A mixture of cement and sand is a component of many solutions and dry mixtures. Both sand and cement can be used in concrete or mortar , plaster and the like.
Effect of a cement-sand mixture on the properties of the final product
The proportions of cement and sand directly affect the properties of the mortar or dry mix. Moreover, the influence is multidirectional, since cement is an astringent component, and sand is a filler. Accordingly, increasing the proportion of cement in the mixture:
- Increases the speed of setting the solution;
- Strengthens strength (up to a certain limit);
- At some point, excess cement leads to excessive drying of the mixture and the appearance of cracks;
- In addition, cement is more expensive than sand, so increasing its share increases the cost of the finished mixture.
Sand, in turn, provides a solution:
- Plastic;
- Hardness;
- However, exceeding the proportion of sand in comparison with cement over reasonable limits leads to loss of strength and crumbling.
Mixture consumption per cubic meter
The consumption of cement-sand mixture per cubic meter of solution (no matter what - for floor screeds or for the formation of concrete structures) depends on the proportions optimal for a given type of solution. Flow rate variability refers solely to the weight of the mixture, since its volume will correspond to the volume of the finished solution, adjusted for water.
Note that adding cement to the sand practically does not increase the final volume of the mixture. That is, if you add 300 kg of cement to the cubic meter of sand, the volume of the mixture will still be 1 cubic meter. The reason is that the cement particles are very small, and easily occupy the space between the sand particles. This is what determines the homogeneity and monolithicity of the final solution.
Suppose that we want to prepare a solution of brand M200 on cement M500. The optimal proportion of such a solution is 1 to 3, that is, the proportion of cement is 25%.
The cubic meter of sand weighs approximately 1400 kg. Proceeding from the fact that we need 25% of cement, it will be approximately 350 kg. The final weight of the cement-sand mixture will be 1,750 kg. It is this weight of a cubic meter of a mixture that is considered average.
Do not forget that we are talking about a cubic meter of dry mix. The volume of the finished solution will be higher due to the addition of water.
What factors affect the consumption of the mixture?
In fact, the cement-sand mixture is a worker solution (if you do not take into account water and various modifying additives). Accordingly, the consumption of the mixture depends primarily on the scale of work and the need for a solution.
The weight of the cement-sand mixture is affected by:
- proportional ratio of sand to cement (the higher the proportion of cement, the heavier the mixture);
- properties of sand (sand with coarse particles will be heavier than fine sand).
The working consumption of the cement-sand mixture is already dependent on the specific type of work and its characteristics. For example, the consumption of the mixture on the floor screed depends on the thickness of the screed. With increasing thickness, you need more mortar, respectively, more cement-sand mixture.
The installation of a cement-sand floor screed is the most proven and reliable way to level the surface. With its help, the floor not only aligns, but also additionally gives the necessary rigidity, which will be required in the future. You can buy in the building stores a ready-made mix to arrange the screed, or you can cook it yourself.
Composition and proportions of cement-sand screed.
The cement-sand screed includes, as the name implies, cement, sand and water. For plasticity, you can add a plasticizer. Proportions for obtaining the required grade of cement-sand mixture: for 1 bag of cement (50 kg.), It is necessary to take 150 kg of sand (about 10 buckets of 10 liters) and about 25-27 liters of water. The amount of water depends largely on the moisture content of the sand. The higher the humidity of the sand, the less water is required.
Consumption weight and density of cement-sand screed.
The density of cement-sand screeds directly depends on the choice of materials used. Subdivided into light and heavy. Easy screed - density up to 1400 kg / m3, heavy - more than 1400 kg / m3. The density of the composition is greater, the higher the strength and frost resistance. With the use of compositions of any kind. The consumption of cement-sand screed is not difficult to calculate, based on the manufacturer's data (see the back side of the bag). The cement-sand floor screed consumption is approximately 20 kg per 1 m2, with a layer thickness of 10 mm. In this case, the weight of the cement-sand screed will be approximately 15-20 kg. for every centimeter of thickness.
Minimum and maximum thickness of cement-sand screed.
The recommended minimum thickness of cement-sand tie is 30 mm. If the minimum thickness of the screed is less, then there will certainly appear small cracks. The maximum thickness of the cement-sand screed is limited only by the bearing capacity of the overlap and the increased over-expenditure of the material. With a thickness of 80-100 mm, the weight of the screed will reach 150-200 kg per square meter, which is not always acceptable. The optimum thickness, recommended by specialists, is 30-50 mm.
