When dealing with problems of insulation during the repair of an apartment, the construction of a house, a bathhouse, other ancillary or household facilities, any owner always faces the problem of choosing the best thermal insulation materials. It's good that in our time their assortment is on sale - it is quite wide. But this variety of choices can play with an ignorant person and a "cruel joke" - it's no wonder to get lost in such abundance and make a mistake. Therefore, going to the store to buy or intending to make an online order, the consumer should already have an idea about the characteristics of the material, its features, applications and basic technological methods of installation.
This article will review the thermal insulation materials, which, although they may have different base bases, are still combined by one common important feature - the foil surface. So, we consider varieties, advantages and disadvantages, price level and practical application of heaters with foil.
Advantages and disadvantages of heaters with foil
Any of the insulation materials has its own insulation properties for the light of a foamed, porous, fluffy, fibrous or other substrate that allows the creation and maintenance of an air layer. Well, the air itself has an extremely low thermal conductivity, and in the total we get a thermal insulation layer, the transfer of heat energy through which, if not completely eliminated, is significantly reduced. It is clear that any material has its own indicators of thermal resistance, and the general possibilities of a heater depend on its thickness.
1 - mineral wool
2 - expanded polyethylene
3 - expanded polystyrene.
4 - foamed concrete.
But this, so to speak, the passive role of insulation. Is it possible to do so that the thermal insulator not only does not let heat through its structure, but also takes part more actively, reflecting the thermal energy in the right direction? It turns out that it is possible - and for this is used by foil.
The wavelength of the infrared radiation is close to that of visible light, and the heat flux, like a light ray, is able to be reflected from the mirror surface and redirected back. It is on this principle that any thermos is working - a thin glass or metal liquid flask with an internal mirror or polished surface, and an air (or vacuum) layer around.
The heat in this simple construction is very long. Precisely the same principle is also used for the warming of residential premises, bathhouses, industrial buildings and technological lines, agricultural objects, and so on. To do this, use foil insulation.
Modern technologies make it possible to apply a layer of aluminum foil to virtually any thermally insulating materials, so that the strength of the resulting multi-layer construction is maintained, without its stratification. As a result, new heaters acquire a number of remarkable qualities:
- The created "thermos effect" in the room allows much better to keep the heat in the winter, and vice versa - cool in the summer.
- Increasing the effectiveness of thermal insulation leads to a reduction in energy consumption for heating.
- The foil surface itself is a good barrier against penetration of moisture and water vapor, which in some cases allows you to do without an additional waterproofing layer.
- Foil does not reduce the thermal insulation properties of the material, on the contrary - it strengthens them and makes it possible to use insulators of much smaller thickness, which in cases of close rooms is sometimes extremely important.
- Any of the types of foil insulation is also a good noise isolator.
- The application of foil to a thermal insulator poses no threat from an environmental point of view. On the contrary, it often becomes a reinforcing boundary from the penetration of the smallest particles of material into the space of the room.
- The material is easy to assemble, for which no special skills are required. Moreover, it can, if necessary, be dismantled, and then installed on the same or another location.
- The form of the material - rolls or panels, it is very convenient for mounting works.
Among the shortcomings can be noted the following:
- Aluminum is still subject to gradual corrosion, which causes it to grow turbid, and over time its reflective qualities somewhat weaken.
- The metal layer can become very hot, and therefore, during installation, a small air gap must be provided between the heater and the finish surface finish. By the way, the same air gap will promote the ventilation of the aluminum coating, and the absence of moisture on the foil surface will greatly reduce the aggressiveness of corrosion processes and thereby increase the service life of the material.
Main types of insulation with foil
Now it is worthwhile to consider in more detail the main types of foil insulated heaters, their specific features and applications. In private construction, materials are widely used from foam polyethylene, from mineral wool or from expanded polystyrene. There are other materials, for example, basalt fiber-base plates with foil, but this material is expensive, and has a specific purpose - for thermal insulation of production lines, power plants, special industrial facilities, etc.
