A beam as a material for building a house is chosen by many people, both professional builders and beginners. The beam is in the middle price category, it is easy to handle, the range of its application is quite wide. From this material can be executed as small buildings of economic purpose, and high-grade houses. Houses made of timber are environmentally friendly, have a beautiful appearance, if necessary the useful area of such a structure can be expanded with the help of the second floor. So, we make the second floor of the house from the bar: the pros and cons.
About what will be discussed:
Brick house
If you own a single-story brick house, and there is a need to expand the area of the house, the optimal, economically viable option is the construction of the second floor of the timber.
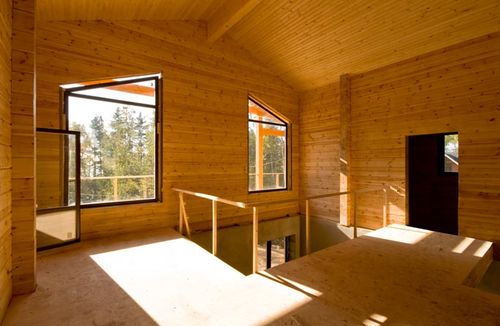
In addition to the price aspect, if you stop at the option: the first floor brick second floor of the timber, you will get a number of advantages:
- a very special atmosphere and microclimate, which are possible only in wooden buildings. It is wonderful to have bedrooms, children's rooms in such premises;
- strength. Wooden houses are durable, they will last for several decades;
- wood is very easy to process material, with their own hands, without attracting heavy equipment, you can create any shape and configuration;
- aesthetics. Wooden houses are very attractive, they are a sign of good taste of the owners.
Benefits
What are the other positive aspects of the fact that you will equip the second floor of the house with a lumber yourself? Consider the following:
- this saves the useful area of the land plot;
- possibility to equip a separate, isolated area with sleeping rooms and an excellent view from the window;
- saving time and money. You do not have to spend money on expanding the basement, wait until it freezes, you can immediately start construction work.
Choice of timber
At the moment the market of materials, in addition to the usual planed beam200x200, offers a choice of profaned and glued beams. Each of these types has its advantages, but the house of the beam on the second floor in any option will be winning.
Kinds
Planed
Traditional planed beam, which is a common log, planed from all sides, as in the photo. Controversial material, which although relatively cheap initially, is much more expensive to operate. Before lifting the beam to the second floor, please note that the material shrinks up to 20 cm, which is very important. The choice of the supplier from whom you intend to purchase the planed timber should be given special attention, since the material is bought not dried, and it dries up already in the walls. In addition, you will have to spend money on patching gaps, and decorating the walls. By the way, taking into account all the same shrinkage, finishing works are recommended not earlier than six months after construction. This, of course, is not very convenient.
Profiled
The most popular view at the moment. Also of this building material often make single-storey baths for private use. It has the following advantages: due to the fact that the surface of the beam is treated in a special way, the gaps in the adhesion are practically excluded, this makes the walls warmer (however, without special heat-insulating material, such construction can be used only in the warm season), resistant to wind. Buildings of such material are not subject to shrinkage, their walls do not need additional finishing, which significantly saves the budget.
Glued
The technology of manufacturing this kind of timber is very simple: it is made by gluing together several wooden lamellas, to add strength to the product, lamella fibers are crossed, as seen in the photo. This kind is obtained high-quality, has good characteristics, since segments of lamellas with defects are written off and not allowed into production.
Purchase
On what first of all to pay attention at purchase of a bar:
- the surface of the bar 200x200 should be as smooth as possible, without jaggies, distortions, hooks. These nuances can significantly complicate the construction;
- carefully check the timber for cracks. Even a minor split will expand over time, which can lead to rot;
- do not buy a bar with blue spots on it. Construction of the second floor from a bar of such quality is impossible, as it is already subject to internal putrefactive processes.
Installation rules
In order for the result of your efforts to please you for many years, you need to observe all the nuances when building a frame of the second floor of a bar:
- to realize the laying it is necessary in several stages - first lay out the first bar, on top of it lay a layer of insulation. Optimal material of the heater can be a tow or felt. From above the heater is covered with the second bar, performing the fixing function;
- select the method of bonding the masonry elements to each other. The simplest option is using nagels - special pins used for vertical connections. The optimal gap between the nagels is 1.5 meters, holes of this diameter are drilled for their installation so that the pin enters tightly, without gaps, and does not swing;
- it is especially necessary to make angular joints. For this purpose, a groove is cut on one of the bars, and in the joint - a spike, which exactly corresponds to the size of the groove. Comparing the spike and groove - we get a strong connection of the elements.
