The complex of works on waterproofing includes the preparation of surfaces. The bases are cleaned of debris, the places of chips and cracks are leveled. All this leads to the formation of small particles of dust, which can not be completely removed from the surfaces. Dust hinders good adhesion of waterproofing materials, and as a result, the finished coating serves less, needs repair or replacement in the past. To prevent dust formation and improve the adhesion of waterproofing agents to the substrate, a special primer compound is used.
Primers are not only building, they are used in a variety of areas - for cars, getting rid of the fungus, etc. The purpose of the primer can be any, and the action is always approximately the same: the material impregnates the substrate, binds and glues small particles on its surface. This property of primers is used for anti-corrosion, anti-dust protection, gluing insulating materials on concrete, reinforced concrete, metal or wood.
Primer application for waterproofing
Primers are made on the basis of various substances - bitumen, polyurethane, epoxy. Bitumen compositions are widely used in construction. They penetrate deeply into the structure of building materials, quickly dry out and compact the rough surfaces. After drying primers lose sticky properties, create a durable, resistant to external influences coating. Due to this, they can be used for hardening roads, gluing of roll waterproofing, protection of porous surfaces, pipelines.
For the convenience of buyers, manufacturers produce primers in two forms - ready-to-use (standard) and concentrated. Finished primers do not require any additional manipulation, except for thorough mixing. Concentrates are much more convenient in storage and transportation. They are often purchased by developers who require a large number of building materials. Such primers are diluted with solvents in proportions of 1: 1.5 or 1: 2, depending on the purpose and base material.
Anticorrosion protection of pipes with a primer
Antifungal primer compositions
Fungus - scourge of premises with high humidity. This is not only an aesthetic problem, because pathogenic organisms can cause many serious human diseases - bronchitis, conjunctivitis, allergies. Influencing the structure of building materials, it worsens their performance properties.
If you do not get rid of the fungus, it will spread and eventually become a threat to the building and the people who are in it. Effective means - antifungal primer. This is a composition with an antiseptic, which treats the surface at the first signs of the appearance of the fungus.
In order for the solution to penetrate the materials well, it is necessary to completely remove the finish, carefully smudge the places where there is a fungus, and for the new coating, use facing materials and glues with antifungal additives. If the instructions to the staff have a recommendation to repeat the treatment, it must be done in due time. For the care of surfaces it is recommended to use disinfecting household chemicals.
As for reliable brands of antifungal primers, it is possible to choose "Fongifluid" from ALPA or one of the means of TIKKURILA ("Senezh Effo", "Homeenpoisto"). When buying the product, you should carefully read the manufacturer's recommendations, since the composition of the primers may vary depending on the type of surfaces for which they are intended.
Antifungal primer Ceresit
Properties and benefits of bituminous compounds
Primer is an emulsion based on bitumen and organic solvents. The properties of the materials of each particular brand depend on the field of application, purpose. Bituminous primers are used for both external and internal works.
Their main advantages:
- High hydrophobicity. Building materials impregnated with primers, do not absorb and do not pass moisture, which significantly affects their wear resistance and lifetime.
- Quick drying. The primer dries quickly - from 1 to 5 hours. If the waterproofing works are carried out in cold weather, the complete drying may take longer. Therefore, experts do not recommend applying bituminous primers at temperatures below 15-20 degrees.
- Resistance to temperature changes. The thin elastic coating, which is obtained after the primer has dried, is elastic, it does not burst when the temperature of the environment changes. The material retains its properties at a temperature of -50 to 120 degrees.
- Versatility in application. Construction primers are used for a variety of purposes. They can be applied to sand-cement screed, concrete, roofing material, metal or wood.
- Economical. A relatively small amount of primer is required to coat surfaces. Taking into account the quality of the preparation of the base and the acceptable price of the material, this is very advantageous. In addition, primers are easy to prepare on their own, which saves even more.
Technique of manual surface treatment with primer
6 basic rules for working with primers
- Primers on bitumen base are not used at low temperatures. Declared by the manufacturers the minimum temperature is -20 degrees, but in practice it is better not to start work if it is below -15.