Foiled insulation based on foam polyethylene
This is one of the most common and easy-to-use types of foil insulation. It is a layer of foamed by special technology of polyethylene, coated with one or two layers of foil with a thickness of 10 ÷ 15 μm.
The thickness of the insulation layer can be different - from 2 to 15 mm. The form of release is usually rolls, but there may be also sheets of standardized size, which is especially characteristic of the thickest (15 mm) species.
There are three types of material:
- type A - one-sided foil;
- type B - the foil is applied on both sides, which is sometimes required to enhance the thermal insulation properties;
- a type FROM – from one side of the foil; on the other hand, a self-adhesive layer covered with a protective film, which facilitates, if necessary, the process of mounting on the ceiling or on vertical surfaces.
According to the type of source material used, there may also be differences:
- In inexpensive brands, the usual polyethylene HPE, which undergoes repeated foaming during production with the creation of a closed gas-filled porous structure. The disadvantage of this material is a low resistance to deformation loads, a property of gradual shrinkage.
- The best indicators are a heater based on specially treated, "cross-linked" polyethylene (PPE). The density is somewhat higher, but due to the transverse intermolecular bonds, it not only maintains a mechanical effect, but also seeks to recreate its original form after removing the dynamic load. When acquiring material, this nuance must be taken into account.
Some types of such insulation can additionally have in their structure a fiberglass reinforcing mesh.
You can find many names of insulation based on foam polyethylene. The certified products of the brands Penofol, Ekofol, Isoflex, Isolon, Dermaflex, Folgoizol are well-deservedly popular. Some characteristics of these materials are given in the table:
Name of material | PenoFol | Isolon | Ecofol | Isofleks |
---|---|---|---|---|
Miniature | ![]() ![]() |
|||
Coefficient of thermal conductivity, W / m × ° С | 0,049 | 0.04 | 0,049 | 0,035 |
Density, kg / m³ | 35 | 26 ÷ 33 | 33 | 35 ÷ 45 |
Heat reflectivity | not less than 90% | up to 95 ÷ 97% | not less than 80% | not less than 90% |
Operating temperature range | from -60 ° to + 100 ° С | from -80 ° to + 80 ° С | from -60 ° to + 90 ° С | from -60 ° to + 80 ° С |
Vapor permeability of the material, mg / m × h × Pa | 0,001 | 0,001 | 0,001 | 0,001 |
Form of issue | Thickness 2, 4, 5, mm with a foil layer of 14 microns, rolls 1.2 × 30 m; The thickness of 8 and 10 mm - rolls of 1.2 × 15 m | The width of the canvas is 1.5 m, the thickness is 2, 3, 4, 5, 8 and 10 mm, the length in the roll is 200, 170, 130, 100, 80 and 50 m, respectively. The individual sheets are 15 mm thick, 1500 × 2000 mm | Rolls of 1200 mm width, thickness of insulation 2, 3, 5, 8 and 10 mm, length 25 and 15 m. | Rolls with a width of 1200 mm, thickness of insulation of 2, 3, 5, 8 or 10 mm, length 25 and 15 m. The thickness of foil - 10 mkm. |
Foamed polyethylene foam is widely used in repair and construction works. Sheets or stripes of insulation are attached to the surface in any convenient way, but in such a way as to prevent a strong violation of the integrity of the foil (for example, it is permissible to fasten it with the help of staple staples). Typically, the linens are laid back to back, which is then glued with foil tape to provide a single, integral reflective and insulating surface.
- Warming of the floor. It is used as an additional or even basic (for example, in multi-storey buildings) thermo-insulating layer, which simultaneously can play the role of a waterproofing. Folds the foil part up before the flooring of the floor finish.
- Thermal insulation and additional noise insulation of walls and ceilings, especially in conditions when the size of the room does not allow the use of thicker types of insulation (a classic example - a narrow balcony or loggia). It is fixed with a foil side towards the room. It is mandatory to provide a gap between the foil and the finish coat (lining, panels, etc.). It is usually fixed on the surface by the rails of the crate (gratings), which become the basis for the cladding.