Of course, at first glance it seems that it is quite easy to build a second floor from a bar, however, before you start working - study the video available on the Internet about technology, materials, and the necessary tools. Remember that the thoroughness, diligence of your work depends on the comfort, quality and characteristics of the room, in which you and your family will spend a lot of time. Make the construction of the second floor really economical, and realize your building fantasies.
for additional square meters is available to everyone. A house made of timber is an excellent choice for a practical person who cares about the health of the family. After all, there is no more environmentally friendly material in the world.
if necessary?
Build the second floor of the house from a barit is possible and necessary! Very often, people want to increase the available living space, due to the increase in the family or for some other reasons, this applies to the tenants of the apartments (they remove the balconies and loggias, make the superstructures) and the residents of small houses (add additional sq.m. area of the plot), and residents of single-storey houses (finishing the second floor). Even at the brick one-storey house, recently, the second floor is built from a bar. This is due to the availability of material and ease of installation.
The second floor of the house from the timber pricefor work
If you are just now planning to build a house - I advise you to think in advance about a two-story cottage from a bar. This is especially true for a large family with a small plot of land. Often, in private two-story houses, the first floor is assigned to the kitchen, garage, bathroom, living room, pantry, and the second floor, if you can say so, more private, on the second floor there are bedrooms, study, library, billiard room, another bathroom and living room . It is possible to build a loft, balcony or terrace in a two-storey house from a bar. Speaking about the area of such a house, it will be the most functional starting from 150 sq.m., but very often for a two-storey house they stop at a size of 10 by 10 meters (200 sq.m.). In a two-story house, in my opinion, there is only one significant drawback - quite a lot of area is "eaten" by the staircase.
Is it possible to build a house of lumber and brick, and is there any sense in such a combination of building materials?
To answer this question, it is necessary to consider not so much each material separately, how many variants of combined construction, in which you can see all the advantages of this choice.
Combined construction
To begin with, it is necessary to determine the basic properties of both bricks and wood, in order to have an idea in which direction they are best used.
Properties of materials
Brick:
- Ecological compatibility. Natural components, sand, water, clay, make this material an ideal "neighbor" for humans.
- Strength. For example, double silicate brick m 150, which is often used in the construction of houses, can withstand a load of 150 kg per square meter. cm.
- Duration of operation. Here you can talk not so much about years, even as about decades and even centuries.
- Easy operation. Brick masonry can be carried out even without having certain special knowledge in construction.
- Frost resistance. High indicators allow you to build houses in any climatic zones.
To be completely objective with respect to the brick, it is necessary to note the drawbacks, which are connected, first of all with low heat-insulating qualities. If, then the wall should be 50-60 cm thick.
However, the heat of building brick is extremely difficult, so it is possible to maintain a constant temperature in the premises quite comfortably during the cold season.
Wood, beams:
- Environmentally friendly, as in the case of brick.
- Easy to use.
- Availability.
- Heat-insulating and noise-insulating properties.
Of course, there are enough minuses in the bar, however, it's a question of wood, and this is the possibility of rotting, the formation of mold, fungus, fire danger.
Types of combining
In order not to face the choice of brick or timber, it is possible to offer several construction options, where these two materials can perfectly complement each other.
Option 1
Very interesting is always a private house, the first floor of which is built of bricks, and the second of the timber.
The technical points are as follows:
- Bearing walls made of bricks have high strength, and easily perceive the load of the second floor.
- The second level can be a mansard, lightweight construction, insulated with additional heat insulation material.
Turn-based construction:
- Foundation. Typically, a tape type, and not particularly powerful, thanks to a light second floor.
- Masonry of the walls of the first floor. You can lead, this just will be enough for a thickness of 38 cm, plus, insulation with mineral wool or foam.
- Intermediate floor. Just thanks to the brick walls, you can cover the house of brick and timber with reinforced concrete slabs.
- Erection of the second floor of the timber. This can be a full-fledged floor, and a mansard version.
What are the advantages of this option? First of all, this is the rational use of the material. Show this can be an example of brickwork and brick consumption. If the second level is erected from a bar, then a brick laying in a half brick will require 10x10 - 45, 6 cubes of brick at the house, without taking into account the window openings.
Despite the fact that the price of the material is relatively low, the laying in two bricks, and even two floors, will eventually turn out to be much more expensive construction than the version of the combined house. And do not even have to make calculations on the topic, which is cheaper than a house made of timber or brick?
Advice!
To immediately have an idea of the cost of materials, it is just necessary to calculate the cubature of the house. To do this, multiply all the values of the wall: length, height and width.
Concerning the device of the second floor, the instruction for erection will require:
- Mineral wool, as a heater.
- The bar is 50x50 mm, as a crate for insulation.
- Steam insulation film.
- Siding, they will be finished if the walls are not planned to be left in kind.
To show this by example, the calculation will be conducted around the house from a bar, 8x8, and step by step will be as follows:
- The area of the walls is determined. The length of the perimeter is 8 * 4 = 32 meters, multiplied by the height of the floor - 32 * 3 = 96 meters. This is the area of the first floor.
- The total area, if the second floor is full - 96 * 2 = 192 meters square.
- On the amount of material that will require finishing with brick brusovogo house affects the number of window and doorways. Their area is calculated and subtracted from the total.
- The number of bricks per meter of cladding is calculated. For this, the length and height of the brick are taken, which are multiplied. Standard dimensions are 250 mm * 65 mm = 0.01625 sq. M. meter.
- Further one square meter of the wall is divided into 0.01625 and it turns out 61.538 or 62 bricks.
- To calculate everything accurately, the binder is included, which reduces the amount of material to 51 pieces.
- Before the brick house is bricked, the area of the windows is subtracted, this is approximately 15%, and it turns out about 150 meters, taking into account both window and door openings.
- Multiply the number of bricks per square and it turns out that the facing will require 7650 pieces of facing bricks.
Such exact calculations, firstly, allow you to understand at the cost estimate stage at which cost the facing of the house from the timber with brick will cost, and secondly it makes it possible to purchase the whole lot at once, and not to pay extra afterwards.
Important!
Often a brick from a batch that you have to buy can not match in color, and this will already be a real problem for the appearance of the building.
Course of work
It is necessary to understand that the brick lining of the house from the timber is an additional load on the foundation, so if the house was not originally erected on a strong base, it is necessary to build a base around the perimeter.
Step by step work from beginning to end look like this:
- The construction of a trench, a depth of 1.2 meters - 1.5 meters, and a width of 40 cm.
- Manufacturing of the reinforcing element, a simple rectangular construction of reinforcement with a cross section of 12 mm is used.
- Backfilling of a pillow from sand, ramming, packing reinforcement.
- Formwork device, 15-20 cm high above ground level.
- Pouring concrete.
Concrete should be left for a week, so that it completely seized, after which you can start facing yourself.
The walls are thoroughly cleaned, primed, and then you can start the main job, in which instead of a weave under the heater, flexible connections will be used.
A vapor barrier film is "put on" the wall.
- Surface of concrete is waterproofed with mastic or roofing material.
- The first row is laid out, strictly according to the level.
- In the second row a few holes are left in the half-brick.
- Between the walls should be a minimum distance of 60-100 mm.
- Mineral cotton wool is laid. For easy installation, mats can be used.
- Flexible communication is established. Through the cotton wool, a hole is drilled into the wall, a flexible connection is made, which fixes the mat and mucks in the masonry.
Important!
The fixing of the timber to the brick wall is solved, it is using flexible connections that this instantly gives the whole structure of strength and rigidity.
Flexible connections are established with a step of 50 cm horizontally and 20 cm vertically.
Masonry is carried to the roof, and under the top in the wall must remain openings, as in the second row of masonry, this is an opportunity for natural ventilation.
Conclusion
Of course, before laying a house out of a bar with a brick it is worthwhile again weighing the pros and cons. Nevertheless, it is worth to pay tribute to combining the timber and brick, with these two materials you can bring the house in perfect condition, and offer interesting constructional moments.
In the video in this article you will find additional information on this topic.