Monolithic house by strength is superior to all other types of buildings. In the past, only industrial facilities and high-rise buildings were built in a monolithic way, today people often use this technology for building cottages and houses.
The system for calculating the mass of a monolithic concrete slab.
The house, built on monolithic technology, allows you to embody the most incredible design ideas in life.
And increasingly, future homeowners are thinking about how to build a monolithic house with their own hands. Such construction is becoming more popular also because the house, made by own hands on such technology, is surprisingly durable. It can withstand a small earthquake, does not require much labor and expensive materials, is durable and reliable in operation. A monolithic house can be finished with anything, and walls can be erected immediately equipped with additional insulation. Technology, which uses non-removable, it allows.
Scheme reinforcement of concrete overlap.
This technology, like any other, has its drawbacks and advantages. And the merits are very significant:
- Integrity monolithic design greatly increases the mechanical strength of the construction. They are resistant to damage caused by rinses, earthquakes and earth movements.
- There are no so-called cold bridges, which are in ordinary buildings from constructions with seams. This makes the premises warmer.
- Monolithic construction can be made at any time and on any ground.
- Quite fast construction.
- Low financial costs.
- Projects of monolithic buildings can have curvilinearity.
- If perlite, sawdust, slag, expanded clay and the like are used in concrete solutions, the construction will be light enough not to make a heavy foundation under it.
- Additional insulation will not be necessary in the construction with a non-removable. And the total thickness of the wall will be less than usual;
- Monolithic walls have an exceptional sound insulation.
- Intermediate floor can be made of any material.
- This technology eliminates the appearance of cracks in the walls due to uniform shrinkage of the building.
And about the disadvantages of monolithic construction - they are much smaller:
- on the upper floors of the constructed structures, you can not do without a mortar pump or a concrete pump;
- monolithic slabs require multiple labor costs, since special scaffolding is needed;
- when the formwork is not removable, it is required to equip the house with intake and exhaust ventilation, otherwise humidity and consequences from it can not be avoided;
- obligatory plastering in order to avoid possible negative consequences from its burning - release of toxic substances;
- mandatory earthing of the whole building, since it is reinforced reinforced concrete.
Construction technology
Scheme of a monolithic-concrete ribbon foundation with reinforcement
As already understood from the above, the technology of erection in a monolithic way can be produced with different formwork: removable and non-removable. Both types of construction have their own nuances and features both in construction itself and in operation.
Removable is individual for each project. Its task is to accurately repeat all the features and curves of the future structure. More often used plywood, wood, iron or plastic.
The distance between the walls is the width of the future wall. And it is calculated taking into account the region of construction and thermal conductivity of the concrete mix used. Shields are fastened with nuts, pins, washers. To facilitate removal after filling, threaded studs are fitted with corrugated tubes to protect them from contact with the concrete mixture.
This technology allows you to pour into your formwork not only ordinary concrete, but also mixtures with less thermal conductivity: perlite concrete, expanded clay concrete, cinder concrete, aerated concrete, aerated concrete, aerated concrete, arbolite and others. Such walls will be more vapor-permeable and warm, but loads can withstand less.
A very important point in monolithic construction is reinforcement. For it, steel or plastic reinforcing meshes are used, and for an even greater strength an reinforcement frame is made.
At a time, you can pour concrete no more than half a meter. And continue the pouring is allowed only after it is grasped. Concrete is necessarily harnessed with deep vibrators, with special attention paid to the corners. After the hardening of concrete, the formwork is lifted higher, and the work continues this way until the entire structure is filled to the roof.
Finishing and warming of the walls can be done by hand not earlier than 4-5 weeks after the maximum strength. Warming is made with mineral wool, expanded polystyrene, warm plaster or extruded polystyrene foam.
Sometimes self-insulation is made with the help of a well facade. In this case, the indentation from the concrete wall is made and the wall is made of brick or tile, and the indentation is covered with eco-wool, expanded clay or other insulation material.