- Warming of the roof slopes. Can be used alone or in combination with other materials. In any case, the foamed polyethylene foam is fastened last to the attic space, and on top of it, with the gap observed, a casing is mounted.
- Warming of the bath. The foil layer simultaneously plays the role of a reliable waterproofing, protecting the wall material from waterlogging. True, in a steam room where there can be critical high temperatures, the use of the material is not always justified due to the limited temperature range of its operation. waste heat energy for unnecessary warming up in the outer wall, redirecting the infrared flow back to the room.
It is interesting that this material is widely used for other purposes not related to construction. So, it is great for insulation and noise insulation of car interiors. It is also used for the manufacture of warm insoles for winter shoes.
Video: comparative tests of insulation from foil foam polyethylene
Mineral cotton wool with foil
The thermal insulation properties of mineral wool are very high in themselves. But additional foil will only increase the effectiveness of insulation. In addition, this material is very hygroscopic, and an additional barrier against penetration of moisture and water vapor will not allow the mineral wool to get wet and lose its qualities.
Mineral wool insulation is produced in the form of collapsible cylinders or semi-cylinders - these products are excellent for thermal insulation of pipelines.
The heat resistance of mineral foamed cotton wool allows it to be used for additional thermal insulation of boilers, boilers, storage tanks, and other heat engineering devices.
Video: Thermal insulation baths with foil insulation «ISOVER Sauna»
Expanded polystyrene mats with foil
Not so often, but still one more type of foil insulation is used. We are talking about plates (mats) made of expanded polystyrene with aluminum foil on one side.
Such products can be produced by single mats, or rolls of several meters, sectional, like a tractor caterpillar.
The main purpose of such insulating foil materials is thermal insulation of the floors, both self-contained and in the "warm floor" system. The aluminum foil layer reflects the heat flow upwards to warm up the finish coat, so that expensive energy is not expended on the grate of the massive floor slabs or the rough floor laid on the ground.
To facilitate the process of laying the contours of the "warm floor" on most models of these mats a comfortable, well-visible marking is applied. Fixation of pipes is not particularly difficult - for this you can use special clamps with "harpoon" tips, which reliably hold the element in the thickness of expanded polystyrene.
Fastening of the pipe of the "warm floor" to the mat
Acquire better mats made from extruded polystyrene. Its increased density makes the material resistant to quite significant mechanical stresses, which is especially important for the installation of floors.
In conclusion of the review, it is necessary to make one very important observation. All listed advantages of foil insulation will be valid only if the material is of high quality. The fact is that some unscrupulous manufacturers are limited to applying a thin aluminized spraying. This is far from foil, although outwardly the materials may be similar. A thin sprayed layer is not able to adequately reflect the heat flow - infrared radiation for the most part will pass through it. And the barrier to penetration of moisture and water vapor such a "decorative" shiny layer will also not.
Without a roll and tile materials, not a single construction site can do. Currently, the construction industry, using advanced technologies, has established the production of various insulation products:
- Fiberglass;
- Stone wool;
Warming of the building or a separate apartment helps to keep the heat in cold weather and maintain a constant climate in the premises during the whole time of the year.
This saves money for the maintenance of buildings. Thermal insulation is used for building: floor, ceiling, loggias, attics.
Also, an insulator is used for buildings of various purposes - baths, a garage, a summer cottage, a barn. They are available in different thicknesses, lengths and widths.
It has been used for many years with foil glued to it. It is especially advantageous to use a heater with foil for walls.
Foiled insulation
The foil gives a reflective effect and contributes to the additional preservation of heat in the room. Each species has its own properties, which give some advantages to each in relation to others.
Foamed polyethylene has considerable strength. Therefore it is better to use it for floor insulation. Material made of stone wool withstands high temperatures.
It is well suited for chimneys, saunas, bathhouses, heating mains. In addition to the thermal insulation properties of all types of insulation is a good soundproofing material.