- The surface of the substrate must be perfectly clean and dry. If it can not be dried, you should buy a special compound that can be used on wet surfaces.
- For normal bonding with the substrate, the primer temperature must be at least 10 degrees. It can be slightly heated, but not overheated (maximum - 40 degrees). Do not use near fire sources.
- Bituminous materials evaporate until completely dry, so they can be harmful to health. Most often they are used for outdoor work, and builders themselves are in the open air and are not endangered. If you have to work indoors, you need to ensure quality ventilation.
- When working with bituminous compounds, you should use protective clothing, appropriate protective equipment to protect the skin, respiratory system, mucous membranes.
- Store the material in a dark dry place at a temperature of -20- + 30 degrees. The maximum shelf life is 1 year.
Ready-to-use primer "TechnoNikol"
How to prepare the bituminous primer
The technology of preparation of bituminous compositions is not difficult, it can be mastered by any developer. The primer is prepared immediately before use, so that it does not freeze and easily lays on the surface to be treated. The composition is undesirable to prepare for stock and, moreover, to freeze, because this can affect its properties.
The first way is cold
There are two main ways to prepare a primer - cold and hot. The first is used if the developer has nowhere to hurry and he has at least 1-2 weeks. As a solvent, low-octane gasoline can be used, brands AI-80 or AI-72 are suitable. It is poured into a large tank and laid pieces of bitumen. The rest is a matter of time.
Bitumen dissolves in gasoline in about 7-12 days. In many respects it depends on the temperature of the environment. To accelerate the process, it is desirable to mix the bitumen. It is very important to hermetically close the container in which the mixture is located so that the gasoline vapor does not evaporate. A sign of the primer's readiness is the complete dissolution of the bitumen, the transformation of the composition into a homogeneous mass.
Applying primer to the concrete floor
The second way is hot
Most often, a hot method of primer preparation is used. To do this, pieces of bitumen are put in a container and "boiled", i.e. heated to the boiling point. As a source of fire you can use an ordinary fire. When the bitumen boils, it is slowly and gently poured into a tank of gasoline.
- for concrete - 1: 2;
- for metal - 1: 3.
Heated bitumen
When preparing the primer, be sure to pour boiling bitumen into the gasoline, although many do the opposite. The prepared mixture must be thoroughly mixed until uniform. The composition should not be solid pieces.
Master class on hot preparation of primer
The variety of types of primers is enormous. Each of the primer compositions has its own purpose and is able to improve the characteristics of building materials, extend their service life. When choosing a primer, it is important to correctly determine the desired properties, to find the product from a good manufacturer and follow the recommendations given on the package or in the instructions to the primer.
Epoxy primers (primers) - one of the best options for primer mixes for preliminary preparation for the finishing of concrete bases. The use of soil allows to achieve a substantial strengthening of the base of concrete, but the mixture is suitable for processing other types of surfaces: it will eliminate cracks, roughness and roughness on the basis of wood, plaster, plastered.
The peculiarity of epoxy primer is that it is produced on the basis of epoxy resins and therefore in the finished form the solution acquires unique properties, a detailed review of which will be presented below.
So it looks like an epoxy primer for concrete
Types of epoxy primer for concrete
Epoxy solutions for concrete are graded into two main types:
1One-component mixture
Single-component solutions can be used on various types of surfaces, including bases with poor absorbency. With their preparation for work there will be no trouble: the ground is sold in ready form and before processing the basis it will only be necessary to mix it.
1Two-component mixture
Two-component epoxy primers are used most often for the priming of concrete surfaces, on which it is planned to make liquid floors in the future. The soil before the work will need to be prepared by mixing two components: a base base and a hardener.
Specifications
Above it has been said that epoxy primers are valued in the construction market due to their unique properties. The technical characteristics of compositions based on epoxy resins are as follows:
- Excellent adhesion, allowing to prepare for the subsequent finishing of different types of bases: from concrete, brick, metal, wood, ceramics;
- High moisture protection;
! The moisture-protective properties of the epoxy primer will be particularly relevant when working with wood. Due to this quality of the soil, it is possible to refuse the purchase of special impregnations for wood and thereby reduce the cost of purchasing consumables.