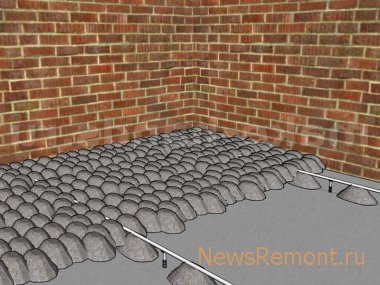
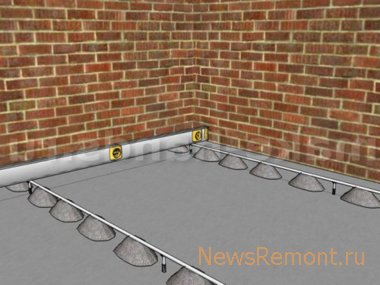
The device is cement-sand floor screed.
The installation of a cement-sand floor screed begins with the filling of a mixture of shovel space between the previously installed beacons. Laying cement-sand screed must be done quickly, so that the mortar prematurely does not freeze. If the work is done alone, then you need to fill in one strip. After filling the solution stretches the rule. At the appearance of small pits and holes there it is necessary to throw the solution. The screed is tightened by the rule several times until an even surface is obtained. Screw ready. It remains only to wait until it dries. In the drying process, to prevent the appearance of cracks, it is recommended to water it with a small amount of water.Cement mortars, like pure cement, are often used for construction purposes. It has several advantages over other building materials. That is why, it is very important to understand the calculation of the mass required for laying a strong and durable foundation. The main indicator of the calculation is the volumetric weight or the specific gravity of the cement.
Factors affecting the change in cement density:
Specific gravity of cement mixture
Name / grade of cement / mixture | Specific weight (kg / m3) |
M 100 | 900 |
M 150 | 900 |
M 200 | 900 |
M 300 | 1100 |
M 400 | 1100 |
M 500 | 1100 |
Sand and cement mixture | 1700 |
Cement-pearlite mortar | 1000 - 1400 |
Cement-slag solution | 1000 - 1400 |
Cement, in the process of transportation, has the property of enriched air. In this case, immediately after unloading, bulk cement weightwill be 1200 kg / m³. Over time, the material will begin to be compacted, and its density will return to normal - about 1600 - 1500 kg / m³. There are situations when the cement is filled with moisture, and becomes too dense, reaching the limit values of 3100 kg / m³. The main factor affecting the variability of the density is the size of the cement crumb.
At control purchase of materials, it is very important to pay attention to this indicator. Although, unfortunately, to check the density of matter is not easy. But there is an average figure that suppliers should adhere to - 1300 kg / m³.
During mixing the mortar, it is possible to compact it. To do this, you need to fill the tank with coarse sand (sealant), then sprinkle the medium, and at the end, the smaller one.
Calculation of the volumetric weight of cement for construction works
When working with building mixtures, incorrect calculations of the requirements for materials, can affect the productivity and quality of the result. Specific weight of cement,as well as any other bulk building material, is defined as: M / V, where M is the mass and V is the volume.
The resulting ratio of mass and volume, measured in - kg / m³. A good example of HC calculations of known brands in the table above.
As can be seen from the table, specific weight of cement m 500, m 400 and m 300, equals or exceeds the indicator of 1100kg / m³. In production, there is a system for controlling the volumetric mass of matter. It helps to establish the desired value, using various types of additives (barium).
To create a high-quality and durable foundation for any finish flooring, you need to find out the carrying capacity of the entire structure.
The weight of the screed is large enough, and therefore it exerts great pressure on the base of the structure.
In those cases when the work is done using not a ready-made mixture purchased in building stores, but a composition prepared independently, precise calculations should be made taking into account the specific features of the materials used.
Selecting materials and preparing the mixture
DSP or cement-sand screed is a necessary and rather simple way of leveling surfaces. To create it, you need sand, cement and water. The number of each component depends on their characteristics.
So, for example, if cement M150 is taken, then sand will need three times more. If M500 cement is used to prepare the mixture, the sand is taken in accordance with the proportion 1: 5.