Thermal insulation for walls
Insulation with foil in most cases based on fiberglass. This material has a number of good qualities: good vapor barrier, low density and increased flexibility, non-flammable, environmentally friendly, does not emit smell, durable, not high price.
Still it is used for the warming of cellars, ventilation ducts, baths, loggias, mansards. With the same effect can be used for the insulation of surfaces, especially indoors, thermal insulation with foil based on rock wool and foamed polyethylene.
The choice of insulation is reduced to the selection of its thickness, depending on the design of the surface, the climatic zone and the thermal insulation properties of the selected material.
The best option for choosing a heater will be his calculation in the design institute. You can try it on your own by picking up the calculation system on the Internet.
Warming materials are made with a thickness of 10 mm to 150. Therefore, after calculation, you can build the required thickness of insulation.
Helpful information:
Mounting the insulation on the walls
Thermal insulation should be done in a warm and dry time. Before the production of these works, they must be cleaned of foreign objects, pollution, dust.
In the brick walls, it is necessary to repair cracks, chips, remove the peeling paint and plaster. After that, they must be primed and treated with an antiseptic.
To fix the insulation on wooden walls use self-tapping screws with large hats or screws with washers. The length of the screw must be greater than the thickness of the material by 15 mm.
On the brick and concrete surfaces, the insulation material is fixed with special glue solutions. Some heaters with foil for walls are produced with a self-adhesive surface.
It is necessary to remove the protective layer and glue the insulation. Inside the room, the thermal insulation is usually covered with DSP boards (cement-chip boards), followed by their final finishing with painting or wallpaper.
Outside use a plaster, then make a painting or close with siding.
Requirements for thermal insulation
Insulation with foil for walls must meet the following requirements:
- High thermal insulation properties. From this depends the effectiveness of the insulation of the walls. The thermal conductivity of rock wool is 0.039-0.041 W / (m * C), for foamed polyethylene - 0.049 W / (m * K), glass fibers - 0.037 W / (m * K);
- A light weight. This eliminates the need to strengthen the foundation. The volumetric weight of rock wool is 30-40 kg / m3, foam polyethylene - 35, glass fibers - from 28 to 60;
- Good vapor permeability. In thermal insulation based on rock wool, it is 0.3 mg / (m Pa), foamed polyethylene - 0.001, glass wool - 0.35. Water vapor permeability removes unwanted moisture from the insulation, contributes to the refusal to install powerful ventilation systems to dry rooms;
- Ease of final finishing. The warming material for the walls must be flexible enough to be easy to lay in niches and other irregularities;
- Ecological compatibility. Especially important is the property for the thermal insulation of walls in apartments, houses, kindergartens, schools and public buildings (culture houses, sports palaces, sanatoriums);
- Durability. The cheapest insulation for walls should not lose its qualities for at least 10 years;
- Insulating material for the exterior walls of the building should not absorb moisture and not lose its qualities in the cold;
- An important indicator of thermal insulation is its flammability. If the package contains the letters NG, it is not a flammable insulator and it can be used for insulation of any buildings and premises. When specifying the letters SG - slightly combustible - there are some restrictions on the application.
The correct advice:
Glue the foil material to the surface behind the heating batteries. This will increase heat dissipation of radiators and reduce heat loss.
A foil insulated heater is a relatively new material that is used for thermal insulation in industrial and civil construction. It consists of a reflective layer and a base. Basalt is used basalt cotton wool or foamed polyethylene, and for the upper reflective layer used aluminum foil or metallized film.
The foil is applied by thermal welding and polished to a reflecting coefficient of not less than 97%. Metallized film can be used in conditions of high humidity (saunas, baths).
Foiled thermal insulation has found application as a heater for enclosing constructions of structures, allowing to save on heating. It is also used for insulation of pipelines, air ducts and other utilities. It is very convenient to install. They produce a roll and sheet insulation.
The video in this article will tell you how to properly build a heater.