- Fire safety. Working with the composition, you can not be afraid that the surface will ignite;
- The finished coating will be extremely strong and resistant to wear and tear;
- Epoxy soils have a deep penetrating power and therefore perfectly strengthen the base from the inside. Using the mortar, you can get the highest quality finish and do not worry that the finish coat is cracking or peeling off.
The epoxy primer dries out about 24 hours after application, but it is important to know that it is highly undesirable to apply it on wet surfaces, otherwise there is a risk of deterioration in the adhesive properties of the mixture.
It should be noted that these technical characteristics will only have high-quality epoxy primers, and therefore it is important to know - how to choose the right material. To perform a significant amount of work, it is best to purchase prime. Soil in this form will be cheaper. But if the work is to be done small - it will be more convenient to use the aerosol release form of the primer.
When choosing an epoxy primer mixture for a concrete base, always carefully study the composition of the solution, see the expiration date and visually assess the type of soil.
! Epoxy primer mixtures should never be used on wet surfaces. The permissible moisture content of the substrate is not more than 4%.
The process of applying the epoxy solution to the substrate will consist of the following steps:
- Preliminary preparation of the substrate, which must be thoroughly cleaned of dirt, dust, old coatings. The basis is necessarily cleaned from any oil and grease stains, traces of substances of different origin. If necessary, the substrate can be washed, but in this case, before starting the priming, it must dry completely.
- The technology of preparing the epoxy primer for work will depend on what kind of material was purchased. One-component mixtures are simply thoroughly mixed, for a two-component primer another preparation procedure is provided. Open the package with the resin component and mix it with the hardener. The proportions of the solution are given by the manufacturer in the instructions for use, and you can not reduce or increase them at your own discretion! Such amateur activity is fraught with the loss of soil useful properties.
- The components of the solution are mixed by a mechanical stirrer until a uniform consistency mass is obtained, which must be used immediately.
- The epoxy primer can be applied with a variety of tools, instructions on what type of tool is best used in the work can be found in the instructions for a particular kind of solution. Most often the manufacturers advise to distribute the primer over the surface with rollers, spatulas, graters, spray gun.
- The material is poured over the base with a thin layer and neatly distributed by the manufacturer's recommended tool.
! Work with epoxy primers should be quickly and during the work to avoid the formation of puddles.
- Two-component solutions quickly set, so after preparation, the primer should be applied to the substrate as quickly as possible - in about 20 minutes. Therefore, it is not recommended to prepare the solution in large quantities.
- High temperatures can adversely affect the useful properties of the soil mixture, so in hot weather, the solution is always prepared in a small amount, which is required for a specific stage of work (portions of not more than 3 kilograms).
Freeze the ground for about a day. On the admissibility of walking on the created coating, it is necessary to clarify the information in the application instruction to the specific brand of the primer.
The need for repeated priming with an epoxy primer is determined visually. If the solution is absorbed completely (this is possible with increased porosity of the base), without forming a noticeable and shiny film or on the surface of the coating, bubbles and holes appear - it is required to apply the solution to at least one more layer.
When working with a solution, you must follow certain rules of work. The skin and eyes should be protected with special clothing, gloves and glasses. If the epoxy primer is used to treat areas in an enclosed space, it is important to ensure good ventilation in the room.
Epoxy primers for concrete - a material, the use of which helps to properly prepare the surface for the production of further finishing works. The finished base is obtained by reliable, heavy-duty, resistant to wear and the action of negative environmental factors. Therefore, epoxy primers remain in demand on the construction market, despite the relatively high price of the material.
What is a primer?
Primer is a material used to pre-prepare the surface before applying any coating.
More primly, the primer is a primer. True, some LMC sellers are often referred to as primers and different impregnations. But the impregnations are then more correctly attributed to the sealers (English sealer - impregnating sealing material).
