings are a protective layer for the profiled sheet and have the same function, their properties are very different. For convenience of choice, they are summarized in the table below.
Properties | Polyester | Matte Polyester | Pural | Plastisol (PVC) | PVDF (PVDF) |
---|---|---|---|---|---|
Physical properties of the polymer coating | |||||
The thickness of the coating is nominal, μm | 25 | 35 | 50 | 200 | 27 |
Thickness of polymer coating of metal, micron | 19 | 23 | 30 | 192 | 20 |
Primer thickness, microns | 6 | 12 | 20 | 8 | 7 |
Maximum operating temperature, ° С | 90 | 90 | 100 | 70 | 110 |
Surface | Smooth | Relief | Smooth | Relief | Smooth |
Service life, years | 20-30 | 30-40 | 40-50 | 30-50 | 30-40 |
Compositions of polymer coatings | Polyester | Polyester | Polyurethane, polyamide and acrylic | Polyvinyl chloride and various plasticizers | Polyvinyl fluoride - 80%, acrylic - 20% |
Stability of decorative polymer coatings to various impacts (see note) | |||||
Resistance to UV radiation | 3 | 3 | 4 | 1 | 5 |
Resistance to mechanical impact | 2 | 3 | 4 | 5 | 3 |
Resistance to chemical attack | 2 | 3 | 4 | 4 | 5 |
Resistance to aggressive climatic conditions | 2 | 3 | 4 | 4 | 5 |
Resistance to corrosion | 3 | 4 | 5 | 5 | 4 |
Note: The stability value, which is different for a particular polymer coating of galvanized products, is indicated in points from 1 to 5, where 1 is the lowest index and 5 is the highest. The evaluation was based on the manufacturers' data, as well as the existing tests for these coatings.
As can be seen from the table, the thickness of the polymer coating of corrugated board is much less than the thickness of the "protective layer", which is indicated by the manufacturer. Although this can not be called deception, the primer also has certain protective properties.
Perhaps you noticed that the table does not have such an important characteristic as the weight of corrugated board with a polymer coating. However, this is not a mistake. The fact is that even the mass of a thick protective layer of plastisol is negligibly small, compared with the mass of the metal sheet itself. Therefore, the weight of the polymer coated steel is usually considered to be the same as without it.
Methods of applying polymer coatings
Technical characteristics and service life of galvanized sheet with a polymer coating depend not only on the material of the protective layer, but also on the method of its application.
A layer of polymers can be applied to the metal in various ways, but their essence is one. The galvanized steel is degreased and prepared, after which it is painted. Then the product enters the furnace, where polymerization and fixing of the protective layer takes place under the effect of temperature.
The most common technology of applying polymer coating in a powder way. To do this, during the painting phase, an electric current is passed through the article, informing it of the charge. After that, a fine-dispersed coloring powder is sprayed in the chamber, which has a charge opposite in sign. Under the influence of the magnetic field, the powder particles are attracted to the surface of the metal, after which the product enters the furnace where the polymerization process takes place.
Production line for powder polymer coating
Polymer-powder coating of metal has a number of advantages, compared with the coloration of liquid ink particles. First of all, this is a very uniform distribution of the dye over the surface with a minimum error. This improves the protective properties of the polymer layer, and also reduces the likelihood of a defective product passing through.
In addition, polymer-powder coating of metal has a high adhesion and wear resistance. Due to this, the corrugated board with such a protective layer has a longer service life and better resistance to mechanical damage.
Polyster plated profiled plaster - price and purchase
As already mentioned above, a polymeric profiled sheet with different types of protective coating differs not only in characteristics but also in cost. And quite significantly - in some cases, even several times.
So, for example, let's take a polyester profiled sheeting with a polymer coating - the price of grade C21-1000-0.5 on average is 250-270 rubles per m², while with a protective layer of pural, a similar brand will cost 550-600 rubles per m² .
Despite the fact that such costs, in the long run, pay off with a long service life and reduced maintenance costs, due to their cost, the most wear-resistant polymer coatings did not become widespread in the CIS. They, as a rule, are applied in territories with aggressive environmental conditions.
The table below shows the average market price for a profiled sheet with a polymer coating of various types for three common grades of corrugated board.
Buy corrugated board with polymer coating can be in any construction hypermarket, from the manufacturer or an authorized dealer, as well as in the construction market and in the online store. However, before buying, you should make sure of the quality of the material. To do this, follow a few simple rules:
- Visually inspect the surface of the profiled sheet. It should be smooth, without dents, the paint should be uniform, without streaks, and the edges - cut smoothly, without burrs.
- Demand from the seller a certificate for the painted corrugated board with a polymer coating. This document alone does not guarantee quality, but in its absence, it is not recommended to buy material.
- Specify what warranty is provided by the manufacturer. If it is 1-2 years old or missing at all - this is an obvious signal of poor quality of the material.
- Slightly bend one of the sheets along the corrugations - even the coated polyester should not crack at the same time. If they are formed, then you have a poor-quality product.
- If possible, buy corrugated board either directly from the factory, or from authorized dealers. This will greatly reduce your chances of purchasing poor-quality material.