Properties of foil insulation
Properties of foamed polyethylene foam
The foil insulation with foam polyethylene base (Penofol) is characterized by good vapor barrier properties, which prevent the formation of condensation and excellent soundproofing qualities. It combines the thermal insulation properties of polyethylene foam, which is filled with air trapped in the microcapsules, and aluminum with its excellent reflective qualities.
- High level of thermal insulation. Due to the fact that the insulation not only keeps the heat lost due to the thermal conductivity of the structures, but also prevents its convection and radiation, it has excellent thermal insulation performance;
- Wind -, sound -, hydro - and vapor barrier. It provides not only protection against heat loss, but also serves as a good barrier to adverse effects: moisture, noise, draft. Even with a constant humidity, the heater does not lose its qualities, does not rot and does not swell. It is widely used in rooms with high humidity or under the threat of flooding;
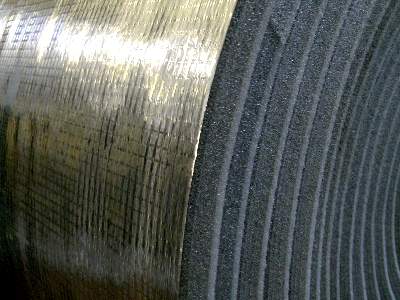
- The minimum thickness of the insulation layer is 10 mm. This will save valuable space, relieve engineering problems in the design, does not require a special partition for the heater. In addition, the compactness of the protective layer makes it convenient for transportation in rolls;
- Protection from radiation. This is practically the only insulation that can reflect radiation. This task is perfectly performed by a coating of aluminum. This property is very important for industrial and residential premises that have an increased radiation background;
- Strength. Natural qualities of the basis of polyethylene and foil are the key to the high strength of the insulation on the cut, puncture, tear or pressure. In addition, the protective layer does not interact with various building materials, paint and varnish materials;
- Security. This eco-friendly material is completely safe for humans. It is non-toxic, does not cause allergies, does not emit gases;
- Elementary installation. Install penofol on the ceiling and walls is simple enough due to the convenient format and minimum thickness. This does not require protection and cumbersome equipment. It is especially convenient to mount the material with a self-adhesive layer. This makes it possible not to use additional fastening and to save time considerably.
Properties of foil basalt wool
Foiled basalt insulation is used where additional protection against heat losses in strong winds is required.
It has the following qualities:
- fire resistance;
- resistance to chemical and biological effects;
- strength.
Basalt insulation is produced in the form of mats, cylinders, rolls, sheets.
Where to apply a heater
Foiled polyethylene is used in civil and industrial construction. It is installed together with a reflective thermal insulation or with ordinary thermal insulation. The use of foil insulation provides maximum effect in the air gap between the finishing material and the heater (1.5 - 2 cm). Without this gap, heat transfer occurs through solid bodies.
A heater with a polyethylene base is used as:
- thermal insulation for the floor;
- heat-reflecting screen behind the radiator;
- noise and heat insulation of air ducts;
- waterproofing and thermal insulation of sauna and bath;
- heat insulation of pipelines;
- hydro, noise and heat insulation for walls, roofing and attic;
Two-sided foil insulation is used to insulate the space under the roof. This will reduce the overheating of the attic in the heat (thermos effect), i.e. Keeps cool in summer and warm in winter.
Foam polyethylene ropes in the form of round profiles of continuous cross-section are used as sealants for prefabricated building fencing elements.
For surfaces of complex shape, a foil self-adhesive polyethylene with a layer of glue is used. It is used mainly for soundproofing and insulation of metal structures (garages, containers, hangars); river and sea vessels; salons and spaces under the hood of cars, refrigerators; boxes for air conditioners, exhaust and ventilation. Adhesive layer is characterized by high adhesion, guarantees the reliability of fixation and ease of installation.
The instruction on a photo - how to strengthen a heater
How to mount a heater
It is necessary to emphasize that it allows to store and reflect heat. Try to keep a distance of 25 mm between the material and the finish, and its properties will provide additional heat due to this gap. When installing the heater on the wall, fasten it to the crate between the rails. Having finished installation, joints between them should be glued with foil tape.