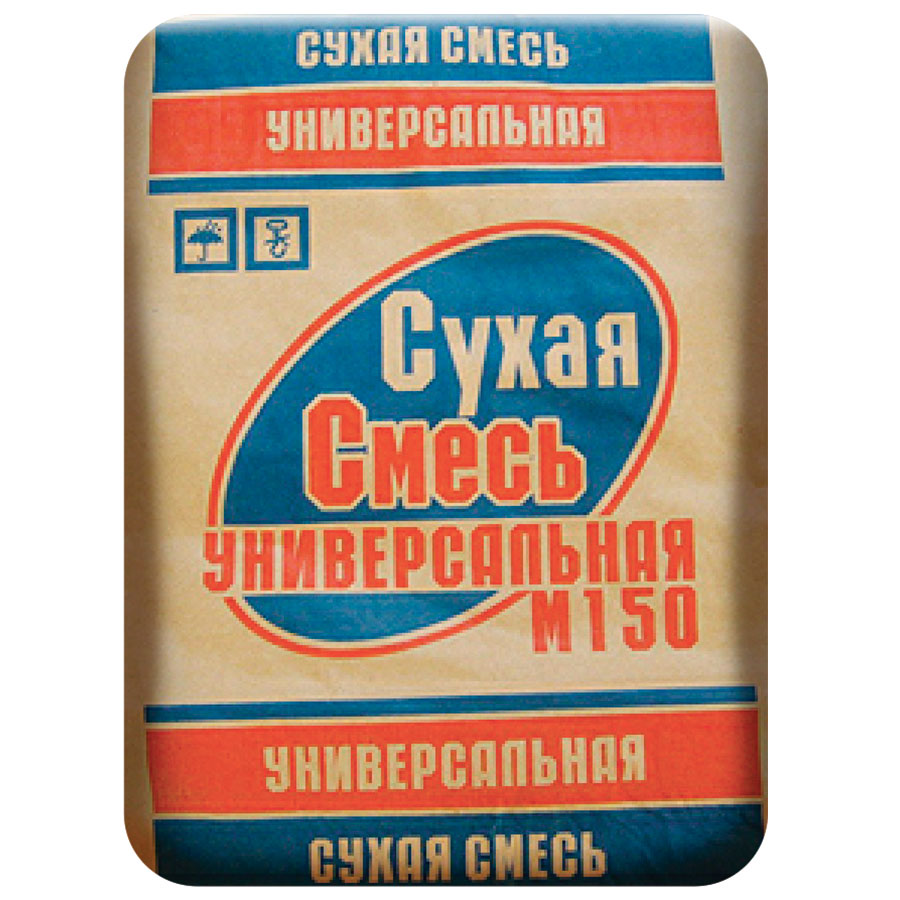
The optimal use of M 150 cement is recognized, therefore 150 kg of sand will be needed for this material weighing 50 kg. As for the amount of water, it depends on the moisture of the sand.
You can prepare a quality solution by taking:
- 1 bag (50 kg) of cement;
- 15 ten-liter buckets (150 kg) of dry sand;
- 27 liters of water.
The introduction of wet sand will reduce the water volume to 25 liters.
The weight of the cement-sand screed depends on the pressure it will have on the base of the structure. Accordingly, before proceeding with the work, it is necessary to clarify the thickness of the layer being poured.