In accordance with the base material, the primers are also called: a polyurethane primer, an epoxy primer, a bitumen primer, and the like. For example, a polyurethane primer PS-Grunt we can say that this - polyurethane primer for concrete.
When polymer floors are used, primers are used to improve the adhesion (adhesion) of the substrate to the finish coat.
Always remember that the key to success can be only mandatory quality preparation of the foundation. Therefore, primer primers play a very important role in construction. In each specific case, you should apply for instructions and explanations to manufacturers and suppliers of paints and varnishes.
Primers primer - Online site.
The site focuses on materials and technologies for the device floors. A lot of information is devoted to the correct preparation of the surface, which also tells about primers primers (what is a primer, why a primer is needed, etc.).
We hope, sections of the site will help you make the right choice of paint and varnish.
The primer for the filler floor (primer) must perform three main functions:
- hardening of the surface layer;
- sealing of pores (decrease in absorbency) and filling of small cracks and shells;
- increasing the adhesion of the polymer to the base.
Compositions of polymer primers
The main criterion for choosing a primer is a complex of properties of the base surface. Nevertheless, the best result is a primer under the filler floor , the corresponding material used to fill the layers.
Consider the main types of compositions used.
Epoxy primers
Suitable for preparation of surfaces from ordinary concrete, its porous modifications, mixtures of concrete with asphalt, as well as wood and other materials (depending on the brand of a particular composition). It is believed that it is the epoxy primers that provide the best hardening of concrete screeds.
Primers of this type, as a rule, have a two-component base (resin and hardener). Depending on the chemical composition, they are characterized by different viscosities. The grades intended for deep impregnation have a lower viscosity. The advantage of thicker compounds is that it is better to use them to repair the puttying of cracks. In addition, viscous primers provide a good preliminary leveling of the surface.
Primers based on epoxy resin are used for both epoxy and polyurethane self-leveling floors. However, combining different types of chemical bases is only permissible within the materials of one brand, if this is directly stated in the technical characteristics of the material. The use of epoxy primers as a preparation of the surface for cement-sand filler floors is economically justified in only one case: to harden a concrete screed of poor quality with a brittle surface layer.