Advantages of non-removable
The scheme of the device of the partition from the foam blocks.
The form can be different. There are longitudinal, angular, window-sills, nadkonnye and others. At its core, the arrangement resembles the collection of structures from a children's play set.
Fixed formwork is more popular because it is also an insulating layer, while overall labor costs are reduced and there is no need to spend money on a heater for walls.
After the foundation is equipped with a waterproofing layer, a formwork made of expanded polystyrene is installed on it, fastened with special profiles, which have the form of a "spike-groove" fastening, allowing the concrete to be poured without leakage and without sagging in the bonding points.
Scheme of reinforcement of slabs.
The width of expanded polystyrene can be different. And with a large number of them, they can be manufactured in the factory by order. The standard width of the block is 150 mm, with polystyrene walls 5-7.5 cm.
This fully meets the requirements for which the heating will have to be turned on only when on the street it will be below +5 degrees.
To fill the non-removable formwork, you can not use warm mixes - just ordinary concrete. The thing is that the vapor permeability of warm mixes is sensitive above the vapor permeability of expanded polystyrene, this neighborhood will lead to condensation and the house will become fungi and moldy.
After the construction of walls with a non-removable formwork they do not need to be insulated, it will be sufficient to apply decorative plaster or siding with siding.
Kinds
During the installation of the frame, boards are used. The foundation must be wider than the future walls by at least 20 cm.
In the application, several types are distinguished: formwork of foundation, overlapping, annular walls with the possibility of changing the radius, tunnel formwork. Thus, any element of the building structure can be manufactured.
Constructing different elements in the same way is impossible. For example, for horizontal supports and mowing, formwork is installed, the walls are made using building locks, brackets and racks. And for the flooring, the formwork is laid on the structure from retaining space columns or telescopic racks.
Removable can be built of steel, plastic and wood. If we build a plywood molding, then it must be cut with a saw with small denticles, in order not to damage the lamination and veneer. The holes are drilled from the two sides for the same reason. Keep plywood formwork in a dry place. In order for the removable formwork to be conveniently removed, not only special fasteners are made for it, but also treated with a solution specially designed for this.
Tools and technology
To build a house on your own using monolithic technology, you will need the following:
- concrete mixer, mixer;
- at manual preparation of a concrete mix utensils for its kneading, shovels, measuring utensils are required;
- stretchers for transferring a concrete mix or wheelbarrow;
- gas cutter, building hair dryer;
- reinforcing mesh;
- scissors for cutting mesh, pliers or other similar devices;
- a knife for cutting expanded polystyrene;
- hammer, nails;
- roulette, water building level;
- machine for making the grid a special shape;
- metal and wooden props;
- reinforcing hook for wire mating;
- perforator;
- individual protection means.
The monolithic technology of building a house with your own hands allows you to completely dispense with additional building materials, except for those that are required to make a mixture for pouring into the formwork.
One of the variants of the base is a floating monolithic slab. It can be either shallow or not deepened type. Such a foundation is not suitable for projects that provide a basement. This disadvantage is compensated by the affordable price and the possibility of building a monolithic foundation on problem soils, since it qualitatively distributes and transfers the combined loads to the soil.
Different types of foundation slabs
There are three types of monolithic slabs:
- simple pillow without stiffeners;
- plate with simple stiffeners;
- plate with reinforced stiffeners.
There are combinations of these options, for example, the foundation of tape-plate. It is applied if it is necessary to equip the basement. A popular solution is a plate with stiffeners. It has maximum strength.
Monolithic slab is made with the use of continuous reinforcement. Its thickness depends on the planned building, and ranges from 25 to 55 cm. The use of a shallow version of the slab gives a material saving of up to 35-40%.
For the construction of a reliable foundation it is necessary to use only a high-quality concrete mix and reinforcement.
When constructing a monolithic slab, one should adhere to building rules and norms. Almost all problems with frame structures occur due to miscalculations or errors during the installation of the foundation.