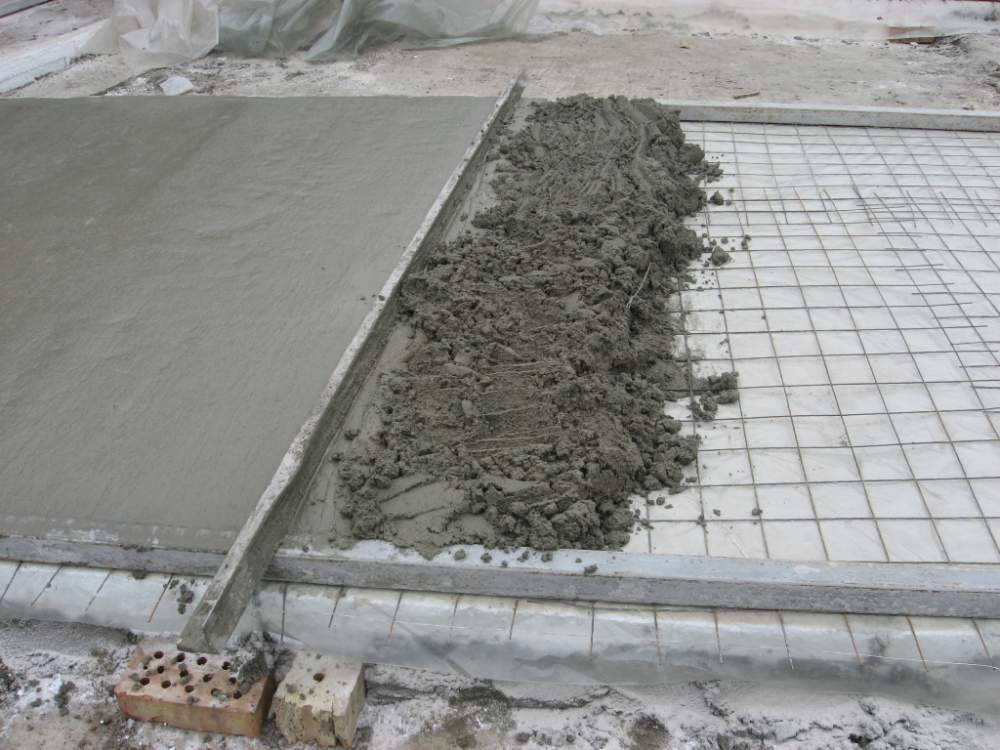
The minimum thickness of the screed is 0.3 cm. Otherwise, after curing the solution, the surface will crack. Exceeding the maximum thickness of 0.5-1 cm leads to exceeding the permissible load on the substrate.
If the given value reaches 8-10 cm, then the weight of the cement screed per square meter is about 150 kg. This is unacceptable and therefore experts recommend not to exceed the set parameters.
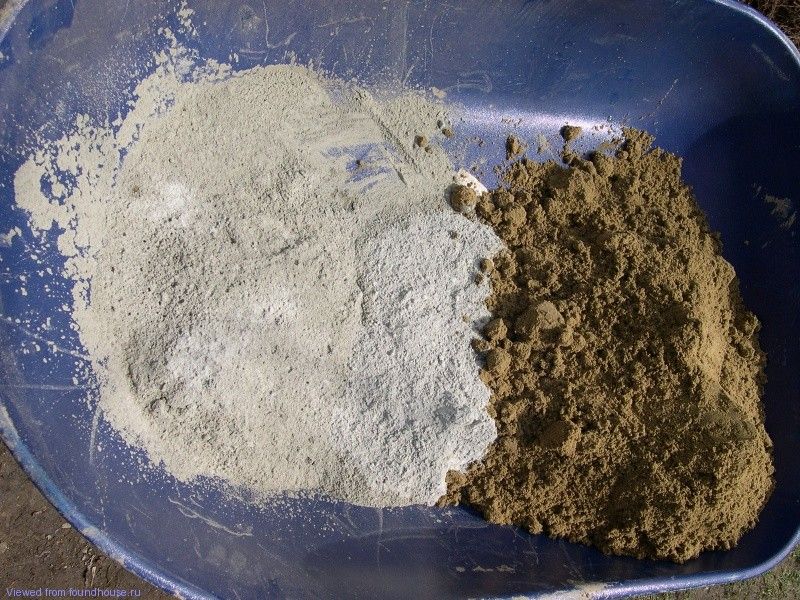
When creating a cement-sand screed 1 cm thick, its consumption will be at least 20 kg per square meter. At that, for 1 cm², its weight will be from 15 to 20 kg.
It is necessary to take into account during the creation of a cement-sand screed density of the composition, which depends on what materials will be chosen by the masters.
In this parameter, the compositions are divided into:
- Light, density of which does not exceed 1400 kg / m³.
- Heavy screeds, the indicated figure is much higher than 1400 kg / m³.
If the technology is strictly observed, the specific gravity of the sand-cement screed, depending on the given characteristics of the sand, will not exceed the permissible limits.