Polyurethane primers
Used as a preparation of the substrate for applying layers of polyurethane self-leveling floors. Like epoxy primers, suitable for all basic types of substrates - concrete, asphalt, cement-sand screeds and metal surfaces.
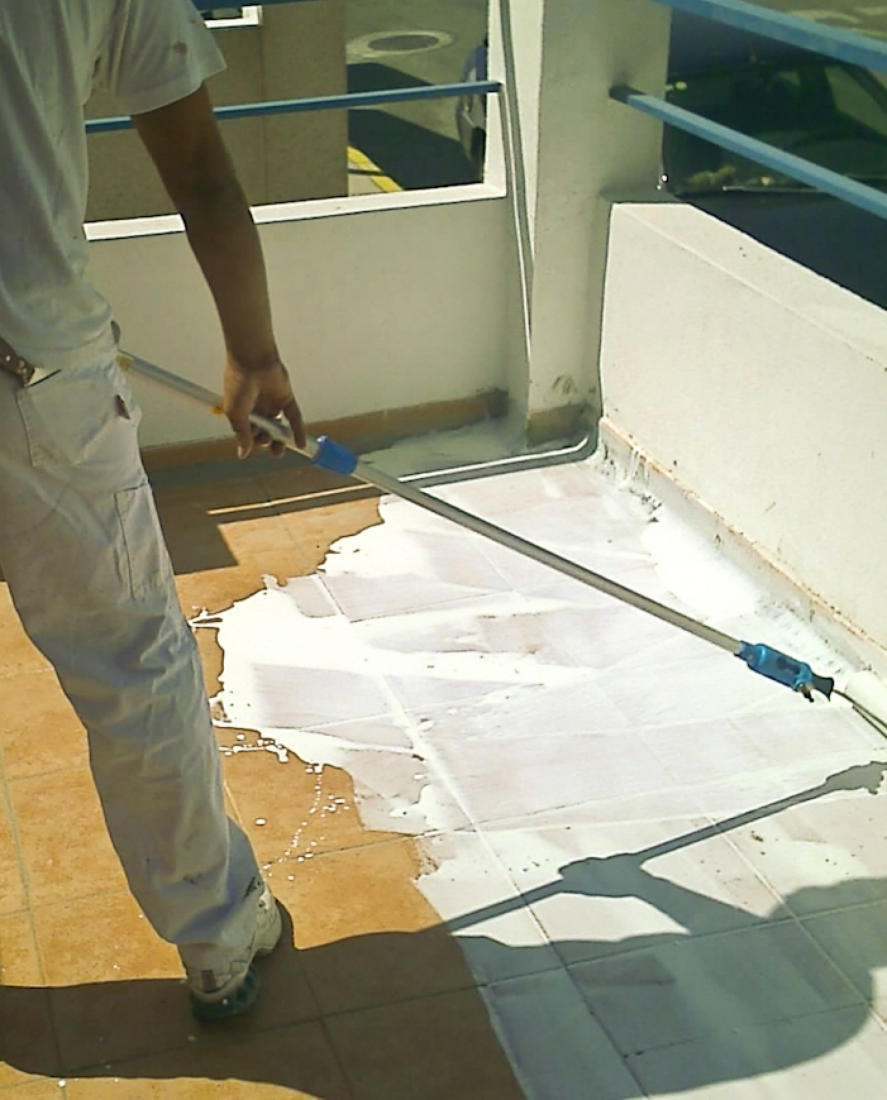
A special feature of polyurethane primers is their effective use on ceramic tile floors. Inferior to special epoxy impregnations of deep penetration in cases of insufficient strength of base concrete. If the compressive strength of the substrate is less than 20 MPa, as a rule, the profile epoxy composition is used as the first primer, and then the polyurethane primer is applied.
Acrylic and latex primers
Acrylic compositions are considered the best types of primers for the preparation of wooden surfaces and screeds that contain a gypsum binder. When working on concrete, acrylic primers are inferior to epoxy and polyurethane compositions in hardening and impregnating properties and are almost not used for sealing cracks in concrete. However, with good quality screeds, acrylic based compounds work well as a preparation base for all kinds of self-leveling floors, providing a high degree of adhesion.
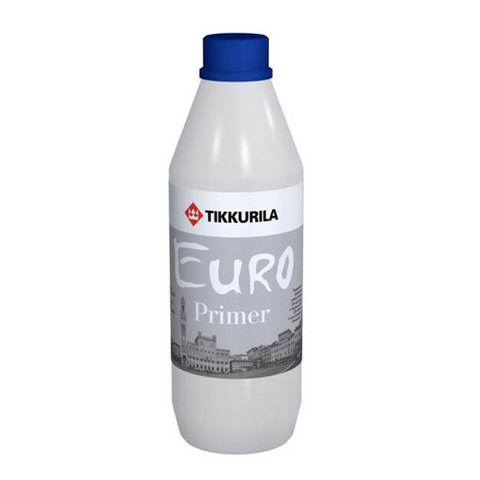
Prior to use, acrylic primers are found in combination with acrylic and cement-sand bulk floors. Popular primers such as "concrete-contact", depending on the brand and manufacturer, have an acrylic or latex binder. As filler, quartz sand of fine fraction is used.
Methyl methacrylate primers
Primer for flooring under the filling floor based on methyl methacrylates is usually included in the installation kits based on this chemical base. Like all materials of this type, it has a very high drying speed and final hardening. It has high covering and adhesion properties, but is inferior to epoxy and polyurethane compositions in terms of penetration depth into concrete. The use of methyl methacrylate primers complete with epoxy and polyurethane floors does not make economic sense due to the high price of the material. However, in case of need for emergency repairs, methyl methacrylate repair compounds may be used as a local repair of liquid floors of a different chemical composition.
Priming technology
Regardless of the type of primer immediately before application, the following steps are performed:
- Diagnostics of the base. Depending on the properties of the concrete or other type of substrate, as well as the expected type of filler floor, the primer grade is chosen. Sometimes it is necessary to use two types of primers on one base.