Advantages of a monolithic slab as a base are:
- the construction budget is lower than analogues;
- simplicity of building a monolithic foundation;
- ability to withstand high loads due to large contact area;
- no deformation of the walls, as the plate rises and falls evenly;
- savings in finishing works, the stove is a ready-made rough floor;
- possibility of erection on problem soils.
Literature on regulations and rules
To learn how to fill a monolithic slab with a long life, it is not superfluous to read and take into account the requirements:
- SNiP in the section "foundations of buildings and buildings";
- GOST "classification of soils";
- a set of rules for the erection of reinforced concrete and concrete structures.
Stages of preliminary work
From the very beginning it is necessary to carry out such work:
- geological survey of the site - to measure elevations and determine the type of soil;
- remove the soil layer on the foundation site and deepen the foundation pit to the calculated depth;
- lay the necessary communications or bookmarks for them;
- lay drainage system;
- arrange a pillow of sand and rubble;
- lay a waterproofing foundation foundation;
- mount the formwork;
- to build a power frame made of reinforcement with a cross section of 12-14 mm, welded or bound with a special wire.
Carry out other work, if necessary. To strengthen the structure and stabilize the geometry, it is necessary to provide stiffeners in the lower part of the plate.
Rules for pouring a monolithic slab
Standard filling of the foundation plate is carried out in one step. But sometimes you have to do it in several ways. To do this, select the part that will be poured to full height, and fence it with a vertical partition at an angle to the horizon, so that the resulting seam is slanted.
Contractors consider it wrong to fill the monolithic foundation of the house in parts. But for independent work it is completely permissible.
Selection of brand and class of concrete
Before pouring a monolithic foundation plate, you need to place a concrete order from a reliable supplier. For a monolithic base, you need to choose a concrete that meets these requirements:
- density of the mixture from 1850 to 2400 kg / m³;
- brand of concrete from M200 and more;
- class of concrete from B-15 and above.
In the middle zone, 250 grade concrete of concrete, strength 230 kg / cm², frost resistance F200, water permeability W4 and mobility P3 is suitable.
The frost resistance of concrete depends on the presence of pores in the concrete structure. During crystallization, water expands and fills them, preventing cracking.
When the mixture itself is made, it is necessary to adhere to the technology of preparing concrete with frost resistance from F100 to F150.
Depending on the planned structure and type of soil, it is recommended to choose such concrete grades for pouring a monolithic foundation plate:
- M400 - for heavy buildings of brick or concrete, on weak soils;
- M350 - for 2 - 3 storey buildings of lightweight materials, for example, from foam concrete;
- M250 - for wooden houses;
- M200 - for houses built using wireframe technology.
When the mixture itself is made for the concrete casting of the slab, the proportions of rubble / sand / cement are used as 3: 1, 5: 1.
Important aspects of building a foundation
When building monolithic foundation plates with their own hands, there are recommendations that make it possible to maximize the service life. They concern some stages of work and design features:
- The recommended concrete delivery height from the concrete mixer is no more than one meter. Avoid moving concrete for a distance of more than two meters. Rearrange the concrete mixer around the perimeter or use a concrete pump to fill the entire area.
- The total thickness of the concreting layer is selected at the design stage, depending on the future structure.
- The formwork height is set above the plate level by 5-10 cm.
To increase the bearing capacity of the base, the following methods are used:
- arrangement of stiffeners occurs along the entire perimeter and, additionally, perpendicular to the long wall;
- the additional piles are equipped at the interfaces (corners of the building).
The design with piles is called pile-slab foundation.
For a visual representation of the main stages of the arrangement, you can see the video on the construction of the basement monolithic slab.