In accordance with GOST 8736-77 one cubic meter of sand should contain no more than 1600 kg, and its specific weight should be 1550 to 1700 kg / m³. For more information on how to make a solution, see this video:
Calculate the consumption of materials using the existing formula and reference data. When working with a cement grade M 400 for a 3 cm thick screed in an area of 50 m², you need a lot of cement and sand, which can be learned by simple calculation:
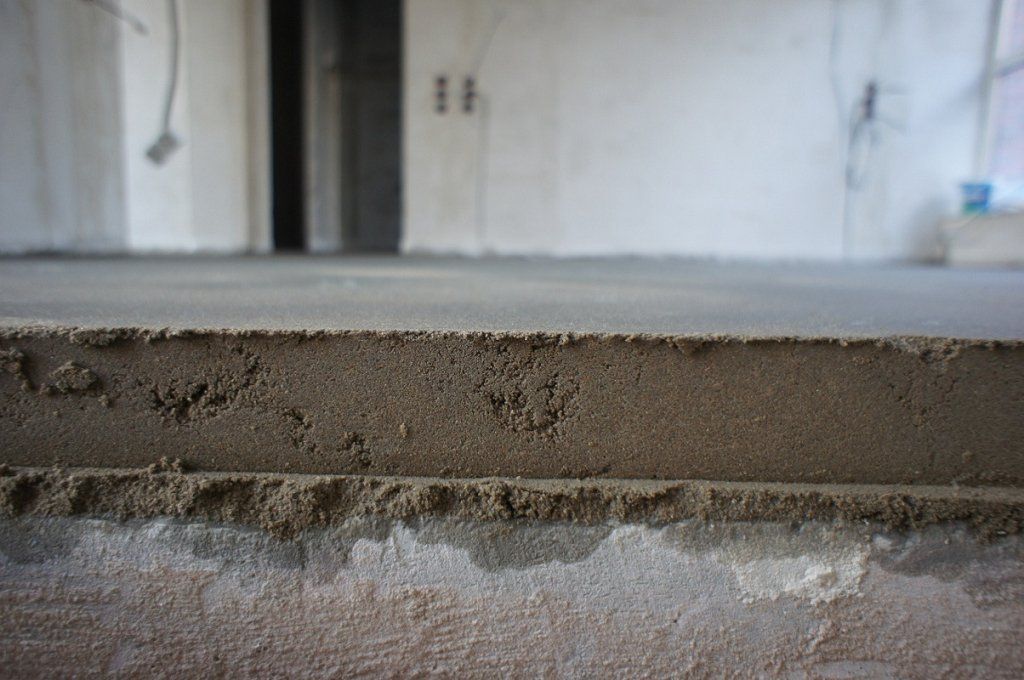
The volume of water is determined from the calculation of 0.5 liters per 1 kg of cement. Accordingly, 4875 × 0.5 = 2437.5 liters is required.
Observance of all specified norms will allow to execute works qualitatively and to create the strong and reliable basis for a finish covering.
The order of performance of works
Start the action with the preparation of the ground.
To do this, the floors are cleaned from the previous floor covering, free the building from debris and put up building beacons, determining the horizon using a leveling tool.
Arrangement of sand-cement screed is possible in any premises, base temperature in which does not fall below +5 ͦTelsia.
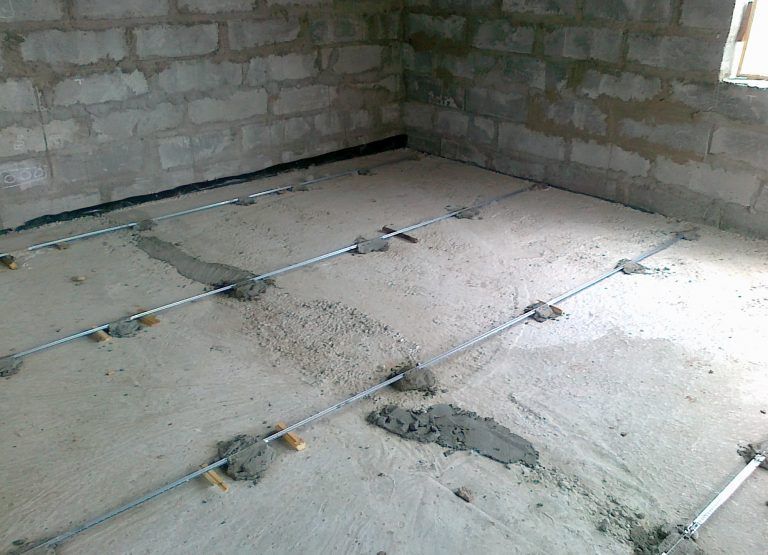
Lighthouses are installed on a pre-laid layer of waterproofing, which can be used as a polyethylene film. The edges of the canvas are planted on the wall so that they protrude on the level of the screed.