- Preparing the base. It consists in the removal of cement milk, contamination, repair of cracks and shells, grinding and dedusting.
- Application of priming compositions. All types of primers can be applied with a sprayer, roller or brush. The brush is suitable for local repair in small areas.
- Application of the second layer. The decision to apply the second layer is adopted depending on how evenly the drying goes on. Accelerated drying in some areas indicates increased porosity and requires repeated primer treatment throughout the floor surface. If it is stipulated in the primer instruction, the second layer is applied without fail.
The main differences in the technology of applying primers are the preparation of mixtures for work and the time of their drying.
The epoxies and polyurethane primers last the longest and polymerize - from a few hours to two days. The time for the application of the second layer is determined depending on the degree of polymerization of the resin: the surface must be no longer sticky, but not yet completely solidified. Pouring the first main layer of the filler floor is, as a rule, after the complete polymerization of the primer.
The drying speed depends on the temperature and humidity of the air in the room.
Acrylic and latex primers, in particular primers of the "concrete-contact" type, dry for 6 to 24 hours. The time intervals between the application of repeated layers and the beginning of the pouring of the floors are the same and take into account the complete drying of the primer.
Methyl methacrylate compounds are champions of polymerization speed: it passes in a few minutes. At the same time, high humidity and low temperature have little effect on the course of the process.
It is important to note that exceeding the time interval between priming and pouring floors is undesirable to the same extent as insufficient polymerization. After drying, the primer can lose a significant part of its properties. Dousing the overexposed primer does not ensure the restoration of its functions.
Primer consumption
The consumption of the primer under the filling floor depends on its chemical composition and the porosity of the base surface. For the first layers of epoxy and polyurethane primers, it is 250-500 g / m2. For re-coating takes less - on average, about 100-200gr per m2. The consumption of acrylic and latex primers is commensurate with these indicators.
Optional primer properties
Depending on the conditions and purposes of the work, it is sometimes necessary to choose primers with specific properties. Among such options are:
- Color primer (to prevent the transmission of the dark base surface through the single-layer polymer coatings of light tones).
- Possibility to use the composition with high humidity of the substrate.
- The ability to fill large cracks, pre-mixing the base with quartz sand.
- Increased electrical insulation properties. For use on top of current draw circuits.
Summary
Do I need to primed the floor in front of the floor? Yes, this is a necessary stage of work, regardless of the state of the base surface and the type of the proposed finish coat.
When choosing a primer, it is necessary to take into account the quality of the substrate, the type of the filler floor and the microclimate in the room.
If you are well versed in building chemistry, you can use a primer and a finishing fill of different brands and chemical compositions. However, one should keep in mind: when assembling polymeric self-leveling floors, it is better to limit oneself to materials recommended by one manufacturer. In addition to quality assurance, this will ensure that you file a justifiable claim in the event of a defect due to factory rejection, or a violation of the storage conditions of the goods by the seller. These materials are quite expensive, so it's better to insure yourself in this way.
Tehnoprok offers a universal bicomponent epoxy primer water-based, manufactured by the Pazkar Israel factory, - Epoxy Primer XL-100.
The delivery package consists of a plastic bucket of 8 kg with a primer (component A) and a metal can 2 kg with an activator (component B).
Epoxy primer is an innovative material developed by the laboratory of the Pazkar plant.
Initially, it was assumed that the field of application of this product would be the preparation of the bases before applying acrylic-polymer mastic Master Ruf and.
However, later the epoxy primer formula was modified and now it is used, incl. independently for priming various surfaces.
Epoxy primer is highly chemical resistant, therefore, materials treated with XL-100 are not destroyed and will serve for a long time.
The epoxy primer is applied by brush, roller or airless spray (this is important, - without air supply, ie with high pressure apparatus.
Epoxy Primer XL-100 provides a better adhesion of sprayed polyurethane foam, to almost any substrate, if it is pre-treated with this primer.
Epoxy primer is used as a penetrating compound to strengthen concrete and concrete structures. For example, when working.