Instructions for the installation of insulation in the bath:
- reflecting the thermal insulation mounts directly to the ceiling and the walls of the bath with a foil-coated inside;
- steam -, hydro - and heat insulation of the bath walls are performed with the help of small nails or a construction stapler, the seams carefully glue the metallized scotch. To ensure the withdrawal of condensate at the junction of the floor and the wall make a small conclusion of the insulation sheet;
- on the reflective coating, a wooden crate with a thickness of 2-3 mm is mounted, on which the inner decoration of the steam room is mounted (lining, etc.).
Note! Which side should I put the heater on? Installation of a heater is done with a foil surface inward to reflect and preserve the heat of the room.
Installation of a heater in the bath can be done by yourself, but it's difficult to insulate the floor in a bath and it's better to entrust it to a specialist.
A comfortable temperature in a house is often provided, using porous or fibrous materials having a low thermal conductivity. However, ever increasing popularity began to acquire insulation, working on a different principle - on the reflectivity of the mirror surface. This is how foil insulation works, which today is considered the most effective.
What is thermal insulation with foil
This combined insulation, which, in addition to the base base with low thermal conductivity, has a mirror layer of a very thin, about 20-30 Å (angstrom), polished aluminum foil. This component provides the maximum effect of reflecting infrared rays, in fact, heat - up to 97%, and the base layer "takes over" the remaining 3%. Thus, the heat remains in the room.
Types of heaters
Foiled thermal insulation has a diverse form of release - in the form of rolls, mats, tiles, cylinders used mainly for pipe insulation, and dimensions. They differ in other parameters.
- The type of the base layer.
- foamed polyethylene,
- mineral or basalt wool;
- expanded polystyrene.
- Technology of foil insulation. Aluminum foil for thermal insulation can be glued or sprayed, perforated or not.
- Number of reflective layers. On some types of thermal insulation foil can be applied from one or both sides, on others there is an adhesive layer, that is, in addition, this insulation reflects, it can be laid directly on the surface without. These heaters are labeled respectively A, B and C.
On a note
Since self-adhesive foil insulation is flexible enough it can be used for laying in corners, as well as on uneven surfaces. By gluing the joints of heat insulators with foil tape, you can achieve their full tightness.
- Appointment. Thermal insulation materials with a foil coating are used both as the main thermal insulation, and additional.
For those who are going to buy insulation, we note that the price of foil insulation is formed depending on such parameters as:
- base material;
- thickness of aluminum foil;
- height of the thermal insulation layer;
- number of reflective screens.
Advantages and disadvantages
- The foil has an excellent ability to reflect the thermal radiation as much as possible. On the one hand, it keeps the heat in the room, on the other - it does not let the heat in, that is, the inside creates a "thermos effect".
- An additional layer of foil increases the wear resistance of insulation.
- It has hydrophobic properties, so in some cases it can replace the waterproofing.
- Heaters of this group have a small mass, are easily cut and installed. Moreover, if it is required, it can be dismantled and reused at the same or another location.
- They maximally isolate from external influences: they do not let the wind pass, they are resistant to critical temperatures, they significantly reduce the noise level coming from the outside, and so on.
- Such insulation serves for a long time, while it does not rot and does not become covered with mold.
- It is much thinner than conventional heaters, but it is much more efficient and allows saving energy costs to 25-30 percent.
- The foil layer not only does not create problems for human health, but also becomes a barrier to the smallest particles of the substrate that can penetrate into the space of the room.
- From the disadvantages of insulation with foil, we note the susceptibility of aluminum to gradual corrosion. The reflective layer begins to grow dull with time, which leads to some weakening of its basic reflecting qualities.
- These materials are made on the basis of foam polyethylene by special technology. The height of the insulating layer can be very different from very thin in 2 mm to relatively thick a 15 mm. As a rule, this is a foil-foamed thermal insulation. The thicker materials can be supplied in the form of sheets having a standard size.
- The thickness of the foil layer from the foil is 10 ÷ 15 microns.