Nuances of reinforcement of a monolithic plate
When pouring the foundation, remember that all metal elements of the power frame must be covered with a layer of concrete not less than 15 mm. For convenience, under the frame from below put special holders 15-20 mm thick. It is not recommended to use such supports from wood, reinforcement or rubble. The upper power frame is fixed to the vertical pieces of the reinforcement by welding or binding wire. When leveling and distributing the mixture, you can not walk on the reinforcement so as not to disturb their structure. To distribute the load, use shields or boards, removing them as they fill.
The monolithic slab can be buried 30-40 cm, be level with the ground level or above the ground.
Features of the arrangement in winter
At minus temperature the cost of the arrangement will increase, since the mixture must be heated for three days. Heating takes place with the help of heating cable, incorporated in the power frame. It remains inside the structure. In addition, the following methods are used:
- creating a thermos - the foundation is covered with a film and the heat generated from the reaction of cement and water is preserved;
- arrangement of warm formwork - steel shields, which are heated by electricity;
- admixing to the concrete of accelerators of solidification, hydration.
The latter method is cheaper and is used more often.
Care of the foundation in the process of solidification
After pouring the monolithic slab, care must be taken. Since the cooker is a finished rough floor, it should be made as flat as possible. Work to care for "maturing" concrete:
- Control of formwork. Its displacement is not allowed. If detected, remove within an hour.
- Protection from natural phenomena. Organized shelter with polyethylene - this will help with wind and various precipitation.
- Drying control. After 8-10 hours, the humidity should not drop below 90%. Watering the plates is carried out within 3-5 days.
To build on such a foundation, you can start after 2 days at a temperature of 25-30 degrees, after 5-7 days at a temperature of 15-20. In winter, start building better on the 10th day. You can remove the formwork about a week after the end of pouring.
Important! At all stages of building construction, a responsible approach must be applied. Then the constructed construction will serve for many years.
Conclusion
If we adhere to the necessary technologies and norms for the installation of the formwork, the manufacture of concrete and its pouring, and also carry out the subsequent care for the "maturing" foundation, this will provide the necessary foundation properties and maximum service life.
In practice, several foundation designs are used in construction. One of the most common is a monolithic one. In fact, it is a reinforced concrete monolithic slab, laid down to some depth in the ground.
Its difference from other types of grounds lies in the fact that when a groundwater rises or deforms the soil layers, a monolith placed under the structure will react to changes entirely, that is, with the whole mass. Such a reaction will not lead to deformation at home.
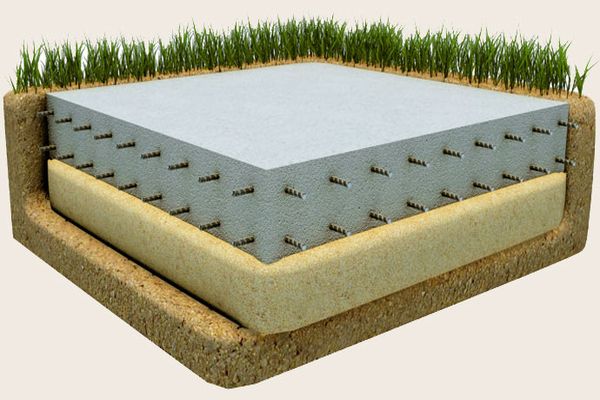
Monolithic slab can be given any shape that will completely repeat the shape of the house. And the most important thing is that such a construction of the base of the building ensures complete tightness, since there are no structural joints, and the concrete itself is made using water repellent additives.
In addition to obvious advantages, there are some disadvantages in the monolithic design. To them it is possible to carry the big expenses of time necessary for its construction. To fill the slab itself, a considerable amount of concrete and special equipment will be required.
As already noted, a monolithic foundation is a slab laid in a pre-prepared place. But, nevertheless, there are several ways of making such a foundation. Between them they differ in the options of hydro and thermal insulation. As you know, belt monolithic foundation - it's a little different. There, the earth is excavated only under the foundation, if there is no basement, and under the space of rooms the earth remains. Here the entire volume of land is excavated, under the entire area of the house.