The epoxy primer performance characteristics
Color before drying | White |
Color of the film after drying | green |
Specific gravity (density), kg / m3 | 1050 …1150 |
Consumption at a film thickness of 70 μm, g / m2 | 100 |
Dry residue | not less than 65% |
Allowable temperature range for application, deg. C | +10…+35 |
Mixing ratio, A to B | 4 to 1 |
Ratio (A + B) when mixed with water * | 1 to 1 |
Life time after mixing, h | not more than 2 |
Drying time until the touch and before the first rain, hour | 4 … 6 |
Drying time before application of 2nd layer, hour | 6 … 8 |
Final curing, day | 7 |
* A feature of the two-component epoxy primer is that it is a concentrate. It is necessary to dilute with water in a ratio of 1 to 1. That is, in fact, buying a kit (8 + 2) kg Epoxy Primer XL-100, it turns out 20kg.
Concentrate 10kg (a mixture of components A and B) is mixed with ten liters of water. Thus, the epoxy primer has a water base, which makes it an environmentally safe product. The epoxy primer is not flammable.
It should be noted that there is still a smell. Although XL-100 does not contain organic solvents, but, after all, it contains an epoxy resin. Therefore, when used indoors, ventilation is mandatory.
Surfaces to be applied Epoxy Primer XL-100, should be strong and cleaned from dust, dirt, debris, oils, etc. Concrete should be strong for at least 4 weeks. Cement film (milk), formed during the setting of concrete, will interfere with adhesion to concrete. Therefore, it should be deleted.
Preparation of a two-component epoxy primer
Prepare an empty clean container with a wide mouth, volume 22 ... 30 liters.
Pour the activator from the metal can of component B into the bucket with component A and mix with a mechanical mixer for 2 minutes. Pour the resulting mixture into a prepared clean empty container.
Add the same 10 liters of tap water. The resulting mixture of 20 liters is mixed with a mechanical mixer for 2 minutes.
Give the resulting aqueous solution of the epoxy primer to stand for 10 minutes, then re-mix for 2 minutes. The resulting composition should be used within 1 ... 2 hours.
Manufacturer epoxy primer strongly recommends not to divide the capacity into parts, use both parts of the kit completely.
It is important to first mix components A and B, and only then dilute the resulting mixture with water, and pour water into the mixture, and not vice versa!
After mixing, at a temperature of + 25 ° C, the maximum lifetime of an aqueous solution of epoxy primer is 2 hours.
The use of an epoxy primer
Brushes and rollers used to apply the epoxy primer should be soaked in a solvent and then rinsed. Likewise, if you do not rinse immediately after primer application with an airless installation, repair is required.
Excess soil should not be. If the epoxy primer is applied in excess, the surface becomes glossy, it glitters. You'll have to wait longer until the primer dries.
A task epoxy primer primer - penetrate (if the structure of the base allows) into the material and form a thin on the surface! film thickness of 50 ... 100 μm. Therefore, the consumption of epoxy primer for metal - less than, for example, for concrete.
In one pass, a film of 70 μm can be obtained, which corresponds to a flow rate of 100 g / m2. But, if the film is not formed and the entire primer is absorbed into the substrate, then it will be necessary to apply a primer coat again. Depending on the porosity of the substrate (concrete concrete - discrete), the flow rate is from 100 to 400 g / m2 of an aqueous solution of the epoxy primer.
Epoxy primer provides increased adhesion between the substrate and the material that is laid on this base, for example between the screed and waterproofing of liquid rubber or thermal insulation from polyurethane foam. This is due to the thin film formed by the primer drying out. But the film must be clean at the time of application of waterproofing or thermal insulation.
If the film is covered with dust, dirty or, on the contrary, it is thoroughly washed by rain, the reactivity will decrease. Therefore, it is recommended to lay materials on the substrate treated with a primer, no later than 2 days after priming.
Still from the limitations of this material, it can be noted that containers with components of the epoxy primer should not be frozen and should be protected from prolonged exposure to direct sunlight.