Fill the screed from the most inaccessible places of the room, but if the door is provided in it, it is important to make sure that the doorway is not blocked.
After the solution to which the beacons are solidified, the prepared mixture is poured onto the base, filling it with one strip. With the help of the rule, the solution is leveled, and only after the first strip is ready, proceed to pour the solution into the second. After 12 hours, remove the beacons, fill the space with a solution, which will take about 15 hours to fully solidify.
Now prepare the trowelling mixture and perform manipulations related to surface troweling. It will take a dry or wet mixture consisting of equal parts of sand and cement. Rubbing the surface with a special technique or manually using a polisher or float. All the details of the process of pouring concrete on lighthouses, see in this video:
After the completion of all the work, a smooth, slightly rough surface will be obtained, which must be rolled with a damp roller and covered with a polyethylene film. Moisten the screed for at least seven days, after which the film is removed.
Density of cement screed. Weight of solutions and inert in m³ for materials used by us in the device floors, values in a dry state. Standard screed solution, lightweight with perlite, polystyrene granules and heavy granite screening.
Standard solution. The density of the semi-dry cement screed in the standard preparation of the solution varies in the range of 1900-2000 kg / m³. This type of solution is the standard that we prepare and use in the screed device for semi-dry technology. Such a solution consists of inert materials: Sand with a specific gravity of 1550-1650 kg / m³, depending on the sand fraction and the size of the aggregate. Cement - binder, density (average value) 1500 kg / m³ with a flow rate of 375-400 kg. ¼ to the sand. Fiberglass - reinforcing additive - 900 gr. per m³ of solution. The weight of the screed 1 cm thick at this density of the solution is 20-21 kg. per m²
The result of the test, in this example, the density of the solution is 2066 kg / m³
(opens in a new window)
Density of cement screed - 1900 kg per cubic meter
Density of cement screed with heavy filler, granite screening
Heavy solution. Density of heavy solution with fine gravel filler up to 16 mm. This type of heavy cement mortar, which is used in semi-dry technology, is identical in composition to that of the basic composition of the solution, with the exception of heavy filler from gravel, we usually use granite screening of the fraction 5-10 mm. The density of the granite dropout varies from 2100 to 2400 kg / m³. From such a solution, we perform a semi-dry screed for rooms where high loads are expected in the operation of the floor and high strength, example garage-parking . The solution with the introduction of filler granite chips has a density of 2300-2400 kg / m³. The weight fraction of granitic screening in 1 m³ of solution is from 300-400 kg. The weight of a concrete screed with a heavy filler 1 cm thick is 23-24 kg. per m²
Light types of solutions, perlite, polystyrene granules.
Light solution. Mortar for screed with light filler polytherm, polystyrene granules - a light solution type polystyrene concrete. This type of filler we use in 2 versions, as a separate filler in cement mortar to facilitate the specific gravity of the solution, in the second variant as the main filler with the cement binder.
1 Construction option. A light mortar with a filler is prepared with a density of at least 600-700 kg / m³. This type of lightweight mortar is used in most cases on roofs over concrete slabs without loss of bearing capacity under the deposited roll-up waterproofing.
2 The variant is heat-insulating. Lightweight polystyrene concrete solution is used as an alternative to expanded clay as a light basis before the device of a semi-dry standard screed in cases where the floor needs to be raised to a height of more than 100 mm, including on problematic bases with low bearing capacity. Also this kind of solution has good thermal insulation characteristics at a density of the D150-D400 solution and is used by us as a heater. More about polystyrene, wider destinations on the following pages " lightweight construction of floors » « material characteristics «
As an alternative to a lightweight filler, perlite can be used; this material is used as a subbase under the floor for the screeding process, and also as a filler in the cement slurry. An example of the use of perlite, see the publication on our work on the installation of floors at the construction site of the House of Culture in DK Marfino floor screed with perlite