The simplest of such foundations is performed according to the following scheme:
At the bottom of the foundation pit, a pre-compacted sand cushion is fitted with a reinforcement structure and then poured with concrete. To more complex are the structures in which sheets of waterproofing material, geotextiles are used, in addition, depending on the type of soil, it is possible to manufacture an additional cushion of crushed stone.
The most complex monolithic foundation looks like a sandwich in the section:
- sand cushion;
- a layer of geotextile;
- a layer of rubble;
- a layer of concrete so-called preparatory;
- a layer of waterproofing;
- solid plate.
Sometimes, in order to improve the reliability of foundation protection, before laying concrete, polystyrene sheets are laid, thus, the foundation insulation improves.
Such complex structures are used on complex soils, for example, with a high level of groundwater. Builders with extensive experience say that a monolithic foundation can be used up to peat bogs.
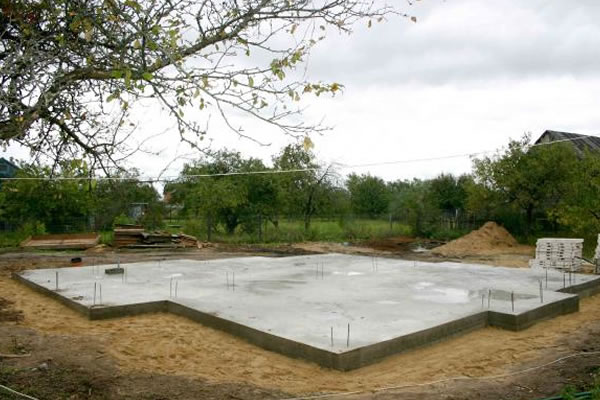
For the calculation of a solid foundation slab you should know:
- Level of location of groundwater;
- Parameters of the soil on which the foundation will be placed;
- The amount of freezing of the soil;
- The total weight of the building, it includes the weight of the box, the roof, the furniture installed in it, household appliances and occupants;
- The size of the snow and wind load;
- Weight of the plate itself.
As a result of the calculations of the given parameters, it is possible to determine what pressure the whole structure will have on the ground. Then it is necessary to apply to SNiP 2.02.01-83 and determine the maximum ground pressure at the site of the structure. Let's consider an example:
- The weight of the building is 19 tons;
- The weight of the roof is 3 tons;
- The weight of the base plate is 20 tons.
The possible snow and wind load will add 7.5 tons from above, total total load is 49.5 tons.
With the size of the building 6x6 meters, the surface area of the foundation will be 36 square meters or 360,000 square centimeters. Load on the ground will be the difference between the weight of the structure and the area of the foundation as a result, we obtain 0.13 kg per square meter. centimeter. This load is permissible for any soil.
When calculating the thickness of a monolith, it is necessary to take into account the following parameters:
- Distance between layers of the reinforcing mesh;
- The height of the concrete layer on and under the end layers of the reinforcing mesh;
- Dimensions of reinforcement.
Practice shows that the traditional thickness of the slab is 200-300 millimeters. If you consider that under it there should be a compacted sand cushion up to 300 mm in height, the total thickness is 600 mm. It must be understood that this parameter varies depending on the type of soil, the weight of the building.
In addition, the force calculation of the design must calculate the amount of consumables and fittings.
The volume of concrete is equal to the product of the perimeter of the foundation to its height, just the same amount of sand or gravel is considered. Based on the calculations carried out, it will be known and the required amount of waterproofing, reinforcement, etc.
Immediate construction of a monolithic base
Phase I. Preparation of the site
Preparatory work for the construction of a monolithic foundation begins with the cleaning of the surface of the building site. With it, remove all unnecessary, including the turf, which is the grass cover. After that, you can mark up the future pit. It is advisable to start marking with a wall that will be parallel to the fence.
For marking, you will need a cord that does not stretch, several pegs. If you do not have special geodetic tools used for marking, you can do it yourself. It is necessary to prepare several lengths of cord in advance, their length should be equal to the length of the wall and the allowance for fixing it on the peg.
After using the cord and the pegs driven into the ground, the first wall is marked, it is necessary to tie one of the ends of the cord to one of the ends, which will designate the second wall. For education between them, the developer must solve the Pythagorean Theorem, this will reveal the length of the diagonal between the walls.
Moving the cords you need to build a rectangular triangle. Once it is built, you can start marking the remaining walls. The result is a rectangle that indicates the location of the future foundation. Checking the quality of the layout can be quite simple. It is necessary to measure the diagonals, if everything is correctly marked, then their dimensions will coincide.
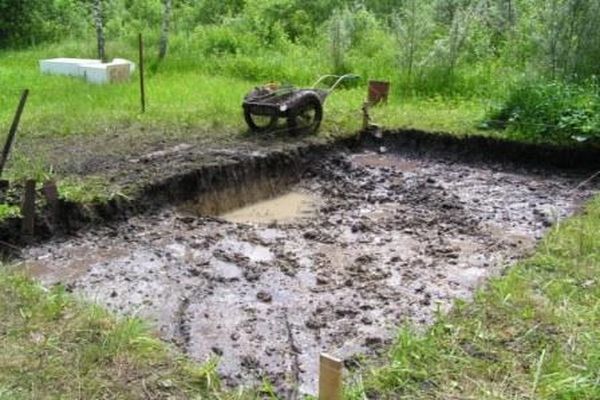
After the end of the marking, earthworks begin. The main requirement to the quality of their performance are as follows - the bottom of the foundation pit must be located strictly in the horizontal, look at the photo.
This determines the quality of the erected foundation. If you consider that the depth of the excavation lies within 1 meter, then the developer has a choice, to dig it manually or to invite special equipment. In any case, after the main volume of soil has been removed from the foundation pit, it is necessary to level the bottom and, as it is found, remove all unnecessary from it.
After the pit is ready, it is necessary to arrange a pillow, as already noted above, it can be made of sand or small gravel. The height of the pillow is up to 300 mm, after tamping.
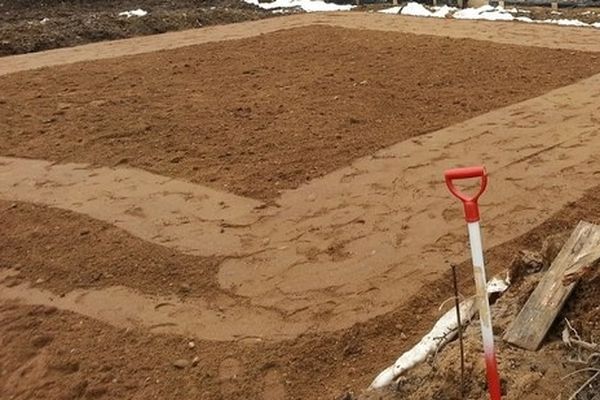
By the way, before you start to fill the sand, it is desirable to lay geotextile on the bottom of the excavation, it will prevent the penetration of sand into the surface of the soil. For this operation, it is advisable to use a special vibratory rammer.
As the sand is compacted, it is necessary to constantly pour fresh sand and continue to ram it until the desired height of the pillow is reached. The surface of the pillow should be located in the horizontal plane.
Stage III. Installation of formwork
Any work related to the manufacture of reinforced concrete structures, one way or another, is associated with the arrangement of the formwork. The simplest formwork is the wooden shields knocked out of the boards. The boards are attached to vertical bars.
These boards should be installed vertically and fixed with wooden braces, resting on a peg, driven into the ground. The step between them is about 1 meter. But practice shows that the more often they are driven into the ground, the formwork will be stronger.
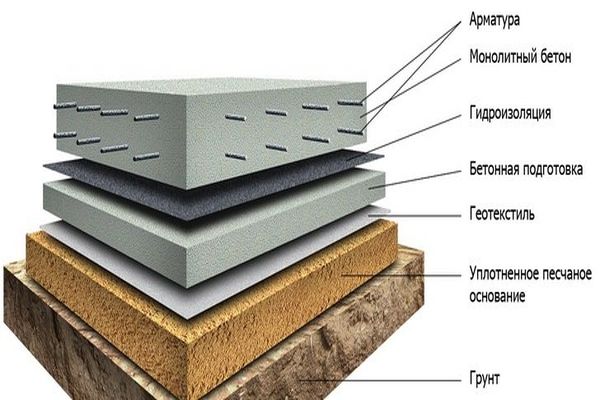
A full monolithic foundation is advisable to protect from moisture and ensure its thermal insulation. To achieve waterproofing, an ordinary roofing felt is used, which is laid in two layers or on the surface of the pillow, if a simple monolith is being built, or laid before pouring on a layer of intermediate concrete.
Thermal insulation of the foundation, if necessary, is constructed of expanded polystyrene. The layer of insulation is laid in front of a layer of concrete and on top of it is laid a polyethylene film.
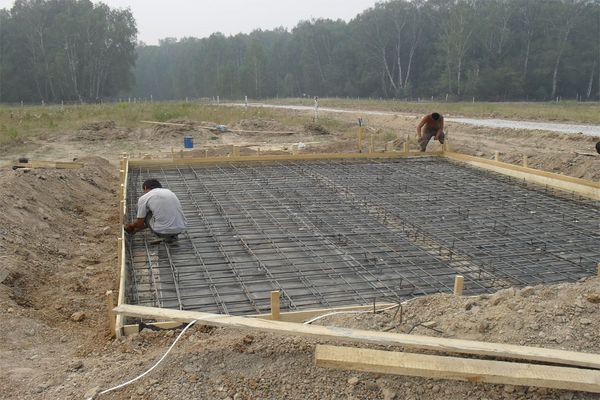
The reinforcement structure is made on a sand cushion. It consists of two belts. For reinforcement, reinforcement mesh may be used, but this applies only to foundations for small structures, for example, a bath.
For the construction of a full foundation it is advisable to use corrugated reinforcement with a diameter of 10 mm or more.
For vertical rods it is permissible to use a smooth reinforcement with a diameter of 8 mm. It is necessary to remember, the heavier the building, the bigger the diameter of the reinforcing bars.
Vertical reinforcement is driven in steps of 200-300 mm, over the entire area of concrete poured. The lower layer of the reinforcement should be located at a distance of about 50 mm from the surface of the cushion, and the top layer at a distance of 50 mm from the foundation surface. The fittings are connected together by a knitting wire or plastic collars.
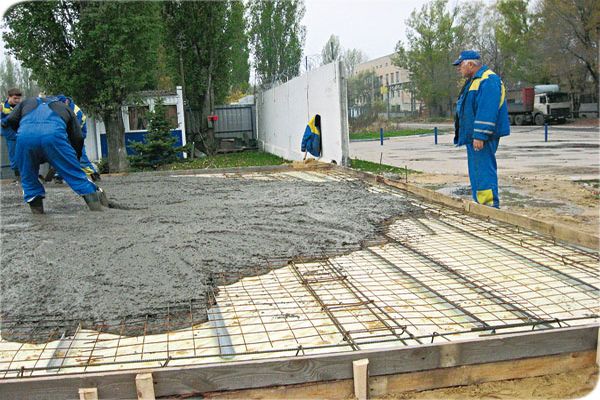
Pouring the foundation, in fact, this is the finish operation, and experience suggests that it is advisable to order concrete at a nearby factory and deliver it with a mixer. Thus, it will be possible to conduct a fill from several points, and even to level it up will be much easier. However, it must always be remembered that the concrete to be poured must be compacted. To do this, you can use special vibrators, submersible or surface.
Video
Watch a video about building a monolithic basement under the house with your own hands.