- The technical and operational characteristics of the insulation also depend on the variety of the raw material:
- Inexpensive brands are made from ordinary polyethylene, subjected to a multiple process of foaming. The result is a closed porous gas-filled structure of the new material. These heaters have a significant drawback - this is the tendency to gradual shrinkage due to low resistance to mechanical stress.
- "Cross-linked" polyethylene (the so-called heaters based on PPE) has the best strength. Cross-links at the molecular level provide resistance to mechanical stress.
Their density is somewhat higher. Moreover, when the dynamic effect ceases, the material "tries" to restore the original form.
On a note
Some types of foamed polyethylene foam have an additional reinforcement layer made of fiberglass mesh.
- On the construction market a wide range of heat-insulating materials based on expanded polyethylene is presented. Among them the foamed Penofol, Isolon, Folgoizol and others are most in demand.
- Insulation sheets are laid back and fixed to the surface, for example, using a construction stepper. In principle, you can use any other method. The main thing is that at the same time, the integrity of the foil is not affected. Then the docking seams are glued with foil tape.
Spheres of use
- Used in the role of an additional or main thermal insulation layer in the installation of the floor, which in this case acts as a waterproofing. The foil part should be looked up when laying, towards the finish coat.
- Excellent cope with the thermal insulation of walls, as well as ceilings in rooms, the dimensions of which do not allow the use of thicker insulation, for example, on a narrow balcony (loggia). Fortify the material with a foil surface inside the room.
- It is used for the insulation of roofing skates as an independent material, and additional to others. And in that, and in another case, it is attached to the inside of the attic by a reflecting surface and stuffed into it with a lath under the lining.
- With his help they equip the thermal insulation of the bath. Simultaneously with the warming of the bath from the inside (ceiling, walls), the issue of steam insulation - protection of the skin from waterlogging - is also solved. For critical high temperatures, as, for example, in a steam room, such a material is not very suitable, since it is operated in a limited temperature range.
Foiled Minvata
It already has very high thermal insulation characteristics. Foiling, first, further increases the efficiency of insulation, and secondly - it is an additional way to protect hygroscopic material from penetration of excess moisture and steam, which could negatively affect its performance.
In the sale of the material comes in the form of compressed rolls, sectional or individual plates, cylinders and half-cylinders.
Application
- When the roof is insulated, the material is placed in the interstitial space sufficiently tightly to prevent the formation of cold bridges.
- The density of foil, as a rule, is sufficient, so that it is possible to carry out fastening behind the reflective layer on the staples. Joints must be glued with foil tape. This will help to ensure the effect of water vapor barrier.
- The maximum operating temperature of this material is more than 300˚, therefore it is more than any other suitable for bathing. Some experts even consider this to be its main purpose. Insulating boards or mats are placed between the guides laid in steps that are less than the width of the thermal insulation. Obligatory is the presence of air gap a 20-25 mm, which is left between the layer of thermal insulation and the cladding of walls and ceiling.
- The heat resistance of mineral wool with foil makes it possible to use it for additional insulation of boilers, boilers and other similar devices.
- Collapsible cylindrical or semi-cylindrical heat insulation materials made of foamed mineral wool are suitable for insulation of pipelines.
Foiled from foam polystyrene
This is a durable thermoplastic obtained by fusing polystyrene beads, with aluminum foil on one side. This is a strong material, resistant to significant mechanical stress and high humidity. It does not rot, it is biologically stable. It retains its characteristics in the temperature range from -180˚ to 180˚.
Material is often used when laying a warm floor. To facilitate this process, marking is applied to the plates in the factory. When laying insulation, the foil layer reflects the heat flow upwards, warming the finish coat.
With the onset of cold weather, it is important to keep the heat inside each of the rooms correctly.
And here it is important to choose the right type of insulation with the presence of a foil layer.
Technical advantages of a thermal insulation material with a foil layer
Applied insulation with the presence of a special layer of foil allows better protection of any of the surfaces, reflecting the appropriate amount of heat and not giving it the ability to penetrate outside.
And here it is important to distinguish separate advantages, namely:
- increased capacity of the material with foil to reflect heat to 95 percent of the total;
- quality waterproofing, since the foil material is capable of retaining moisture;
- excellent characteristics for wind protection of walls, since this material does not intend to winter and does not dry up in the summer;
- a qualitative variant of noise insulation, as the resulting insulation with the presence of foil additionally absorbs incoming noise;
- shiny insulation - it is environmentally friendly material, safe for use in decoration;
- has a high durability, if it is properly mounted and does not have a wrong side to the heated elements, which can damage the insulation layer;
- for the floor creates an excellent decisi against decay and the accumulation of moisture from outside or docking areas with a concrete floor base.
These technical characteristics allow using this kind of solution in modern private houses with any kind of structures and load-bearing elements, placing the insulation on the entire surface of the room. Combining the tightness of the docking points and the tight fit to the supporting structures, it performs a mirror function for the transfer of heat.
Material Characteristics
Each species must be placed using appropriate technical solutions. And that's why there are requirements for using the docking of individual types of insulation with the presence of foil.
Foamed polyethylene
The roll material used is well used for finishing walls and floors. It features high strength and lightness.
Also, its parameters will not reduce the amount of living space and perform all the tasks for fixing, without resorting to additional technical solutions, and using a simple construction stapler.
The resulting foam is the basis for the inner side and the reflective surface of the material. It is also very convenient to lay, making the division into sections and corresponding floor areas.
Take into account: place this heater with an aluminum side to the inside of the building and the room. Due to this, the heat reflection will function.
Mineral basalt wool
This type of insulation should be stacked in a similar way, as the previous one, by properly placing a layer of foil and mineral wool.
The use of such insulation has a dangerous effect on the human body. Therefore, when working with it, respirators and special protective suits are used.
Recently, great popularity is gaining, which excludes this effect on the human body. In this case, the material does not burn and is not prone to drying out.
Foamed polystyrene
The material used is a kind of foam, which is located in the form of plates, and its installation is carried out not with the spreading of the rolls, but with an accurate layout along the perimeter of the insulated section of walls or floor.
For sealing, an additional foil self-adhesive tape is used. It ensures the integrity of the system being created. The connection is made at the expense of one adhesive side.
Nuances of fastening and installation
Each type of insulation should be attached to the side that has the foil inside the building.
This allows you to reflect the heat inside the room. But the available cotton wool or foamed polystyrene can not be inside.
Note: if you use a foilized version of the building's insulation, the insulation layer will be thinner. Due to this insulation will eat less of the residential area of the entire building.
All versions of the insulation must fit tightly to the bearing structures, but not shrink and have the ability to pass air. In case it is used, its installation should be carried out and with propenivaniem places of joining of separate plates.
The type of insulation, which is used as a spray, can be supplemented with a roll option of thermal insulation with the presence of a layer of foil. But this type of solution can only be applied to sections of walls and floor.
But in quality or a roof it is better to use or plate. It is more easily fixed on existing structures.
Such as neoprene, capable of creating additional protection against the arising noise. It is an actual solution for roof insulation with metal roofing.
The resulting plate will reliably absorb noise from falling rain and wind. And the applied adhesive composition for fixing will create the required sealant between the individual places of joining the roll material.
Also, on its basis, the procedure for additional insulation of the ceiling can be performed. Connecting to the surface of the rough floor or placed lags, the heater will create a single structure. This is in case there is a cold attic.
Subtleties of the insulation joint with the foil base
It is important to properly glue and join, as a roll, and slab insulation. After all, the usual building adhesive and glue are unsuitable.
It will be necessary to have a special version of foil tape, with the presence of an adhesive base. Then the thermal insulation and all the installation performed will be carried out correctly.
Such solutions are very relevant for a modern frame house or are applicable in a wooden house. The combination of special criteria in the layered arrangement with the possibility of overlapping the cold bridges makes the application of the heater more practical.
See the video in which the expert clearly explains how to properly strengthen the foil insulation behind the battery: